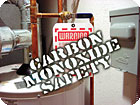
Is heating equipment and the way we install it really as safe as it should be? Every week during the winter the media publishes articles about someone getting ill, dying, or being rushed to the hospital because of carbon monoxide poisoning. We hear about buildings being evacuated due to “mysterious carbon monoxide leaks.” Typically, the fire department places blame for these disasters on defective or faulty chimneys or flues. But is fixing the flue the solution to the problem or does it just cover up the symptoms?
This spring and summer we read of birds’ nests restricting vents causing CO poisoning inside buildings. I have nothing against birds and realize it is their job to build nests and lay eggs. But when this happens in chimneys, it can jeopardize the health and lives of people. When incidents of CO poisoning are reported due to birds’ nests in flues, the first question that should really be asked is “Why was the equipment still running with the vent plugged?”
In addition to bird nests blocking chimneys, there are also situations where mortar or bricks have come loose or the metal chimney corroded and collapsed but the equipment still continued to run. Would you consider this equipment or installation safe enough for your customer?
Another cause of CO poisoning that has occurred during the winter is snow drifting and covering vent pipes on higher-efficiency equipment that is sidewall vented. Once again the question should be asked, “Why did the equipment continue to operate with the vent pipe plugged?” Shouldn’t the equipment shut down under this condition?
AUTOMATIC SHUTOFF
Fortunately there are many more situations that don’t make the 6 o’clock news because an alert contractor discovered the bird’s nest, or collapsed or blocked chimney before anyone realized there was a problem or symptoms became severe. What always seems strange to me is that in many cases the equipment involved had been functioning unsafely for quite some time. No one noticed the problem because the equipment didn’t shut off or create a no-heat situation.The contractor or contractors in the cases above potentially saved a family’s life. The contractor may feel somewhat like a hero or at least feel the satisfaction that the discovery prevented a possible disaster. But the big question is: Was the real problem addressed and repaired or was only the symptom treated?
First off, why was there a bird’s nest in the chimney? Doesn’t CO kill birds? Wouldn’t the heat of the flue gases cook the bird? Second, why is the chimney corroded or collapsed? It seems so simple to blame the chimney or a bird, or even the weather and go about our business.
In reality, it was probably the original installation, poor setup of the equipment, or mechanical room interference at fault. The fact that the equipment kept running should make us realize some important additional safety issues need our attention.
Obviously, if a vent pipe becomes covered with snow, there may not be much we can do. Nature causes extreme conditions that come and go constantly. Sometimes we can’t install sidewall vents any higher and we certainly can’t control the weather.
But if we do sidewall vent, aren’t there additional things we could do to minimize some potential hazards? Certainly advising the homeowners of the potential problem so they could keep the snow cleared around the vent would be one simple step unless it happens when they are sleeping. There has to be more we can do!
POOR VENTING
But what about the cases where the chimneys or vents are not blocked and the appliance is still not venting properly? In these situations, after there is an incident, it will be reported as another mysterious CO leak. Needless to say, there are many of these just waiting to happen, when in fact, we could do something now to prevent it.Usually when the chimney or vent is not restricted or blocked the cause is just reported as “vented improperly.” Once in a while the problem will be listed as the chimney was too big.
Unfortunately this is just another situation where the appliance is not venting properly because of possible environmental conditions, but somehow the chimney will be blamed regardless. But as usual, no thought will be given to why the equipment was still running.
The typical response is to remove the restriction, repair the chimney, reconfigure the chimney, or install a liner, or maybe raise the vent higher off the ground if it is a sidewall vent. Maybe we add a little more combustion air or lower the gas pressure so the appliance will make less CO when it does spill.
If the customer really wants to be extra safe, we recommend they buy a CO alarm. Are we really demonstrating our technical expertise and diagnostic skills in these situations or have we fallen short in providing the customer maximum safety?

Most CO detectors sold in retail stores don’t register at
low levels of CO detection. This monitor offered by National Comfort Institute
detects levels as low as 15 ppm, a level that can actually cause illness.
WHAT'S THE SOLUTION?
Doesn’t it seem logical that anytime an appliance is not venting properly there should be a safety on it to shut it down? Shouldn’t all appliances have some type of adequate temperature-activated spill switches on the drafthood, barometric damper, or flue, or in some cases near the burner that sense heat is going the wrong way? What about air proving switches?Air proving switches only measure pressure or flow but cannot quantify flue gases. And if equipment does have some sort of spill switch that comes standard, does it actually sense all unsafe conditions that can occur in the field? Apparently not.
If we added more safety switches to cover all possibilities, wouldn’t we cause more nuisance calls? In my opinion, safety should never be considered a nuisance. Although industry standards state that it is OK for vented appliances to spill for several minutes after the burner comes on, this has been proven in the field to be totally unacceptable, unsafe, and very preventable!
Today there are hundreds of thousands of existing vented appliances in all types of buildings that will continue to operate when they are not venting properly, regardless of whether the flue is plugged or not. Even though manufacturers are making equipment safer today than ever, they have no way of addressing every condition that can occur in the field.
ONE SYSTEM AT A TIME
In the end, it is the installer or service technician that is exposed to real-world conditions. And each of us must take the responsibility of providing maximum customer safety in all installations. Unfortunately, this is currently accomplished one incident at a time instead of one system at a time.Additional safety devices need to be added to make equipment as fail-safe as possible. Just because the equipment doesn’t come with a particular factory safety device to handle all spillage problems does not mean it is not necessary, or that we can’t field install one. Hopefully, we have the technical expertise to recognize potentially unsafe situations and correct them.
Additional safeties should never interfere with existing safety circuits, but instead should complement them. But remember that safeties only warn of impending dangers and do not eliminate the need to correct venting problems.
ONE LAST THOUGHT
You may think your customers don’t have any type of venting problems. Any time you see rust on burners, heat exchangers, drafthoods, or flues, you have venting issues. These are accidents waiting to happen and must be corrected. Also, if you see a white powder-like residue on the flue pipes, drafthoods, heat exchangers, burners etc., you have venting issues. Don’t overlook these telltale signs of potential danger to your customers.In Part II of this article I will deal with several other possible safety issues on vented appliances that need to be discussed and not necessarily carbon monoxide poisoning.
Publication date:09/10/2007