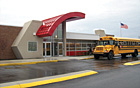
In 2006 the Moon Area School District (15 miles northwest of Pittsburgh) completely renovated the 38-year-old McCormick Elementary School. The HVAC system had to be installed in three months before the school reopened. There was no room for ductwork. Heat recovery, energy savings and exact temperature zoning controls were high priorities.
In 2006, the Moon Area School District (MASD) completely renovated McCormick Elementary School, which is located 15 miles northwest of Pittsburgh. Despite completion of major construction, Alan Criswell, MASD supervisor of buildings and grounds, had an extremely tight schedule for the HVAC system installation. It was May 2007, and he needed to have the equipment in place and operating for the August school opening.
Can you air condition a school and turn it around in one summer? With ductless systems it was possible.
With school projects, timing can be critical. “It takes a while to sow the seeds” for new work, said David Heckler, vice president of Comfort Supply Inc. (CSI), Pittsburgh. “Some stuff goes quickly, but other stuff takes a while, getting the budget approved and getting the money. We’re accustomed to working like that. We know that stuff takes a long time to come around.
“We’re a niche wholesaler,” he added; “we primarily sell equipment, not sheet metal, screws, and commodities. We deal with mechanical contractors. We know that we can call on engineers, architects, and design professionals.” Replying on its professional resources, the company provides design-assistance to contractors. “We help guys lay jobs out. We certainly do have a lot of people on staff with a lot of technical ability who will assist. We’ve been big ductless guys for a long time (since the early 1980s).”
On this particular job, CSI worked with R&B Mechanical Inc., Pittsburgh. According to project manager Tom Recker (the R of R&B), the McCormick project had a very tight window - “tighter than usual for a school,” he said. “US Airways had owned the building and it sat idle for a year or two. The school district brought it back because their population grew.”
YOU NEVER KNOW WHAT YOU CAN DO
Having a fast-track job like this one “kind of opens your eyes,” said Recker. “‘Wow, we can get a lot done.’ We worked with the engineer,” Dan Kendra of Tower Engineering, Pittsburgh.“He did a great job. They visited the site almost weekly, so we were able to work out problems on the site instead of using RFIs (Requests for Information). Dan made himself very accessible. He was aware of what it would take to get it done.”
Most of the contractor’s coordination was with the electrical trades, Recker said. “They did a nice job also.”
R&B superintendent John Hazel also “did a phenomenal job,” Recker said. Working hand-in-hand with Kendra, “he actually found different routing that allowed for shorter piping runs, using less refrigerant and resulting in a better system. That was great because material costs have gone through the roof.”
The existing building did not have a/c and did have an antiquated hot water system. “Some of that hot water piping remained and we tied into some existing lines, ran new lines at the same time,” said Recker.
The project’s start time was May 1. It’s required end time was Aug. 30.

Mitsubishi Electric’s ceiling-recessed cassette indoor unit was installed in the library at McCormick Elementary School, Moon Area School District, Pittsburgh.
THE EQUIPMENT
Meeting that timetable required equipment that was available on very short notice and could be installed quickly. There was no room for ductwork. Heat recovery, energy savings, and temperature zoning controls were high priorities.The hot water heating system would not come online until late November, so the HVAC system had to include a generous heat pump capacity to keep the building warm until the hot water boilers were operational. “The heating system is a hybrid, a heat pump-A/C-glycol water system,” said Recker. Its unique design, Kendra’s, lets the heat pumps take over on certain days, Recker explained. A set temperature of 45°F brings on the heating system.
CSI had the ductless equipment in stock (City Multi® R2-Series Variable Refrigerant Flow Zoning (VRFZ) systems from Mitsubishi Electric HVAC, Advanced Products Division). An easier installation, combined with Kendra’s onsite design assistance, helped cut the labor time in half. The 69-ton system was up and running in time for the school year.
Lossnay® energy recovery ventilators were used in conjunction with the ductless systems to meet the need for improved IAQ, heat recovery, efficiency, and ventilation. The City Multi Controls Network (CMCN) allows Criswell to control all temperature zones locally or remotely. A split-ductless system also was employed to provide cooling for a large computer lab.
SPECIAL NEEDS
“Over the past 12 months, the systems have performed outstandingly,” Criswell said. “I have had no complaints from teachers, which is a tremendous plus. I would highly recommend this system to anyone. The performance has exceeded my expectations.”But the performance of the system goes beyond comfort and efficiency. “At McCormick there is one child with MS,” said Recker. This disease affects the insulation of the central nervous system, and similar to the performance of frayed electrical wiring, heat can affect symptoms. “Cooling is very important.”
There is a lot to learn from a job like this. “You can take something away from that, yes you can,” said Recker. “Every building is unique,” but understanding how various elements worked together adds to a contractor’s knowledge base - not just of the systems, but of the people and companies they work with.
For more information, visit www.comfortsupplypgh.com, www.mehvac.com, and www.randbmechanical.com.
Sidebar: Living Lab
PITTSBURGH - Comfort Supply, Inc. (CSI) opened its Variable Refrigerant Flow (VRF) Living Lab in 2008. With more than 80 architects, engineers, mechanical contractors, and developers from western Pennsylvania in attendance, CSI showcased its new lab, which features Mitsubishi Electric HVAC Advanced Products Division’s City Multi Variable Refrigerant Flow Zoning (VRFZ) systems.“The lab is a state-of-the-art office and training facility that allows us to study and promote VRF technology in a real-world setting,” said David Heckler, vice president, CSI.
“Our lab is the first installation of its kind in North America operated by a privately held company; we are using energy-modeling software to analyze VRF performance compared to conventional systems.” Because VRF systems feature a heat recovery mode, energy can be transferred from zone to zone with minimal compressor use.
“We installed two systems, one in our offices and one in our training room, separated by the warehouse and other space,” Heckler said.
“We obviously live in it, and we do training and informational seminars. We have breakfasts, lunch-and-learns, for not only contractors but also engineers, general contractors, and end users. We do all our training there whether it’s VRF related or not, but in a year’s time we might have had 30-40 events.”
The company promotes its events via direct mail and a quarterly newsletter. “It’s absolutely appreciated,” said Heckler. “We’re on two larger jobs, one school and one larger building, where the end user was brought into the lab. We won it by feel and touch.”
Publication date:04/27/2009