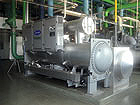
Customers are concerned with the availability of products, and they want to know more about products that are currently available, such as Carrier’s Evergreen 23XRV chiller. (Photo courtesy of Carrier.)
Thirteen years ago when CFCs were phased out, commercial building owners and managers had to make the decision whether to keep their existing chillers that used refrigerant such as R-11 or invest in equipment containing HCFCs such as R-22. Now that HCFCs are being phased out, owners and managers are faced with the same decision: keep their current equipment and most likely pay higher premiums on refrigerant in the future, or move to chillers using HFC refrigerants such as R-134a or R-410A.
It’s a difficult decision to make, especially in this economy; building owners may opt to repair their existing chillers rather than make a large investment in new equipment. Some may also be tempted to hold onto their existing equipment until final decisions regarding cap-and-trade legislation are made, as a current proposal calls for “phasing down” the use of HFCs by 85 percent after 2032.
As for now, equipment containing R-22 can no longer be manufactured after the first of the year, and the decrease in R-22 production allowances as of January 2010 could create some concern for commercial end users. For these reasons, manufacturers have been planning for the phaseout date for many years in order to make the transition as painless as possible for contractors and end users alike.
EASIER TRANSITION
Many industry experts believe that the phaseout of HCFCs will be easier and less dramatic than the CFC phaseout 13 years ago. As Mike Thompson, director of environmental affairs, Trane, noted, “When the CFCs were phased out, use of the refrigerant in new equipment and production of the refrigerant stopped at the same time. With HCFCs, refrigerant will be produced for an additional 10 years beyond equipment production for use in service applications. The end result will be a much easier transition.”Indeed, R-22 will continue to be produced until 2020; R-123 can be used in new equipment until 2020, and the refrigerant will continue to be produced until 2030. Thompson stressed that end users need to understand that there is no phaseout of existing equipment and that equipment containing R-22 can continue to be in use for as long as the end user wants.
Trane has transitioned its scroll chiller products to use R-410A, and the final transition of its screw chiller products to R-134a will be complete in time for the 2010 phaseout date. Trane will continue to use R-123 in its centrifugal chillers for the foreseeable future, given that the refrigerant has a low ozone depletion potential (ODP) and will be manufactured until 2030.

Trane has transitioned its scroll chiller products to use R-410A, and the final transition of its screw chiller products to R-134a will be complete in time for the 2010 phaseout date, including its AquaStream. (Courtesy of Trane.)
John Mandyck, vice president - sustainability and environmental strategies, Carrier Corp., also believes the phaseout should not cause any problems. “We don’t foresee any potential challenges. Primarily, customers are concerned with the availability of products. They want to understand which products are available now with environmentally sound refrigerant and also understand the product developments that will shape future design choices.”
Several years ago, Carrier made the decision to design all its chillers, including Aqua Series air-cooled chillers and Evergreen® water-cooled chillers, with HFC refrigerants such as R-134a or R-410A. Mandyck stated that new chillers designed with HFC refrigerants have the same or better performance than the HCFC models, but the HFC units were designed from the ground up to work with that fluid. “Simply changing from an HCFC to an HFC refrigerant will not provide the same results,” he stated.
Ian Casper, senior program manager, York® brand small-tonnage chiller products, Johnson Controls, agreed that the HCFC transition should not create any new challenges for contractors or owners, although he noted that some customers who recently purchased R-22 may perceive a risk in regard to refrigerant availability for the full life of their equipment. At Johnson Controls, small-tonnage air-cooled and water-cooled chillers have now been transitioned to HFCs, with screw compressor-based chillers using R-134a and scroll compressor-based chillers using R-410A.
York brand large centrifugal and screw water chillers from Johnson Controls all utilize R-134a. Larry Kouma, director of large-tonnage chiller products, Johnson Controls, noted that the phaseout schedule has been set for nearly 20 years, allowing for an orderly transition out of products using ozone-depleting substances (ODS). “This well-defined schedule permitted investments to develop a new generation of products that deliver higher efficiency and lower leak rates than predecessor HCFC water chillers.”

Retrofitting a new compressor into a machine that is in good condition can be a wise investment, but retrofitting a machine with bad heat exchangers isn’t. (Photo courtesy of Danfoss Turbocor Compressors.)
THE RETROFIT QUESTION
One of the big questions that end users and contractors both have is whether or not they should retrofit an existing chiller from an HCFC to an HFC refrigerant. That scenario has major technical implications for both the OEM and the equipment owner, noted Ron Conry, vice president - innovation and business development, Danfoss Turbocor Compressors Inc. “Changing out refrigerants is rarely sufficient, as there are material, lubricant, and component compatibility issues that need to be considered.”That being said, if a chiller is going to be retrofitted to a new refrigerant, Conry recommends changing out the compressor at the same time. “When you simply change out the refrigerant, you can expect a drop-off in performance in both capacity and efficiency, however, if the compressor is upgraded at the same time, then the capacity can be compensated for, and there could possibly be very little difference in performance.”
In the case of a positive pressure machine, when the compressor is replaced with a Turbocor or a set of Turbocor compressors operating in parallel, stated Conry, then no drop-off in capacity should be expected. “But there will be an increase in energy efficiency, whether compared to centrifugal, screw, or reciprocating compressors.”
Retrofitting a new compressor into a machine that is in good condition can be a wise investment, noted Conry, but retrofitting a machine that has bad heat exchangers is a recipe for a dissatisfied customer. “At a minimum, contractors need to eddy-current the tubes and check out the condition of the tube sheet. Air-cooled chillers should be handled with caution. It is very important that the proper planning and investigation be carried out prior to starting the project.”
Kouma agreed that combining a compressor retrofit with a refrigerant replacement might mitigate capacity loss and still provide a cost-effective alternative to complete chiller replacement. “For existing R-22 centrifugal and screw chillers, R-134a is typically the best [retrofit] choice. While this will carry a capacity reduction – which can be as high as 35 percent - the retrofits often result in a higher-efficiency package benefiting from the excess surface area.”
He added that since large water chillers use flooded-type evaporators, they are not good candidates for refrigerant blend retrofits because the refrigerant components can separate. Also, R-245fa, the Environmental Protection Agency-approved alternative to R-123, requires a higher design working pressure and cannot be used with the existing York R-123 equipment.
For small-tonnage chillers charged with R-22, the most likely alternative for a retrofit is the HFC refrigerant, R-407C, said Casper. “Although there is a moderate 5- to 10-percent penalty for capacity and/or efficiency, R-407C has been available for many years for our R-22-based, small tonnage chillers and is therefore a proven option that has many run hours in our equipment. It is worth noting that R-407C is a blended refrigerant, but for small-tonnage chillers with DX-style evaporators, this will not impact performance. No significant modifications would need to be made in this case.”
While alternative refrigerants can generally be used to retrofit older-generation refrigerants with like pressures (e.g., R-12 can be retrofitted with R-134a, R-11 can be retrofitted with R-123, and R-22 can be retrofitted with R-407C), Thompson noted that retrofitting comes at the expense of reduced capacity and efficiency. In addition, Thompson cautioned that owners wanting to retrofit should first make sure their equipment doesn’t leak. “If a piece of equipment cannot contain its refrigerant supply with an HCFC, it will not be able to do it with an HFC. If the refrigerant cannot be contained, replacement should be considered.”
Mandyck is not an advocate of replacing an HCFC with HFC in the same machine, noting, “In the vast majority of cases, a new refrigerant cannot be ‘dropped in’ to an existing chiller, because performance issues result when equipment has not been designed to utilize a specific refrigerant. Unit modifications would be cost-prohibitive.” In addition, he stated that Carrier warranties would not cover utilizing a drop-in refrigerant without authorization from Carrier.

At Johnson Controls, small tonnage air-cooled and water-cooled chillers have been transitioned to HFCs, with screw compressor-based chillers using R-134a and scroll compressor-based chillers using R-410A. (Photo courtesy of Johnson Controls.)
WHAT LIES AHEAD
As noted previously, legislation working its way through Congress could restrict the use of HFCs after 2032 by as much as 85 percent. While it’s anyone’s guess as to whether or not the HFC provision in the Waxman-Markey bill will make it through the Senate, there is some concern that HFCs may be under legislative pressure. So are there alternatives to HFCs, and if so, will they be available any time soon?According to Thompson, alternatives are being developed to replace existing HFCs, including one that will replace R-134a for automotive air conditioners in Europe beginning in 2011. “These new-generation HFCs offer a very low global warming potential (GWP) while also allowing for safe and energy-efficient applications. The natural refrigerants, such as CO2, ammonia, and hydrocarbons have a place for use as refrigerants, but due to safety concerns and efficiency limitations, the fluorocarbons are still a preferred choice for most of the HVAC applications.”
At Johnson Controls, product teams continuously investigate the latest technologies and alternatives. “Our refrigeration businesses have utilized ammonia, hydrocarbons, and CO2 as refrigerants for more than 100 years, giving us significant expertise in alternative refrigerants,” noted Kouma. “While refrigerants like ammonia and isobutane deliver very high refrigerant cycle efficiency, they are prohibited in many markets by local codes and regulations related to toxicity and flammability.”
Mandyck stated that Carrier has made substantial progress on both ozone protection and climate change with substitutes to CFCs and HCFCs. “We continue to look at all available alternatives to provide environmentally sound and energy-efficient products and solutions.”
While it will be interesting to watch as Congress continues to haggle over phaseout schedules and refrigerants, manufacturers will continue researching and developing new products that follow government regulations and provide the best efficiency and value to their customers.
Publication date:10/05/2009