In this article, we continue the discussion of CO safety and cover several additional issues not mentioned in Part I. This will include certain types of installation problems and operational defects that develop after the system has been put into service.
INSTALL SPILL SWITCHES
I think it is important to note that there are induced draft appliances, currently installed, that continue to operate with the air switch pulled in, even though the appliance is not venting properly.Much of this is field- and installation-related, but we discussed in Part I of this article just because an appliance does not include a safety switch that will shut down equipment in the event of CO spillage, doesn’t mean it isn’t needed. We should install them, when necessary, to protect our customers and our companies.
Of course, if everyone knew what situations required such action, I probably wouldn’t have to write this article. As mentioned in Part I, rust, corrosion, and white powder on the vent or equipment is a sign of improper venting and needs correcting; the addition of safeties will not prevent all CO leak problems, however.
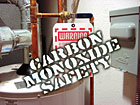
INDUCED AND NATURAL DRAFT VENTING
There is one particular installation scenario where flue gas spillage occurs almost every cycle with an induced draft appliance. This happens when the induced draft appliance is common vented with a natural-draft appliance.Most induced draft appliances have a pre-purge cycle that tends to pressurize the flue until after the burners come on. In most cases during pre-purge, a downdraft is created on the common-vented, natural draft appliance and spillage occurs out of its drafthood. Even after the burner fires, there is still some spillage of flue gases out of the drafthood appliance. How long depends on the mechanical room pressure or the vent configuration.
In addition to this, if the burner on the natural-draft appliance happens to be operating during the pre-purge of the induced draft appliance, the natural-draft appliance flue gases will also spill into the space and combustion gases can back up in the burner. Combustion gases not removed from the burner block combustion air from getting to the flame, and higher levels of CO are produced.
Under certain conditions spillage has been verified to last for several minutes, raising the CO levels in the building significantly. Field testing, or should I say real-field conditions, have shown that the entire flue can get plugged above both appliances, and both will continue to vent through the drafthood appliance. This installation really needs more than just a couple of additional safeties.
FVIR WATER HEATERS
FVIR water heaters (Flammable Vapor Ignition Resistant) have been required since July of 2003, according to requirements set by the Consumer Product Safety Commission. These water heaters are equipped with a vapor screen so consumers can store open containers of flammable materials next to them without danger of explosion.Because of the possible restriction to combustion airflow created by a dirty vapor screen, these water heaters are equipped with an overheat switch to protect the water heater.
A dirty screen causes the heater to be short on combustion air and the burner then begins to produce excess CO. Without proper air flowing into the burner, the burner will also get much hotter.
When this occurs, the overheat switch at the burner will safely shut the burner off. Although the screen is a great idea to prevent flammable gases from combusting, the safety switch is exposing the problem just mentioned.
It is common in the field to vent the FVIR water heater in the same flue with an induced-draft appliance, even though some FVIR water heater installation instructions prohibit this type of installation. The problem in the field is that the pre-purge of the induced appliance is blowing back down these new water heaters and tripping their plugged screen overheat switch if the water heater is running at the time.
Installers and technicians should be aware of the additional intermittent nuisances and possible hazards that may be created when FVIR water heaters are vented with induced draft appliances. A key word here is “intermittent” which means it may be hard to detect. Proper combustion and draft testing protocols need to be applied to demonstrate what we can’t always see or expect. At least in this case, we have a safety switch that is doing its job and that is great. But now can we keep this to a minimum?
Whenever possible, FVIR water heaters should not be vented with an induced draft appliance. There may be some new venting devices on the market soon that will address this exact type of problem.
HIGH FLUE TEMPERATURES
FVIR water heaters may also be creating an additional safety issue of concern. Field testing has indicated that the gross flue temperature exiting these water heaters is almost 100°F hotter than the conventional water heaters they replaced. This means that the actual measured gross flue temperatures of a new water heater starts at 480° to 580° right out of the box. As these water heaters develop scale buildup over time, the flue temperatures will certainly climb.Existing water heaters easily reached temperatures of 500° to 600° with minimal scale build up. These new water heaters will most likely see temperatures of 600° to 700°. The concern here is no longer CO poisoning but rather fire hazard. Most B-vent is rated for a maximum flue gas temperature of 550° to maintain a 1-inch clearance from combustibles.
Although drafthoods allow dilution air to mix with the flue gases and lower their temperature, on hot summer days or low-draft days, dilution air will be minimal and the temperature above the drafthood can be very close to the temperature coming out of the water heater, and eventually exceed 550°.
I believe it is important to start measuring these temperatures as often as possible now, just to be sure. It has been mentioned to one manufacturer of venting products to offer a high-temperature limit for B-vent flues in the future.
This is one of two possible high temperature issues on newer water heater vents. What about water heaters that use a built-on power vent on top and vent through plastic pipe?
They are designed to bring in dilution air through some type of drafthood to lower the flue temperature so it can be vented into Schedule 40 PVC pipe. Schedule 40 PVC pipe has a recommended operating temperature of 140°. Above that temperature, the strength of the pipe weakens.
This is no problem when the water heater is scale-free and operating with temperatures between 400° to 500°. However, a recent field test indicated that because of scale buildup the actual discharge flue temperature of one of these water heaters was in excess of 700°. The temperature going into the plastic pipe was well over 140° and the plastic flue pipe was noticeably discolored and starting to sag.
When the pipe eventually cracks or breaks loose, all the flue gases will vent into the building. Initially the amount of CO would normally not be that great, but as the flue gases displace the combustion air in the room, the combustion process will go berserk and CO will increase drastically.
AIR PROVING SWITCHES
The only safety to prove these heaters are venting is the air proving switch. However, it will remain closed should the flue pipe become disconnected. Therefore, it would seem logical as a preventive measure to install a high-temperature limit in the flue so the temperature going into the plastic does not become excessive.Adding safeties doesn’t eliminate the need to make the necessary repairs. Something else was actually wrong with the installation to create the unsafe condition. Adding safeties doesn’t eliminate the need to check equipment on an annual basis.
This article is not intended to explain how to make all the corrections or repairs on each problem or how to select and install extra safeties. It is, rather, intended to make you more aware of the possibilities and encourage you to observe and test thoroughly.
These conditions, situations, possible defects, etc. or any corrections we make are not currently addressed by any codes. As contractors and technicians, we have an obligation to offer corrections and solutions to our customers. Unfortunately, the correction is best identified through our testing. Testing needs to be performed on every piece of equipment and every system one at a time. If you test, you know for sure, if you don’t, you’re only guessing.
Safety hazards will never correct themselves. Some of them may be continuous, some intermittent and other hazards are just waiting to happen. The ability to detect a potential safety issue comes with knowing conditions can or will exist and that they can change constantly with the environment.
There will always be measurable symptoms or signs that exist and will expose the problem. It should be our job to recognize and address all safety issues before there is an incident affecting the safety of our customers.
Publication date:11/12/2007