Shutting down the chiller system, which cools 10,400 gallons of honing oil used in the engine block cutting process at Ford Motor Co.’s Essex Engine Plant in Windsor, Ontario, Canada, would run up costs in service and parts, including a reduction in plant productivity.
The best-case repair scenario for the V-6 engine production plant was a projected five-day disassembly of the 24-ton chiller, with hopes that necessary replacement parts would be readily available once the leaking component was found.
The worst-case scenario was waiting one or two weeks for parts and subsequently renting mobile chillers.
Gerry Miller, the plant’s compression equipment engineer, hadn’t heard of refrigeration leak sealants prior to the incident, but he was wary of putting any foreign substance into the system. “I like only refrigerant and oil in my systems, and that’s all,” said Miller, a 28-year veteran of refrigeration service, “but I had run out of alternatives.”
Previous efforts didn’t reveal the leak’s location, but did confirm two realities:
1.The leak was most likely inside the chiller’s evaporator in an enclosed tank.
2.Repairing the leak wasn’t going to be easy.
A CONSULTATION
Ford has stringent environmental policies on refrigerant leaks. So, Miller was preparing a fast-track plan to tear apart the system until Paul Appler, director of research and development for the HVACR division of Cliplight Manufacturing Corp., Toronto, suggested using a sealant made especially for refrigeration system leaks.The relatively new chiller is a 48-ton model with two 25-hp, 24-ton semihermetic reciprocating compressors. It uses filter-driers, expansion valves, R-22, and 150-viscosity refrigerant oil. The unit supplies 55°F chilled water to a 50-ton plate heat exchanger that, in turn, cools the 100°-plus honing oil to an ambient 70°.
The chiller was operating under the following parameters:
• Discharge pressure, 195 psig
• Discharge temperature, 219.2°
• Shell temperature, 212°
• Suction pressure, 40 psig
• Suction temperature, 77°
• Superheat, 60°
With no other choice than system teardown or using a sealant, Miller invited a consultation from Appler; George Cranton, a Cliplight chemical engineer; and Dave Dunn of Thermo-Dynamics Ltd., a Windsor, Ontario contractor.
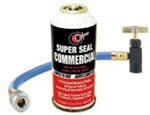
Super Seal Commercial sealant.
TRIAL USE
The sealants were still relatively new at the time. Miller said he wanted to exercise a controlled, methodical approach for their use within the plant. After making sure the system was clean, Miller gave the green light. A trial dose of 3 ounces of the industrial-strength sealant (Super Seal 3 Phase - now called Super Seal Commercial - designed for 5-ton and larger systems) was administered.Testing determined that the trial dose stopped 80 percent of the leak without any adverse effects to the refrigeration system components. Miller opted to inject an additional 3-ounce dose of the sealant. Miller said the second injection completely halted the leak, based on system operation statistics:
• Discharge pressure, 208 psig
• Discharge temperature, 103°
• Shell temperature, 162°
• Suction pressure, 68 psig
• Suction temperature, 53°
• Superheat, 13°
Miller said he waited more than one year to declare whether the sealant had completely remedied the problem. When an oil analysis and acid testing revealed a “crystal clear” oil and acid-free sample, he said, “If there’s going to be a problem, it would have surfaced by now.”
For more information, visit www.cliplight.com.
Sidebar: Tips for Applying Refrigeration System Sealant
Paul Appler, director of research and development for Cliplight Manufacturing, offered these tips for using a sealant in HVACR systems of 1.5 tons and larger.Of course, he said, the best approach is to try to find and repair a leak through conventional leak detection and repair methods. A sealant should be used only as a last resort.
Unlike automotive air conditioning systems, these sealant formulas are designed for HVAC rooftop units, refrigeration chillers, refrigeration compressor racks, and other stationary industrial systems.
Appler presented the following checklist for using an industrial refrigeration system sealant:
• The system should leak no more than 14 percent of its charge over a four-week period in order for a sealant to be used. Leaks this size and larger can typically be found by using standard electronic and dye detection methods. However, if the leak is undetectable or inaccessible, an industrial-strength sealant can be successful with leaks of this magnitude or smaller.
• Moisture, acid, and other noncondensables must be removed from the system prior to administering the sealant.
• Systems that have leaked more than 17 percent of their total charge are probably contaminated, he pointed out. Refrigerant recovery is recommended for the purpose of drying, removing light particulates, and replacing suction and liquid line driers (where required). The refrigerant can then be reintroduced into the system if deemed suitable by the technician.
• Systems under 5 tons shouldn’t exceed an application of one 3-ounce can of sealant. Systems over 5 tons can receive two cans, but the applications must be separated by a minimum 10-day period. During this intermediate time, system pressures and temperatures should be checked to evaluate the first application’s success before adding the second can.
“Sealants are engineered for leaks that go undetected because of their small size and/or intermittent nature,” said Appler. “If you can find the leak, fix it. If you can’t find it, then use a sealant.”
Publication date:05/05/2008