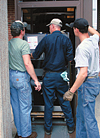
Manufacturers have spent considerable time researching and developing new technologies in order to be able to offer cutting edge commercial boilers.
The winds of change are blowing across the U.S., and nowhere is that more evident than in the commercial boiler market. While manufacturers have traditionally focused on lowering NOx emissions, now they’re looking at ways of reducing other greenhouse gases in response to concerns from government agencies and environmental groups. In addition, they’re researching how to reduce energy costs for end users by increasing efficiencies or even looking at new fuel sources altogether.
Manufacturers have spent considerable time researching and developing new technologies in order to be able to offer cutting edge commercial boilers that feature high-efficiency performance, increased fuel savings, superior control, and low emissions. With the government and end users clamoring for products with this array of benefits, it seems these new commercial boilers will be very much in demand.
BENEFITS OF BIOFUEL
One company that is looking at using alternative fuels in its commercial boilers is The Fulton Companies, Pulaski, N.Y., which was recently awarded a grant from New York State Energy Research and Development Authority to develop an ultra-high efficiency condensing natural gas/B-100 biodiesel fired version of its Vantage boiler.“We’re not necessarily looking at what people are going to want in one to five years, but maybe 10 to 15 years. Fulton always strives for being a part of new technologies, being innovative in different niche markets of all types of heating equipment that people would use, not just in North America but globally as well,” said Erin Sperry, commercial heating product manager, Fulton Heating Solutions Inc.
“We see biofuels as a premiere energy source people are going to be utilizing in the future if, in fact, petroleum type fuels are no longer available or become expensive or difficult to obtain.”

Fulton was recently awarded a grant to develop an ultra-high efficiency condensing natural gas/B-100 biodiesel fired version of its Vantage boiler.
This type of boiler will fill an important niche, because while gas-fired condensing boilers can provide efficiencies over 89 AFUE, most conventional oil-fired boilers are limited to operating at lower efficiencies, due to the corrosive nature of the fuels’ sulfur content. Unlike most fuel oils, biodiesel, derived from vegetable oil, is nontoxic, biodegradable, sulfur free, and when burned, releases less harmful emissions.
“There aren’t commercial size boilers on the market that can condense on No. 2 oil because of the sulfuric acid production associated with the combustion process,” said Sperry. “And if it isn’t possible to produce flue gas condensate, it isn’t possible to get the highest efficiencies from operating the boilers. The ability to condense on an oil that would not result in sulfuric acid production leads to being able to have ultra-high-efficiency condensing boilers with more than just gas-fired options.”
The Vantage boiler fired with B-100/natural gas will be suitable for all commercial applications that could benefit from a dual-fuel option, noted Sperry. The ultra-high efficiency boiler will be placed in beta test sites near the end of this year, and if all goes well, the 3 million Btu version should be available sometime next year.

Lochinvar’s newest boiler, the Sync, features the new Smart Touch control, which utilizes a touch screen display as a user interface.
SUPERIOR CONTROL
Renewable energies are also of interest to other boiler manufacturers, including Peerless Boilers, Bally, Pa., whose Mike McDonnell, director of marketing, noted, “Biofuels and even ultra low sulfur fuels will be a part of the future as will other systems that perhaps will efficiently burn waste oil or other naturally occurring green fuels.”Lochinvar, based in Lebanon, Tenn., is also researching alternative green fuels and, as Stirling Boston, director of marketing noted, “We look forward to sharing more information with our customers in the future about the designs and developments that we are currently working on.” Right now, the company is primarily focused on improved controls, which Boston stated are some of the most exciting and innovative boiler components being developed in the industry at this time.
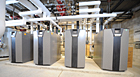
The controls included on Lochinvar’s Sync condensing boiler offer contractors the ability to integrate the product into heating systems with less effort and with more control than has previously been offered. (Courtesy of Tim Inman, Saginaw Valley State University.)
In addition, the controls included on the Sync condensing boiler offer contractors the ability to integrate the product into heating systems with less effort and more control than has previously been offered, said Boston. He added that the modulating condensing design is housed in a compact footprint that features multiple venting options for greater installation flexibility.
These improved control strategies are not only user friendly, they also help combat real world scenarios such as part load heating days; energy saving pumping and piping strategies; system oversizing; and limitations in technology for maintaining the heating system at very low loads. “Due to these variables, we are sometimes not able to operate a complete heating system at efficiencies as high as is desired, however, we will continue to introduce new technologies and controls designed to provide higher realized system efficiencies,” said Boston.

Bryan Steam recently introduced its Triple-Flex ultra high efficiency condensing boiler, which uses a variable speed motor/blower for precise control and energy savings.
The company recently introduced its Triple-Flex™ ultra high efficiency, condensing boiler, which Guth noted uses a variable-speed motor/blower for precise control and energy savings. “We are also using the Honeywell Sola hydronic control to manage the boiler while interfacing with the building management system to change the water supply temperature as needed to reduce the loads on the system pumps, chillers, etc.”
Guth pointed out that since the Triple-Flex boiler is not temperature dependent, it also provides ultra high efficiencies. “Most condensing boilers can achieve efficiencies in the 95-98 percent range when operated with cool return water of 80°F at low firing rates. However these are not real world operating conditions, and when these same boilers are fired at maximum rate with nominal 160° return water and 180° supply, they will return efficiencies closer to 86-87 percent.”
According to Guth, the Triple-Flex boiler delivers a minimal thermal efficiency of 90 percent with the same maximum firing rate with 160°F return and 180°F supply water conditions. The Triple-Flex delivers efficiencies of up to 99 percent with cooler water return temperatures and reduced firing rates when building heating systems are designed and operated with these parameters.
It’s an exciting time in the world of commercial boilers, and there’s still more to come. As Guth noted, “There have been impressive changes in technology over the last five years; I expect greater changes in the next five years.”
Publication date:08/17/2009