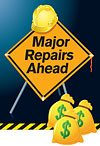
“Deferred maintenance” is a terrible misnomer for what really happens when maintenance doesn’t get performed for a long time. Another name for it is “catastrophic failure.” According to participants in a recentNEWSonline survey, results of putting off maintenance too long can range from simple component failures to major pieces of equipment dying much too soon to the failure of the entire physical plant - and the inconveniences and embarrassments that go along with it.
The worst case of deferred maintenance Wayne Turchetta ever saw involved pneumatic controls. There was water in the air lines “because no one checked on the air compressor or air dryer in the basement,” said the vice president of HMC Service, so it was “out of sight, out of mind. It failed.”
Service manager Scott Davis has seen his fair share of deferred maintenance problems for customers ranging from homeowners to health care facilities. These have included “burned compressors, house burned down, exploded fans, etc.”
The most extreme case of deferred maintenance reported in the survey came from Bob Lake, president of EMCOR Service/Mesa Energy: “A complete central plant went down at a hospital,” he wrote. “It was a complete disaster for them. We got a temporary chiller in there ASAP, but they really paid the price both to the community and to us (the contractor).”
With so much at stake, why do these customers choose to put off maintenance?
WHY THEY DON'T DO IT
Why do some facility owners decide not to get regular system maintenance? “Idiots,” snarled one survey respondent, a sentiment that many probably would like to echo if they dared. Yet, we have no problem saying it to our in-laws when one of them decides to never check the oil in their car, and the thing breaks down. There is very little sympathy for stupidity, or a lack of common knowledge.The person making the maintenance decision is typically the owner, facility manager, director of engineering, or controller.
Another probable “why” was offered by Davis, who explained, “It cuts into their [the owner’s] profit bonus.” But so do catastrophic failures, right?
An anonymous survey respondent chalked the reluctance up to “on-staff maintenance workers who cannot perform repairs.” Another said it was because “they passed the energy costs on to tenants.”
“Saving dollars is the only reason,” said EMCOR’s Lake. “The company is strapped for cash and this is one of the first places to cut.” It seems obvious to outsiders that this is shortsighted, cutting-off-your-nose- to-spite-your-face economy, especially when the results can be like those described previously - and a lot more costly than performing maintenance would have been.

Icing up is just one of the pitfalls of not performing regular maintenance. It can lead to much more severe problems and failures.
WHY DO IT?
There are many reasons to perform regular maintenance, and they don’t require a large stretch of the imagination. The main reasons are to “minimize downtime, minor repairs vs. major replacements, loss of productivity, and extend life of equipment,” said HMC’s Turchetta.The benefits to the contractor include “steady work in slow seasons,” with “less overall maintenance costs” to the customer, said Davis. Refrigeration contractor Dean Slowik, of Slowik Refrigeration, Benton Harbor, Mich., pointed out that for those customers who allow him to maintain their equipment, compressors could last a very, very long time.
One respondent hinted at the appropriateness of having an outside contractor do the work, rather than in-house staff. “If we perform it, it is scheduled and completed,” said Pattie Krippendorf, account sales representative for Mechanical Inc. “If they self-perform it, it may or may not get done.”
“Generally, the in-house techs are not qualified,” said Jaimi Lomas, general manager of A.O. Reed & Co. “Going with a qualified vendor will add to the life span of the equipment and save energy.”
“To the customer, units run more efficiently if they are well maintained,” said Karen DeSousa, operations manager, Advance Air & Heat Co. Inc. “We are also able to catch many repair issues during maintenance that would otherwise have resulted in a service call, downtime, or unit damage. Our company benefits by putting techs to work during slow times,” she added, “and by having predictable (usually upfront) revenue.”
The benefits of HVAC maintenance are huge, said Thom Brazel, GM West Coast operations for Hill York. “HVAC maintenance is absolutely critical. I have seen $100,000-plus units fail 10 years before their life expectancy due to lack of maintenance. I have seen million-dollar claims in high-priced residential condos due to lack of maintenance - flooding, mold, IAQ, etc. Need I say more?”
Lake pointed out benefits such as “lower repair costs along with an extended life of the equipment. It will also run more efficiently, thus saving energy costs.”

Maintenance through monitoring could be the motto for ASHRAE’s rededicated headquarters. System parameters are monitored so that maintenance is performed at the ideal time.
EDUCATING OWNERS
If justifying the need for maintenance is a matter of money - and it is - then what do contractors need in order to help make their case?“It takes a lot to convince the owners,” said Davis. “They think changing filters is enough. Usually it takes a major failure to convince them.” That type of education could be called the school of hard knocks.
The goal, said Krippendorf, is to create “an informed customer. If they are not informed, you have to educate them.”
“Most know they need it,” said Lomas. “Typically we are selling against a competitor. We usually have to convince a client when the equipment is new that the warranty does not cover preventive maintenance.”
“Data on savings in reduced service calls and energy savings data for well-maintained vs. unmaintained units would be helpful,” said DeSousa.
“Maintenance is a key part of the efficiency of any equipment,” said Jeff Phillabaum of Hill York. “This is another verification of when equipment goes beyond performance parameters; this verifies that a clean filter affects performance. It’s the same thing on a pump or a cooling tower.
“Maintenance is a huge part, and I think owners are becoming more aware of this,” he said. “Efficiency is directly correlated to maintenance. We want to be part of the maintenance solution. It really ties us with the owner. It has a lot to do with an ongoing maintenance business. There’s pull-through business, too.”
Keith Kramp of Double K Enterprises, St. Joseph, Mich., agreed, but added that to really build the importance of maintenance with the owner, the contractor needs to communicate thoroughly about what he did to the system, and what his actions may have prevented. “You can’t just send the bill.”
According Janice Peterson, P.E., LEED-AP, formerly a mechanical engineer and now with the Northwest Energy Efficiency Alliance, Portland, Ore., “There is a widespread recognition of potential benefits [of maintenance]. It is pretty widely accepted that building O&M improvements are going to be the next big area of building improvements. Building owners still need information on these very real benefits.”
According to Peterson, owners can expect to save 10-15 percent in energy efficiency with improvements in building maintenance - information that contractors should be ready to communicate to decision-makers. There also are benefits of increasing comfort and tenant satisfaction.

Refrigeration contractor Dean Slowik, of Slowik Refrigeration, Benton Harbor, Mich., said that when customers let him maintain their equipment regularly, compressors tend to last a very long time.
MEASURE IT
“There is a need for better metrics at both the management and building operator level,” she said. “There is a need to distill the information down, and get better usable, actionable information into the hands of building operators.” In other words, measure the results and communicate them as needed.New ways are emerging to help contractors justify the cost of maintenance, through both extended equipment life spans and reduced energy costs. John Conover IV, president of Trane’s Commercial Business in the Americas, pointed out that maintenance is being looked to for efficiency, not just dependability. This is a major effect of the increased interest in sustainability. He also said it will tie into systems that provide self-diagnostics and continuous commissioning, which will communicate when certain system parameters “go out of whack.”
In fact, this is how the renovated headquarters building of the American Society of Heating, Refrigerating, and Air-Conditioning Engineers (ASHRAE) will keep track of its maintenance needs - maintenance through monitoring, not based on somewhat arbitrary schedules. For instance, constant monitoring of system pressure drop will point out exactly when filters need to be changed.
Conover added that monitoring systems for operating data, and comparing it to utility costs, can provide important information.
“Convince owners to do energy studies,” he said. “Onstar, for instance, sends a monthly e-mail on how the car is doing,” he pointed out. “That’s where we’re going.”
William Harrison, ASHRAE’s 2008-09 president, asked members to focus on the operation and maintenance of high-performance buildings. “The unfortunate truth is that many buildings with great designs fade from green to grey when building operators don’t understand how to realize the full potential of the energy-conserving systems they manage,” he said. “A study by the Energy Systems Lab at Texas A&M University indicated that energy use in buildings could be reduced by 10-40 percent by improving operational strategies in buildings.
“Achieving sustainability ... means that we must deliver our message to building owners,” he said. “Owners must be educated so that they can evaluate building decisions based on life-cycle costing. Investors know how to evaluate the cost of the floor plate lost to a larger equipment room. Our job is to show them how to evaluate the cost of not having accessible equipment with efficient duct transitions.”
High-performance buildings require specialized maintenance, he continued. “The operating cost for HVAC systems is made up of several components. Energy cost is a large component. Repair and replacement costs can be large. Maintenance cost is significant and is different from others in one critical characteristic: It can be deferred. Unfortunately, when maintenance is deferred, all of the other costs increase.”
The society’s Technical Resource Group (TRG) 7, Tools for Sustainable Building Operations, Maintenance and Cost Analysis, was formed to produce publications and programs to advance its efforts to communicate with investors and owners. Contractors are encouraged to attend the TRG’s meeting at the ASHRAE Winter Meeting in Chicago.
For more information, visit www.ashrae.org.
Sidebar: Maintenance Resources
There are a few resources already available that can help contractors show building owners the benefits of improving their operations and maintenance:www.betterbricks.com
http://cbs.lbl.gov
www.energystar.gov
Publication date:12/15/2008