
Dave Yates checks system performance during pre-fire at a residential radiant heat retrofit. He used Hydronex panels to reduce time on the job site.
“I defy anyone to show me a building that can’t be retrofitted with hydronic radiant heat,” declared Dave Yates, president, F.W. Behler, York, Pa. “I can come up with a solution for any structure. I can’t think of any situation that would prevent us from being able to install radiant heat.”
While many may dread retrofitting an existing home or building with hydronic radiant heat, Yates relishes the challenge. In fact, he and his crew at the 109-year-old F.W. Behler believe retrofits are far more exciting and fun than installing in-floor radiant heating systems in new construction. “Everybody in our shop feels that retrofitting is where you can show off your skills. If you’ve really got the knowledge and the skills, you can be thrust into any situation and come up with a good solution.”
Skill is definitely an asset when it comes to retrofitting with radiant heat, but manufacturers have also helped by introducing products aimed directly at the retrofit market. These products include low-profile, above-the-floor, modular radiant panel systems as well as flexible tubing systems that install between the joists underneath existing floors. Both are meant to make the retro- fit process a little less challenging - and perhaps a little more fun - for the contractor.
CUSTOMERS WANT COMFORT
The reason why customers are willing to pay more money and put up with the mess that can be involved with a radiant heating retrofit is they want a system that is more comfortable and efficient, said Greg Jannone, owner/president, William Jannone & Sons Inc., Bound Brook, N.J. “Some are put off by the cost, but many want it and are looking for someone with knowledge and experience to put it in. You don’t always have to remove the floor, and in most cases where you do, the homeowner is not put off by that since they were aware of that factor before we started.”Jannone stated that about 20 percent of his radiant heating installations involve retrofits and that sometimes certain obstacles come up that can make a project more challenging, such as finished ceilings or floor coverings. For homes with a forced-air system already in place, Jannone said it is necessary to look at the heat loads and floor coverings to determine the feasibility of a system, as well as how much area is to be done and whether or not the job warrants a boiler.
The heat loss and gain calculation is absolutely crucial in a retrofit situation because it will dictate how the system will be designed, said Yates. “If you’re doing a retrofit, you ask yourself, do you want to cut back on the tubing and raise the water temperature? Or do you add more tubing and lower the water temperature? Our design method is to go for the lowest water temperature possible. It takes less energy to heat water above 100°F to achieve the same goal that I would have if heating water to 180°. We start to see some economical benefits to doing that.”
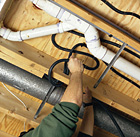
Yates prefers Onix tubing for any radiant retrofit work, especially for staple-up applications. The tubing is swerved and connected to miss protruding nails.
For larger radiant heating retrofits, a dedicated boiler is needed, and as Jannone noted, “A multitude of products may be needed to accomplish the task at hand. There are some great products out there today that we did not have years ago.” Of course, those products come at a price - estimated at anywhere between $12 and $20/square foot - but as Jannone added, “If value is presented to the owners, they will spend the money.”

Dave Yates (foreground) and senior technician Bob Sieger slide Onix tubing into place for joist bay staple-up. The tubing is flexible and can be pinched to go through holes.
MANAGING TEMPERATURE
Existing homes with various types of flooring can be a particular challenge for a radiant heating retrofit, especially when both thick carpet and hardwood floors are involved. Yates encountered this situation recently and noted it was actually an easy problem to solve once the initial heat loss-heat gain calculations were performed. “With hardwood floors, you have to watch the water temperature because you don’t want to do any damage to the wood. Once you have the initial calculation, you know what the tubing value is and how much you’re putting in, so you can tell what temperature water you’re going to need. Programs are also available that tell you what the surface temperature is going to be.”Then it becomes a matter of temperature management. This particular house that Yates retrofitted had multiple temperature zones, and he knew the water temperature needed for the high temperature zone was 140º, with water returning at a temperature of 125º, which happened to be the temperature needed for the second room. The water returning from the second room was at 115º, which was exactly what was needed for the third room, so instead of three circulators and three controllers, he basically treated it as one zone.
“We simply fed water into the first zone, let its return be the feed for the second room, and then let its return be the feed for the third room. When I sat down and crunched the numbers on how many feet of tubing we had, all I had to do was match the circulator up that could meet that heat loss. It became a very simplified method,” said Yates.
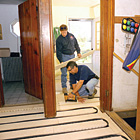
Dave Yates (foreground) and senior technician Bob Sieger complete a SubRay installation as part of an extensive radiant retrofit.
Even though numerous products are now available to make radiant retrofits a little easier, Yates noted he still needed to bounce ideas off fellow contractors and ask for advice on certain installations. That’s why he encourages everyone who is involved with radiant heating systems to join a trade group such as the Radiant Panel Association (RPA). “When you join, you will suddenly have mentors and networking opportunities available to you. I can call all sorts of people around the country to help me out. Unless you’re in an organization that brings you in contact with other professionals, you don’t get those opportunities.”
With winter approaching, owners are more interested than ever in making their homes toasty and warm. Radiant heat fills the bill for many of these individuals, and contractors who know how to design and install the correct systems in these existing homes will find themselves much in demand.
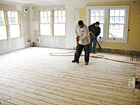
In this home, Greg Jannone retrofitted an existing steam system, converting radiators from steam to hot water and installing radiant heating over the first floor and new master bathroom.
Sidebar: Warming Up
When Alan Deal and his family moved into their 95-year-old home in Plymouth, Mich., about 12 years ago, he added radiant heating to other parts of the home but did not add it to the basement. Two years ago, the basement started leaking after a heavy rain and Deal, who is also an engineer at Performance Engineering Group, Livonia, Mich., knew he would have to permanently fix the problem of water seeping up through the floors. Deal took the opportunity to not only fix the water issues but to remodel the space with radiant heating, so his children could use the basement as a teenage sanctuary.The 900-square-foot basement in Deal’s home includes a combination fieldstone foundation wall, as well as brick walls and other interesting textures, and he preferred to keep them exposed and natural. The floor in the basement - which was probably dirt at one time - was very uneven and subsequently poured over at some point. Given that this was an older structure, any loss of height was a concern, so the thought of doing a pour-over radiant heating system was not an option. For this reason, he decided to use VersaTherm snap-fit radiant floor system.
“We had seen other retrofit systems that incorporated plywood, MDF board, Styrofoam, or plastic, but none of them seemed to be recommended for a site like ours,” said Deal. “I have done quite a few radiant heating installations over the years with just about every system type there is. With VersaTherm, we did very little to compensate for the deviations in floor height and merely made adjustments as to what size piece of the flooring system we used to adjust to the pitch of the floor.”
The existing boiler was large enough to handle the extra load, and Deal noted that it actually works better thanks to the radiant heating system in the basement. “The boiler used to short cycle even on the lowest firing rate and go into a 25-minute timeout condition to prevent the short cycling. The additional load of the basement floor has eliminated the short cycling condition and now the boiler can stay online long enough to satisfy the load.”
Once the radiant heating system was finished in the basement, it was covered with carpet, and the Deal family is quite happy with the results. “The space is much more comfortable, and we no longer need a supply of blankets for any guests who might be watching television down there. We also feel that if we do ever have another water issue, the height of the floor system will help to prevent damage to furniture and other valuables.”
Publication date:10/19/2009