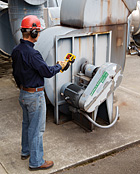
Thermal imagers offer a quick way to inspect equipment for abnormally hot-spots, and piping for abnormally cool spots.
[Editor’s note: This is part one of two in a series on infrared thermal imagers.]
Have you ever taken the rap for an expensive failure after you performed routine maintenance? Have you ever wished for a crystal ball to see into the future, or just to see things your traditional test equipment and eyes couldn’t reveal?
Compared to traditional test equipment, a thermal imager may seem like a crystal ball. By taking our visual sight capabilities beyond the visible spectrum to the radiated heat spectrum, we begin to see predictive qualities that do indeed foretell future likelihoods.
Thermal imagers operate in the infrared spectrum and follow the same laws as infrared thermometers, but the similarity ends there. Infrared thermometers report an average spot temperature. Infrared thermal imagers are similar to digital cameras and, in practical terms, may be thought of as infrared cameras. An LCD shows a “movie” of the infrared image as the user selects the image, focuses, then pulls the trigger to record the image.
(In addition to highlighting temperature variations and hotspots in real time through the LCD, Fluke says its thermal imagers with IR-Fusion® technology fuse a visual, or visible light, image with an infrared image for better identification, analysis, and image management. Even with that, the power of thermal technology is not fully realized until the recorded image is downloaded to a computer, analyzed with the necessary software, and saved in a comparative database along with descriptions, notes, and an actual photograph to compare the infrared with the visual image.)
Thermal imaging is gaining an invaluable predictive and diagnostic reputation in industries such as power distribution, plant maintenance, petrochemical plants, and process applications, to name a few. But what industry is better suited for thermal imaging than the thermal dynamic industry of HVACR?
Dynamic heat analysis can be made of moving parts (motors, bearings, sheaves, and belts); electrical circuit quality (starters and contactors, disconnects, fuses and buses, electrical connections); duct heat loss or span; conditioned envelope heat loss or span; tracing membrane roof leaks; compressor operating condition (relative head, sump, suction, discharge temperatures, and unloader or hot gas bypass operation); analysis of steam traps, radiators, and convectors; radiant loops; or any process that can reveal the integrity of the process by comparative temperatures.
The full range of HVACR applications for thermal imagers will only be realized once they are in the creative hands of HVACR technicians.
USING A THERMAL IMAGER
An HVACR technician interpreting a thermal image is similar to a doctor interpreting X-rays or MRIs. This may sound ominous, but you already have the HVACR knowledge and experience to know what you are looking for. Just add a few facts about the nature of thermal imaging and you’re home free.Infrared energy is just beyond the visible energy spectrum. Radiated light is reflected off of surfaces or emitted from sources that our eyes receive and our brains interpret. Infrared energy is heat radiated by or reflected from a material; energy that our eyes cannot see. Our skin is the best sensor of infrared energy. We feel the heat from a fire. We feel the heat loss when standing close to a cold wall.
A thermal imager interprets infrared radiated or reflected heat by assigning a visible graduated color, or gray scale, to a radiated portrait of the scene. This allows us to see a visible representation of the unseen infrared spectrum. What visibly looks like a disconnect in good operating condition may be revealed as an L2 pole operating 35°F hotter (red) than the L1 pole (blue) - equal loads but different temperatures. This disconnect has a problem that couldn’t be seen, yet the thermal imager takes a picture of the entire device and its electrical connections with comparative temperatures.
All real-world materials absorb, reflect, and transmit infrared energy depending on their physical properties. When expressed as a formula:
Infrared Energy = Absorption + Reflection + Transmission
Whatever infrared energy is absorbed will be equally emitted. We do not encounter materials in the field that perfectly absorb and emit all infrared energy. A material that absorbs all infrared energy is called a “black body” and has an emissivity of unity.
Most materials of interest that we encounter are called “gray bodies,” since they are not perfect emitters - close maybe, but not perfect. Transmission through solids can usually be ignored in field work, with the exception being glass and plastic films, referred to as “nongray bodies.” This simplifies our working formula to:
Emissivity = 1 - Reflected Background
The impact of reflective background is inversely proportional to emissivity. The more an object reflects infrared energy, the less it emits. Reflectivity can be relatively judged according to our sight determinations of reflectivity. Polished chrome has a very high reflectivity and low emissivity. Brushed stainless steel has less reflectivity and more emissivity. Tarnished brass and copper have even less reflectivity with proportionately more emissivity. Most painted surfaces have very high emissivity and negligible reflectivity.
QUALITATIVE vs. QUANTITATIVE
Most thermal imaging tasks are qualitative as opposed to quantitative. Quantitative is accuracy of temperature, and qualitative is relativity of temperature. When viewing a contactor for instance, the interest is in the temperature difference of the 12 contact points. Are the electrical connections all the same temperature (T1-L1, T2-L2, T3-L3)? Are the temperatures consistent between the fixed and movable contacts (T1C-L1C, T2C-L2C, T3C-L3C)? Seeing one point of elevated temperature directs us to a poor electrical connection or failing contactor points without being concerned that the reported temperature is off by some percentage.Painted surfaces have high emissivity and a very small margin of quantitative error. So our thermal image of a compressor, motor, bearings, steam traps, transformers, etc., will tend to be fairly accurate without taking the steps to fine-tune imager emissivity.
•Adjusting emissivity and reflected background:Thermal imagers have adjustments for both emissivity and reflected background. Both are easy to measure and compensate for when the need for quantitative readings outweighs qualitative readings.
•Level and span:Level and span represent the expected target temperature (level) and the differential from target temperature (span). If level were set to 100° and span were set to 25°, the temperature range would be limited to 75° to 125°. Thermal imagers automatically select the best level and span of the target. Set at automatic, the imager displays the highest and lowest temperature values in the scene. The minimum and maximum values of the scene define the extremes of the color palette.
A white spot would not necessarily indicate a very high temperature, only the highest temperature in the scene. The highest temperature in one scene may be 90°, while another scene may have a white spot indicating 250° if it is the highest temperature in that scene. The palette is proportional to the temperature range of the scene, not a fixed value. A slight relocation of the spot on the target can change the gradient display, depending on the range of temperatures now in the scene.
Keep in mind that thermal imagers measure surface temperatures only. The interpreter of the images must understand what is happening beneath those surfaces in order to make accurate judgments. Temperatures of materials with differing emissivities within a scene will not report temperature relationships equitably. Digital photographs of the same scene as the thermal image are useful not only for scene identification purposes, but also to identify materials of differing emissivities within the scene.
Sidebar: Terminology
•EMISSIVITY:Infrared energy emitted from a body indicating the heat of that body. Emitted infrared energy equals absorbed infrared energy.•INFRARED ENERGY:Heat energy beyond the visible spectrum. Infrared thermal imaging devices designed for field use generally detect infrared wavelengths 7-14 micrometers, wavelengths slightly longer than the color red. Infrared energy equals the sum of emitted, reflected, and transmitted energy.
•QUALITATIVE TEMPERATURES:Accuracy of temperature is secondary to relative temperatures. This is the most common use of thermal imagers.
•QUANTITATIVE TEMPERATURES:Accuracy of temperature takes precedence.
•REFLECTED BACKGROUND, or REFLECTIVITY:Ambient infrared energy reflected from a body unrelated to that body’s own heat.
•TRANSMISSIVITY:Infrared energy transmitted through a body such as a gas or liquid and some solids such as glass or plastic films. For most solid bodies, transmissivity is zero.
Publication date:05/10/2010