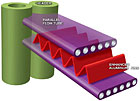
The three basic components used in the manufacture of microchannel coils are parallel flow aluminum tubes (purple in illustration above), enhanced aluminum fins (red), and header manifolds (green). These components are combined by alternating tube and fin sections - a layer of tube atop a layer of fin atop a layer of tube, etc. This combination of fins and tubes is captured at both ends by the header manifolds. (Illustration courtesy of Johnson Controls.)
Long ago, the industry determined that the combination of copper tubing and aluminum fins provided the most efficient transfer of thermal heat in condenser coils.
Manufacturers of residential units are not necessarily on that same page - or that line of thinking - today.
Most manufacturers, if not all, are revising, have revised, or continue to revise their outdoor coil construction. One of the main objectives, of course, is to increase heat transfer efficiency, as energy efficiency is high on every homeowner’s wish list.
In the end, each manufacturer believes it has engineered and/or perfected - at least up to now - the most-efficient coil design. Some, like Goodman Manufacturing, have made changes as a direct result of the efficiency offered from R-410A refrigerant.
The NEWSasked major manufacturers to discuss the residential condenser coil changes that are occurring in the marketplace. Though not all responded, those that did provided great detail as to what’s happening with the component.
MICROCHANNEL TECHNOLOGY
Ten years ago, York International engineers were very concerned with three major issues facing the industry.“The first was efficiency, whether it was a 12 SEER or 13 SEER minimum,” said Andy Armstrong, director of marketing, Johnson Controls-Unitary Products. “We were confident that condenser coils would be challenged with new efficiencies.”
The second issue to address, he explained, was size. “The industry’s answer to efficiency has always been tied to bigger heat transfer surfaces,” he said. “Both application size restrictions and raw material usage made bigger and bigger coils an untenable long-term solution.”
The last issue involved sustainability. “We needed to make products that used less materials to begin with, and then, after use were easier to recycle and reuse,” said Armstrong.
In the case of Johnson Controls and York, they turned to microchannel technology, technology that has been used in the automotive industry for some time now. According to believers in the design, heat transfer efficiency and improvement in reliability are achieved through a higher level of corrosion resistance. (Johnson Controls uses the name MicroChannel.)
“Today, Johnson Controls believes that MicroChannel technology is the solution to all three challenges,” said Armstrong.
“With better heat transfer efficiency, MicroChannel allows us to economically reach the efficiency levels demanded by our customers. Not only do we reach higher efficiency levels, we reach them in a much smaller footprint. And from a sustainability standpoint, MicroChannel allows us to use far fewer raw materials.”
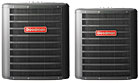
Goodman said its unit with SmartCoil™ and R-410A refrigerant (at right) use 25 percent less refrigerant and the overall unit requires 15 percent less volume. (Photo courtesy of Goodman.)
STATING ITS CASE
Johnson Controls is so convinced it has the answer, a year ago it produced a white paper on the subject, titled “Microchannel Technology: Benefits of Microchannel Technology in HVAC Applications.” (For the full report, go to www.us-ac.com.)In the white paper, it states three basic components are used in the manufacture of microchannel coils: parallel-flow aluminum tubes, enhanced aluminum fins, and header manifolds.
According to the Johnson Controls’ report, these components are combined by alternating tube and fin sections - a layer of tube atop a layer of fin atop a layer of tube, and so forth. It said this combination of fins and tubes is captured at both ends by the header manifolds.
“Separator plates are located within the header manifolds to segment the coil assembly into two distinct sections: a desuperheating section, where the refrigerant gas transitions from gas to liquid, and a subcooling section, where the liquid refrigerant is further cooled below its saturated temperature,” it states in the report.
The manufacturer’s report also points out several advantages of microchannel technology when compared to traditional copper tube and aluminum fin designs. Per Johnson Controls, that list includes improved heat transfer properties, smaller size and weight, improved durability and serviceability, improved corrosion protection, and reduced refrigerant charge up to 50 percent. The report goes on to state its case and proof for each advantage it listed.
“Looking towards the future, January 2010, one of the current refrigerant options, R-22, can no longer be used in the manufacture of HVAC equipment and will be entirely replaced with R-410A, a more environmentally friendly refrigerant,” it states in the white paper. “Microchannel addresses all of the current and foreseeable future challenges in the HVAC industry.”
Armstrong was just as definitive. “Although R-410A refrigerant is better for the environment than R-22, no one would argue that the less we use any greenhouse gas, the better,” he said.
“With our current MicroChannel 5-ton 13 SEER product, we use one-half as much refrigerant as our closest competitor and one-third as much as another. When considering energy and time used in recovery, this statistic alone has dramatic effects for this industry and our environment.”
He added, “When the Johnson Controls-built unit has completed its useful life, an all-aluminum coil is far easier to recycle than its tube-and-fin counterparts. With an eye on the future, Johnson Controls engineers have taken a smaller box to a higher level.”
VARIATIONS THEREOF
Nordyne said microchannel technology is quite new for its current products in the field. It stated that microchannel is currently only available for its R-22 air conditioning products, though many of its split-system and packaged products have converted to R-410A.“We are continuously evaluating new technologies to make sure that we are providing the most cost-effective solutions to our customers while optimizing performance and reliability,” said Dan Arnold, senior director of engineering, cooling systems, Nordyne. “We were early adopters of microchannel and have been very pleased with its performance advantages. It’s a robust technology.”
Arnold added that the company is planning to expand the microchannel technology into other products.
“Our customers like that microchannel allows the footprint to be smaller and that the units weigh less - making installation and handling easier and lowering freight costs,” he said.
Carrier and Bryant, on the other hand, employ Microtube technology in their residential condensing units, which the manufacturer said utilizes smaller copper tubing, which, in turn, uses less refrigerant in the system. According to Jeff Warther, senior product manager at Bryant, Bryant uses two internal enhancements to the outdoor unit, one optimized for air conditioners and one optimized for heat pumps.
“Hatching of the inside of the copper tubes optimizes the heat transfer across the coil, hereby making the coil more efficient,” he explained. “For indoor coils, we manufacture a tin-plated coil. This tin-plated coil resists corrosion better than standard copper coils, and they come with a 10-year limited warranty.”
Bryant said its Microtube Technology™ is one of the smallest copper tube-aluminum fin technologies in residential applications. It said the technology has allowed the manufacturer to reduce the amount of refrigerant and the size of the units from previous models. Warther noted that its newest line of air conditioner and heat pump condensers, introduced in January 2006, are 20 percent smaller than previous 13 SEER products, 30 percent lighter than previous 13 SEER products, and use 40 percent less refrigerant than previous 13 SEER products, all compared to its 2005 38 ETG model.

Smaller tubing in an outdoor coil is designed to generate greater performance, according to Goodman. As pointed out in this illustration, the refrigerant molecules swirl inside the grooved copper tubing, increasing the time the refrigerant molecules come into contact with the inside of the tubing. “Slots” are designed to increase the amount of space available for the refrigerant molecules to touch the inside of the tubing, optimizing heat transfer, it said. Maximum heat transfer between the refrigerant molecules occurs highest at the outside edge of the tubing, it added. (Illustration courtesy of Goodman.)
ANOTHER SLANT WITH R-410A
Goodman Manufacturing is also making changes to its condenser coils, due mainly to the upcoming introduction of R-410A. In the months to come, R-410A will become the primary refrigerant used by the industry in the manufacture of new air conditioning equipment. It said it is ready with its new SmartCoil™, which is comprised of aluminum fins and 5-mm copper tubing. The combination makes the coil smaller and smarter, it said, noting that several patent applications are pending on this coil as a result of the technology required to engineer and manufacture it.“Regardless of SEER numbers, our goal is to manufacture a complete line of residential and light commercial products that maximize energy savings for homeowners,” said Gary Clark, senior vice president, Goodman Manufacturing. “This is just one aspect of our overall green initiatives which are focused on providing the best value and best performance for both HVAC dealers and homeowners.”
Because the majority of thermal transfer occurs in the condenser and evaporator coils, the manufacturer said its engineers accepted the challenge of optimizing thermal transfer in the condenser coils for products that use R-410A. It found out that R-410A refrigerant “works very well with 5-mm-diameter copper tubing.”
In a company brochure, it noted that the tubing’s wall strength is “as strong as the old 3/8-inch tubing.” Regarding the grooved copper tubing, Goodman pointed out that grooves increase the total surface area of the tubing, thus increasing heat transfer.
According to Clark, manufacturers of R-410A refrigerant contend that smaller coils assist the heat transfer properties of the condenser coil.
“From my perspective, you have the HVAC manufacturers and the chemical companies making rather broad changes to their product line as a direct result of the R-410A refrigerant introduction,” he said.

Sidebar: Another Approach - All Aluminum
Trane and American Standard have a different approach to outdoor coil construction. Both believe in aluminum. Last year Trane introduced an era of all-aluminum matched systems. Building on its patented all-aluminum Spine Fin™ condenser coils on outdoor units, Trane added its AlumaTuff™ coil (pictured right, courtesy of Trane), which has aluminum tubes, tube sheets, and plate fins.The manufacturer said all-aluminum coils prevent formicary corrosion, rusty tube sheets, and helps avoid pinhole leaks. “Being corrosion- and rust-resistant, all-aluminum coils deliver on the promise of high efficiency over time, while assuring exceptional reliability,” said Randy Scott, Trane vice president, product systems management.
Trane backs the AlumaTuff coil with a 10-year limited warranty.
American Standard went the same route with its all-aluminum DuraCoil™ evaporator coil to create all-aluminum matched systems, too. It said DuraCoil still uses copper-to-copper refrigerant line connections so that standard installation procedures can be followed. It said it has the same performance ratings and casing dimensions of the copper coils they replace. The new coil is also available for different cabinet widths.
“American Standard dealers appreciate how innovations such as all-aluminum matched systems provide a unique selling advantage that competitors can’t match,” said Jamie Byrne, American Standard vice president of sales.
Publication date:09/08/2008