
This article and its companion,Considerations When Selecting a Condensing Economizer(to be published in the Dec. 17, 2007 online issue), provide information about these efficiency improvements.
A conventional feedwater economizer reduces steam boiler fuel requirements by transferring heat from the flue gas to the boiler feedwater. For natural gas-fired boilers, the lowest temperature to which flue gas can be cooled is about 250°F to prevent condensation and possible stack or stack liner corrosion.
The condensing economizer improves waste heat recovery by cooling the flue gas below its dew point, which is about 135°F for products of combustion of natural gas. The economizer reclaims both sensible heat from the flue gas and latent heat by condensing flue gas water vapor (see Table 1). All hydrocarbon fuels release significant quantities of water vapor as a combustion byproduct. The equation below shows the reactants and combustion products for the stoichiometric combustion in air of methane (CH4), the primary constituent of natural gas. When one molecule of methane is burned, it produces two molecules of water vapor. When moles are converted to pound/mole, we find that every pound of methane fuel combusted produces 2.25 lb of water vapor, which is about 12 percent of the total exhaust by weight.
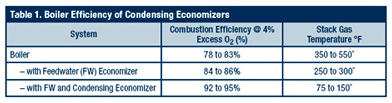
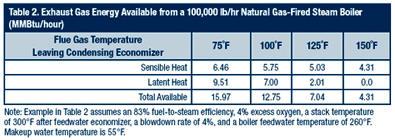
ENERGY SAVINGS POTENTIAL
The available heat in a boiler’s exhaust gases is dependent upon the hydrogen content of the fuel, the fuel firing rate, the percent of excess oxygen in the flue gases, and the stack gas temperature.Consider a natural gas-fired boiler that produces 100,000 lb/hr of 100-psig saturated steam. At 83 percent efficiency, the boiler firing rate is about 116 MMBtu/hr. At its full firing rate, the boiler consumes over 4,860 lb of natural gas each hour while exhausting 10,938 lb of high temperature water vapor each hour. The water vapor in the flue gas contains over 10.6 MMBtu/hr of latent heat. As shown in Table 2, the total heat actually available for recovery is strongly dependent upon the stack gas temperature at the condensing economizer outlet.
Assume that an indirect contact condensing economizer is retrofitted onto this 100,000 lb/hr steam boiler to heat 50 percent of the make-up water from 55°F to 200°F and flue gases are cooled to 100°F. At these conditions, 12.75 MMBtu/hr of total energy is available in the exhaust, of which 7.55 MMBtu/hr will be recovered to heat make-up water in the condensing economizer. More energy could be recovered if additional heat sinks are available. Given 8,000 hours per year of boiler operation, and a fuel cost of $8.00/MMBtu, the annual energy recovered is valued at:
Annual Savings= 7.55 MMBtu/hr x 8,000 hr/yr x $8.00/MMBtu / 0.83 = $582,170
EXAMPLES
District Heating SystemA boiler plant that provides up to 500,000 lb/hr of steam for a district heating system installed a direct contact condensing economizer. This economizer saves up to 20 MMBtu/hr, depending on the boiler load. Since condensate is not returned from the district heating system, the recovered energy is used to preheat plant makeup water from 45°-60°F up to 132°F, resulting in a steam system energy efficiency improvement of 6.3 percent.
Food Processing Plant
A food processing plant installed an indirect contact condensing economizer on a 20,000 lb/hr boiler. The condensing economizer reduced the flue gas temperature from 300°F to 120°F, while capturing 2 MMBtu/hr of sensible and latent heat. Energy recovered by the condensing economizer heated make-up water, reducing deaerator steam requirements from 5,000 lb/hr to 1,500 lb/hr.
Suggested Actions
• Determine your boiler capacity, average steam production, combustion efficiency, stack gas temperature, annual hours of operation, and annual fuel consumption.• Identify in-plant uses for heated water, such as boiler make-up water heating, preheating, domestic hot water, or process water heating requirements.
• Determine the thermal requirements that can be met through installation of a condensing economizer. Determine annual fuel energy and cost savings.
• Determine the cost-effectiveness of a condensing economizer. Ensure that system changes are evaluated and modifications are included in the design (e.g., mist eliminator, additional water treatment, heat exchangers). Simple paybacks for condensing economizer projects are often less than two years.
Resources
U.S. Department of Energy- DOE’s software, the Steam System Assessment Tool and Steam System Scoping Tool, can help you evaluate and identify steam system improvements. In addition, refer toImproving Steam System Performance: A Sourcebook for Industryfor more information on steam system efficiency opportunities.Visit the BestPractices Website at www.eere.energy.gov/industry/bestpractices to access these and other efficiency resources.
Reprinted from Steam Tip Sheet #26A, “Consider Installing a Condensing Economizer,” from the U.S. Department of Energy’s Office of Energy Efficiency and Renewable Energy. For more information, visit www.eere.energy.gov.
Publication date:12/03/2007