WATER SUPPLY
The majority of ice machine problems are the result of a machine’s water supply. Up to 70 percent of problems can be traced back to poor water quality, slow water fill, insufficient water supply, or no water supply. Water also is a critical factor for an ice machine to perform at peak efficiency.Simply put, the better the quality of the water, the better the quality of the ice product. When problems with the water supply are present, the ice produced may be smaller or irregularly shaped, and the ice machine’s production capacity can be reduced. The taste, odor, and clarity of the ice can be negatively impacted.
For example, water with high levels of chlorine can corrode metal and stainless steel parts inside the ice machine. Chlorine also can add unwanted taste and/or odor to the ice, which adversely impacts beverages in which the ice is used. However, chlorinated city water does have its benefits: The chlorine acts as a sanitizer that can eliminate harmful bacteria and other microorganisms.
Particulates in ice can be introduced to beverages as the ice melts, and can cause clogging and abrasion while passing through the ice machine. Particulates, which restrict water flow to the ice machine, are found in hard water that is not filtered.
Lime in the water supply is a common concern in some areas of the country. When water containing lime is frozen, the heavier metals fall out of the water during the ice-making process and are left behind in the machine. Lime builds up on surfaces inside the ice machine and acts as an insulator on the refrigerated surface. This buildup causes the machine to work harder to make the ice.
Hard-water conditions in some facilities necessitate the use of a water softener. Because salt is added to the water during the softening process, ice machines must work harder and longer to freeze the water. The salt content of softened water also negatively impacts the taste of the ice product.
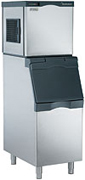
Water is a critical factor for an ice machine to perform at peak efficiency. (Photos courtesy of Scotsman.)
FILTRATION BENEFITS
Ice machine manufacturers recommend that all end users install water filters on their ice machines. Without a water filter, poor water quality can cause ice cubes to stick on evaporators during the harvest sequence, resulting in freeze-up or even failure of major components. A filter can be well worth the investment.Note that it is important to use the correct type of filter. For example, installing a residential filter for a commercial application is a mistake. Residential filters do not have the capacity to filter the water supply required for commercial ice machines. Also, don’t install a water filter that doesn’t address the specific problems associated with the water supply (such as installing a filter for hard water when chlorine levels are the real problem).
Some water filters remove unwanted tastes and odors from the water to improve the ice product. Most commercial water filters remove the off-taste caused by chlorine. Higher-quality filters can remove up to 90 percent of the chlorine by using activated carbon technology. Other filters remove particulates associated with hard water.
Minerals, such as lime scale, can wreak havoc within ice machines and any other water-related piece of equipment. The best way to remove minerals from the system is to keep the minerals suspended in solution to reduce scale from building up on the metallic parts. Different scale inhibitors in the water filter can accomplish this.
THE ENVIRONMENT
It’s important to select a water filter that meets the specific needs of each application. This is why ice machine manufacturers do not sell equipment with built-in water filters.Operating environments vary greatly in different areas of the country and between applications. For example, in applications where the ice machines are located near ovens used to bake bread, a filter must be installed to remove yeast bacteria, which can negatively impact ice machines and ice product. Facilities that serve beer might encounter similar solutions.
All of the environmental factors related to location and water supply must be considered before the correct water filter can be identified.

To improve water conditions, use of water filters is recommended on ice machines.
CLEANING, SANITIZING
Even with the best water conditions, every ice machine should be cleaned and sanitized at least twice a year. In some applications, where air or water quality is poor, machines must be cleaned more often. Even ice machines equipped with purge valves must still be cleaned at a minimum of every six months.Some ice machines feature an external light to indicate when they need to be cleaned, based on hours of operation. End users or technicians have the ability to schedule three-, four-, five-, six-month, or one-year cleaning schedules based on the environment. The light serves as a reminder to clean and sanitize the machine, as well as perform any necessary planned maintenance.
Cleaning and sanitizing processes for an ice machine include circulating a cleaning solution through the water system to remove buildup, as well as to sanitize. Technicians should break down the water-related components in the machine. The sump that holds the water must be cleaned and mineral scale re- moved. The evaporator and every other component that comes in contact with water also should be cleaned and sanitized.
It’s important to use the right cleaning solution, which depends on the type of evaporator used in the equipment. Machines with a nickel-plated evaporator require a special cleaning solution designed to not damage the metal. If a special cleaner isn’t used, chemicals could burn the nickel off the evaporator. Older ice machines use copper-tin-dipped evaporators; full-strength cleaner can be used on this equipment.
Options are available on select ice machines to help improve maintenance. For example, to keep ice machines cleaner longer, some machines feature built-in antimicrobial protection. Antimicrobial compounds are molded directly into machine components, such as the water distributor, to reduce the growth of microorganisms such as bacteria, mold, and algae.
Additionally, some ice machine systems use adaptive purge control, which can help extend the time between cleanings. This technology detects hard-water conditions by measuring conductivity in the water within the sump, and adjusting to purge mineral-laden water as needed. Purge control reduces scale buildup within the machine.
By evaluating the ice machine’s operating environment, technicians can help ensure that the equipment operates at peak performance. Water conditions and the location of the equipment are key factors that impact ice machine water filter selection, cleaning and sanitation schedules, and other maintenance tasks.
Publication date:07/05/2010