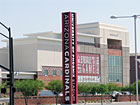
The University of Phoenix Stadium is the centerpiece of a promotion focus that includes a media center with unique cooling demands.
To help with the hype, the nearby Glendale Media Center was created with wraparound windows and outdoor rooftop platforms for backdrops of mountains, the nearby stadium, and its neighboring National Hockey League arena. There is up to 40,000 square feet of space to accommodate hordes of media types.
One challenge was to create the comfort cooling at the center in a part of the country with frequent 100°F or warmer days. Those involved in the project also had to meet key deadlines for startup, ensure reliable cooling, take advantage of the Phoenix area’s low wet bulb to reduce energy consumption, and minimize the footprint of the mechanical equipment.
“There were several design considerations that we needed to incorporate into the manufacture of the Media Center’s packaged central plant, but most important was speed - from concept to startup,” said Sam Macrane, product manager for Chil-Pak, which built what he described as a “fully integrated packaged central cooling plant” for the project.
He said the company was chosen for its ability to “bring all the variables associated with the engineering and construction of a typical central plant into a single cost- and space-efficient cabinet, where all electrical, pumps, piping, controls, chillers, and cooling tower could be integrated in a controlled ISO 9001 factory environment. This integrated package plant concept provided a complete chilled water solution at the lowest possible cost to the building owner in just a few months.”
Macrane noted that the company draws all its components from a variety of manufacturers, an approach he called “brand neutral - application specific.” In the case of the Media Center, the 440-ton packaged central plant integrated two Carrier 30HXC screw chillers, redundant Armstrong Series 4280 chilled-water (CHW) condenser water (CW) pumps, ABB ACH550 variable-frequency drives (VFDs), a Mueller Accu-Therm plate and frame heat exchanger (HX), Carrier Control Network (CCN) controls, and a demounted Evapco AT dual-cell cooling tower.
“The Carrier screws made a good choice for the chillers due to the multiple compressors and dual circuit evaporators. This feature ensured sufficient cooling capacity would be available even if a compressor went down. Additionally, the stacked barrel design reduces chiller width, which is a key packaged plant design consideration. The width of the unit is important due to over-the-road shipping constraints,” said Mark McKee of Sigler & Reeves, who provided the chillers for the packaged plant.
“A redundant pump design was essential to provide the availability desired. Should a pump go down, the standby pump automatically comes on-line. Furthermore, the redundant CW pump is used to drive the continuous economizer when the wet bulb conditions allow the HX to pre-cool the returning CHW.
“The use of outdoor temperature and humidity sensors allow the control system to calculate when the cooling tower (CT) can make water cold enough to pre-cool the returning CHW, accounting for the delta T across the HX. Pre-cooling the returning CHW effectively reduces the mechanical cooling load, reducing energy consumption and improving chiller part load performance.
“This facility has numerous ton-hours available for ‘economizing’ due to the long operating hours and low Phoenix wet bulb conditions, so the HX was sized to take about 160 tons of load,” said Chil-Pak’s chief engineer, Daniel Dominguez.
Facility personnel throughout the season observed the economizer benefit. “We love the savings from the continuous economizer,” said Mark O’Brian, maintenance supervisor for the facility.
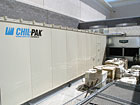
This packaged central cooling plant is described as “brand neutral-application specific.”
“The single point of contact for project coordination and factory-prepped connections saved a lot of time and made this one of the easiest plants I have ever installed.” The packaged plant is “about one-third the footprint of a comparable field-constructed plant and eliminated the owner’s expense of building a mechanical room,” Dill said.
As a rule, Macrane said the Chil-Pak Central Plant Solution™ reduces the engineering design time, reduces the cost of field labor, and simplifies project management versus field-constructed mechanical rooms. He noted that the Chil-Pak “easy button” approach might not be right for every project, which is why the company has an application support team to help engineers and owners evaluate different packaged plant design options.
The “brand neutral - application specific” concept allows a degree of product flexibility for 100- to 3,600-ton applications, he said. Component selection depends on the application, including such options as water-cooled R-134A screw, centrifugal, or Turbocor chillers, various pumping configurations, cooling tower arrangements, and HX economizing capabilities. In general Macrane said, “The market demand for packaged central plants seems to be expanding with a shrinking skilled labor force, more engineering firms without central plant design expertise, and ever tightening budget constraints.”
For more information, visit www.chil-pak.com.
Publication Date:05/12/2008