OVERVIEW
For fleet managers, nothing is more important than keeping vehicles running and productive. Maintaining vehicles, including repair, upkeep, and downtime, has a huge impact on a fleet’s bottom line. A proactive, preventive maintenance program helps fleet managers keep vehicle repair costs to a minimum.Unfortunately, many fleets simply take a reactive approach to vehicle maintenance. In a widely distributed fleet, that could mean costly repairs, not to mention vehicle downtime. Fleet managers need to be able to monitor and collect data on the “health” of their vehicles to fix problems early and reduce costs.
REDUCING VEHICLE MAINTENANCE COSTS
Scheduled MaintenanceRegularly scheduled maintenance is the most effective way to minimize vehicle downtime. Even simple maintenance like regular oil changes can help reduce engine wear and make the vehicle run cooler and last longer, according to AAA. Setting preventive maintenance schedules requires knowing the type of vehicle, its usage (mileage, hours, operating environment), original equipment manufacturer (OEM) warranty, recall status, and regulatory requirements. In addition, it is beneficial to know the types of diagnostic problems that typically occur with different vehicle types.
Vehicle Performance
Information on individual vehicle performance on the road is vital to reduce maintenance costs. For example, when trucks are traveling in high heat and steep grades, monitoring the temperature of the engine, the air intake temperature, and oil pressure can help fleet managers gauge engine performance. Having access to statistics on vehicle diagnostics over time is also important to determine if a vehicle is performing optimally.
Fuel Economy
Vehicles operate more efficiently when they are well maintained. Therefore, improving vehicle performance through preventive maintenance can improve fuel economy. Monitoring unauthorized vehicle use, excessive speeding, mpg, and idling can also greatly reduce fuel usage. Repairing a vehicle that needs a tuneup can improve its gas mileage by an average of 4 percent, according to the U.S. Department of Energy. Furthermore, fixing a serious maintenance problem, such as a faulty oxygen sensor, can improve your mileage by as much as 40 percent.
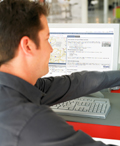
Wireless fleet management provides near real-time information on virtually every aspect of vehicle operations via the Internet. (Photo courtesy of Networkfleet.)
MONITORING ENGINE PERFORMANCE WITH A WIRELESS FLEET MANAGEMENT SYSTEM
Imagine receiving instant notification by e-mail when a vehicle has a transmission malfunction or engine problem so it can be repaired quickly. Combine that with the ability to track the exact location and speed of each of vehicle 24/7 from anywhere in the world. That is the power of a wireless fleet management system.Wireless fleet management gives fleet managers the power to access near real-time productivity and efficiency information on virtually every aspect of their fleet operations via the Internet. The system’s in-vehicle device collects and wirelessly transmits data directly from the engine computer and from a global positioning system (GPS). Fleet managers can view online 24/7, specific vehicle data such as current location, fuel consumption, mileage, speed, and idle-time. Emissions can also be monitored wirelessly, eliminating the need to bring vehicles to a smog check facility (California only).
At the same time, a system with remote diagnostic capability can notify fleet managers via e-mail when an exception occurs within the fleet, such as when a vehicle has exceeded a speed threshold or the check engine light is illuminated. By identifying issues early, fleet managers can proactively fix vehicle problems before they escalate into larger issues. This keeps vehicles running and in production.
HOW WIRELESS VEHICLE MANAGEMENT STREAMLINES FLEET MAINTENANCE
I. Lowering Vehicle DowntimeA. Unauthorized or Unnecessary Driving Wear and Tear Costs
According toConsumer Reports, wear and tear often accounts for nearly $0.25 per mile. Any unauthorized or unnecessary vehicle use can contribute to vehicle wear and tear. Fleet managers can use wireless fleet management to verify daily route and stop locations. By analyzing driving patterns and optimizing routes, the system can help reduce unnecessary vehicle use.
B. Diagnostic Trouble Code Alerts
Typically, managers wait days or even weeks for drivers to report that a vehicle’s check engine light is on. A wireless fleet management system can automatically notify fleet managers by e-mail immediately and report a diagnostic trouble code (DTC). The Networkfleet system, for example, provides the precise DTC and a description identifying the specific nature of the problem. This allows technicians to begin their analysis immediately instead of spending time trying to determine what is wrong.
Fleet managers with relatively new vehicles can minimize repair expenses by taking advantage of vehicle warranties.
Networkfleet has collected DTCs from thousands of vehicles in fleets across the United States. Analyzing aggregate data shows that 47 percent of diagnostic trouble codes for light/medium duty (OBD-II) vehicles were related to emissions issues and 24 percent were related to fuel consumption issues.
Top Individual Diagnostic Trouble Codes Collected:
1.Light Vehicle DTC (P0300) is related to cylinder misfires. Misfires can be indicative of poor maintenance or of a faulty or worn ignition system.
2.Light Vehicle DTC (P0171) indicates that the air to fuel mixture is suboptimal. This could be indicative of a faulty O2 sensor or a faulty/worn fuel pump.
3.Light Vehicle DTC (P0420) indicates that there may be a problem with the vehicle catalyst and it should probably be replaced.
C. Scheduled Maintenance Alerts
A wireless fleet management system can provide daily odometer updates and notify users by e-mail when vehicles have reached predetermined maintenance intervals. Fleet managers can establish custom maintenance alert schedules and receive e-mails when vehicles are due for maintenance based on mileage or other criteria. These schedules enable timely regular maintenance and repairs that extend vehicle life and increase vehicle resale value.
D. Idle-time Data
Excessive vehicle idling leads to increased fuel expenses and engine wear. On heavy-duty vehicles, 0.82 gallons of gas are consumed for every hour of idle-time, according to the U.S. Environmental Protection Agency. Fleet managers utilizing wireless fleet management can monitor idle-time by vehicle to determine which vehicles exceed a certain idle threshold such as 15 percent. Fleet managers can also run a report to compare idle-time as well as fuel consumed between similarly operated vehicles.
E. Remote Smog Check
With wireless fleet management, vehicle emissions are continually monitored through the wireless network. Networkfleet notes that it has a contract with the state of California to allow fleet customers to enroll in a free, remote smog check service. There is no need to have vehicles physically inspected as long as they are running cleanly.
If a vehicle goes out of emissions compliance, the fleet manager receives an e-mail and has 45 days to fix the problem. Fleets using this feature are exempt from having to get smog checks or pay smog certifications. This eliminates fees and reduces the time the vehicle is off the road.
II. Improve Maintenance Accuracy
A. Automatic Odometer Readings
For a distributed fleet, accurate odometer readings are usually a manual, error-prone process when mileage is collected at the fuel pump. Wireless fleet management automates this process by calculating mileage using data from the vehicle’s engine computer. This eliminates the necessity to physically audit vehicle odometer information, which can be time- and labor-intensive.
Access to accurate mileage information is essential to a good preventive maintenance program.
B. Automatic Recall Notices
Recalls can cause vehicle downtime and maintenance problems. If a vehicle manufacturer is found by the National Highway and Traffic Safety Administration (NHTSA) to be responsible for a serious defect, an auto recall is issued. An auto recall requires the manufacturer to send an official notice to owners of the vehicles found to be defective. More often than not, only a portion of the production run of a certain make, model, and year vehicle is affected by an auto recall. Fourteen percent of all vehicles on the road have been recalled at least once to correct either a safety defect or noncompliance with a particular safety standard, according to an article inThe Detroit News.
Online recall notices from a wireless fleet management system give fleets important safety information much faster than postal mail notices from the manufacturer. This allows fleets to make repairs immediately, increase safety, and beat the rush at their service provider.
C. Maintenance History Online
Wireless fleet management can help fleets receive a higher resale value for their vehicles by providing a complete online service history, eliminating the need to maintain paper records. In addition, service records can be quickly and easily entered online through the system’s Website.
MINI CASE STUDY - ROTO-ROOTER
Hoffman Southwest, the largest Roto-Rooter franchisee in the country, selected the Networkfleet system to provide both GPS location and diagnostic information for its fleet of 400 field technicians. The company increased its annual profits by more than $200,000 by being able to make more service calls and reduce overtime costs.Using Networkfleet, Hoffman was able to improve its fleet vehicle maintenance and purchasing by analyzing the frequency of diagnostic trouble codes on various makes/models. Networkfleet instantly alerts Hoffman fleet managers if there is a diagnostic problem with a vehicle. This allows Hoffman to proactively address problem vehicles.
Prior to implementing Networkfleet, the company experienced high repair bills associated with blown engines and other vehicle problems where earlier recognition and maintenance of the vehicle could have reduced or even eliminated the resulting repair cost. During the first eight months of using the system, more than 30 percent of vehicles had diagnostic trouble code alerts. Hoffman now tracks this trouble code data, which allows them to proactively repair vehicles and helps them make better decisions on future vehicle purchases.
Reprinted and adapted with permission from the Networkfleet white paper “Optimizing Fleet Maintenance With Wireless Vehicle Management.” For more information about optimizing fleet maintenance, visit www.networkfleet.com or call 866-227-7323.
Publication date:03/09/2009