
Figure 1. A direct expansion system is most prevalent in commercial refrigeration as it is simplest in design. The basic components of a DX refrigeration system are a compressor, condenser, flow control (expansion valve).
[Editor’s note: The author is group manager - product management for Heatcraft Refrigeration Products, a subsidiary of Lennox International. At Heatcraft, she is responsible for product management, leading product development projects and market research for commercial refrigeration products and market segments.]
The global supermarket industry is becoming increasingly committed to preserving the environment. One indicator is the existence of corporate sustainability programs. According to the Food Marketing Institute (FMI), over two-thirds of supermarkets have a corporate sustainability program in place or have plans to begin one within two years. As part of these sustainability programs, many supermarkets are taking a closer look at their refrigeration systems in an effort to reduce the overall environmental impact of their stores.
Over the last few decades, synthetic refrigerants such as CFCs and HCFCs are being phased out by regulation. Increasing concern and regulatory actions related to the environmental impact of HFCs has prompted a re-emergence of CO2 based refrigeration systems and other low Global Warming Potential (GWP) solutions around the world. CO2 based refrigeration is of interest due to low GWP, low price, potential for energy reduction, non-toxicity, and a positive safety rating.
The following story looks at CO2 applications - then and now.
IN THE PAST
The first mechanical refrigeration system using CO2 as a refrigerant was introduced in 1866 by aeronaut, scientist, and inventor T.S.C. Lowe. It was promoted as a “safe” refrigerant compared to the more noxious alternatives - ammonia and sulfur dioxide - and quickly gained popularity with use peaking in the 1930s. In the late 1930s, CO2 was replaced in commercial refrigeration by a new refrigerant called “freon.” That refrigerant was also considered safe, but operated at much lower pressures and required refrigeration components that were less expensive to fabricate.Over the years, a multitude of CFCs and HCFCs have been used in commercial refrigeration. But then the Montreal Protocol banned CFCs in 1996 and set in place a phaseout schedule for HCFCs.
The majority of the U.S. commercial refrigeration industry then moved to HFCs such as -404, -507, -410A, and –134a. While HFCs have zero ozone depletion potential (ODP), they have a high GWP. There is also a new, emerging class of refrigerant, Hydrofluoro olefins (HFO), which are low GWP, but are still in the early stages of commercial evaluation.
TODAY
There is an emergence of programs building awareness of and the need to reduce refrigerant charge in order to minimize the risks associated with any potential refrigerant leaks. Some regions of the world, such as Europe, have already imposed caps on HFCs and it is expected that the United States and Canada will follow suit. As a result CO2, which has zero ODP and a GWP of 1, is gaining renewed interest for refrigeration applications.As refrigerants with very low ozone depletion potential become more commonplace, the concern has shifted to the global warming potential of refrigerants. Refrigeration systems contribute to global warming directly through refrigerant leaks and indirectly through CO2-equivalent emissions resulting from energy needed to operate the system. The vast majority of the global warming is a result of the indirect contribution (power generation), not the direct contribution (leaks). Industry experts have recently agreed to a model that takes into account both the indirect and direct impact of greenhouse gases on global warming. This model, Life-Cycle Climate Performance (LCCP), provides a holistic approach to estimating greenhouse gas emissions during the lifetime of a product.
Supermarket refrigeration systems can contain up to 5,000 pounds of refrigerant and the industry average leak rate is 23.5 percent, according to a 2008 statistic from the U.S. Environmental Protection Agency (EPA). FMI reports that refrigeration systems account for nearly one-half the electricity consumption in a typical supermarket, which is an indirect contributor to global warming.
Currently, the primary driver for using CO2 refrigeration systems in the United States is to support the overall goals within the supermarket industry toward lower refrigerant charge and lower leak rates. It is anticipated in the near future that carbon footprint will be regulated and reported in financial statements for public companies and carbon credits traded as is, or will soon be the case in other regions of the world, which will further encourage supermarkets to consider CO2 refrigeration systems.
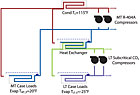
Figure 2. When the low side loop is direct expansion, the CO2 is completely evaporated and only vapor exits the evaporator, meaning superheat exists at the exit. A compressor is used to circulate refrigerant.
CO2 AS A REFRIGERANT
As a result of the movement toward low ozone depletion potential and low GWP, alternative and natural refrigerants, including ammonia, hydrocarbons, glycol and carbon dioxide, are gaining interest.In addition to its efficiency, CO2, also referred to as R-744, is currently viewed as a viable alternative to HFCs for low temperature applications in supermarket refrigeration as it carries a high safety rating because it is non toxic (within a ventilated space) and non-flammable. It is also non-ozone depleting. CO2 has a very low GWP base value of 1 and is a low cost alternative to HFC or hydrocarbons refrigerants. As a result of its physical properties and high volumetric cooling capacity, CO2 technology naturally lends itself as a viable option for all refrigeration processes.
Carbon dioxide is different from other refrigerants in many ways. Key differences are higher volumetric capacity and high operating pressures. At pressures below 75 PSI (5.2 bar) and a temperature of -56.6°F (-49.2°C), CO2 will turn into a solid. In the subcritical phase, CO2 is similar to HFC refrigerants except that it has very high pressure. At a room temperature of 77°F (25°C), the pressure of CO2 is 913 PSI (62 bar).
At temperatures above 88°F (31°C), the density of liquid and vapor are identical, and liquid CO2 cannot be distinguished from vapor. Because vapor CO2 cannot condense into liquid, in this state the properties of temperature and pressure are no longer related. This is called “supercritical.” Carbon dioxide in the supercritical phase operates best in a high-pressure range (1,600-2,500 PSI). Transcritical CO2 systems, which can operate in the supercritical range, are more efficient when operated in the sub-critical range. That is why transcritical CO2 systems are more widely accepted in regions where ambient temperatures are frequently below 88°F (31°C).
Carbon dioxide has a very high volumetric capacity, as much as five or six times HFCs at medium temperature. This means that the same volume of CO2 can absorb much more heat than HFCs; therefore, much less CO2 is required to provide the same cooling effect as HFCs. The pressures at which CO2 operates are much higher than the working pressure of most common refrigeration components which are designed for pressures of 400 to 650 PSI, which means that special attention must be taken in designing the system and selecting appropriate components.

Figure 3. An approach for subcritical CO2 is pumped fluid, commonly referred to as secondary loop.
IN A SYSTEM
A refrigeration system using CO2 as a refrigerant is similar in nature to a refrigeration system using HFC refrigerants. A key difference is that CO2 operates at higher pressures.In general there are two categories of refrigeration systems - non-cascade and cascade.
All non-cascade systems contain a single compressor based refrigeration loop and heat is rejected to the ambient. Non-cascade systems can be direct expansion or transcritical.
A direct expansion system is most prevalent in commercial refrigeration as it is simplest in design. The basic components of a DX refrigeration system are a compressor, condenser, flow control (expansion valve) (Figure 1). A direct expansion refrigeration cycle is not suitable for application with CO2 because at room temperature it is subcritical and high pressure (913 PSI/62 bar).
A transcritical CO2 system operates in transcritical mode whenever refrigerant is above 88°F. Transcritical systems operate at higher pressures (maximum 2,100 PSI) than HFC systems. The condenser becomes a gas cooler at temperatures above 88°F and the CO2 leaving the evaporator is supercritical, a state where vapor cannot condense and one cannot distinguish liquid from vapor.
A key benefit of a transcritical system is that it totally eliminates HFCs from the system, thereby eliminating high GWP refrigerants. This reduces the direct component of global warming.
A disadvantage of transcritical CO2 systems is that components capable of being operated safely in such high-pressure environments can be more expensive. Another disadvantage is that systems designed for transcritical CO2 are less efficient when operated in warmer ambients, as is common in most regions of North America. These are the primary reasons why transcritical CO2 systems are rarely installed in North America.
At temperatures below 88°F, the CO2 is subcritical and the system is similar to a direct expansion system. A transcritical-designed system is also capable of operating as subcritical and is more efficient when doing so.
A cascade CO2 system is a system made of two refrigeration circuits or loops working together as a single system, but using two different refrigerants. These loops never intermingle.
One loop is always a compression loop (i.e., DX) and interfaces with the ambient. Typically a refrigerant, such as R-404A, ammonia or hydrocarbons, is used as the working fluid. The other loop is circuited through the evaporators to cool the load that needs to be refrigerated. This loop uses CO2 on the low side loop and an HFC on the high side loop to keep the CO2 in the sub critical pressure range (maximum 600 PSI). CO2 in the subcritical range in a cascade system can be direct expansion (DX) or secondary loop.
When the low side loop is direct expansion, the CO2 is completely evaporated and only vapor exits the evaporator, meaning superheat exists at the exit. A compressor is used to circulate refrigerant (Figure 2).
The primary benefit of a subcritical cascade DX CO2 system is reduced refrigerant charge. Components suitable for these operating pressures are more readily available and therefore more affordable than those needed for a transcritical CO2 system. In fact, standard components can typically be used. This type of system avoids high pressures associated with a transcritical CO2 DX system, keeping operating pressures in the range of a traditional HFC system (approximately 450 PSI), which can minimize safety issues.
Another approach for subcritical CO2 is pumped fluid, commonly referred to as secondary loop (Figure 3). The key difference between this and a DX system is a pump is used to circulate the refrigerant instead of a compressor. An excess of refrigerant is provided to the evaporator and only a portion is evaporated, so both liquid and vapor exit the evaporator and there is no superheat. This is also referred to as a flooded coil.
BENEFITS
While there are several different approaches, there are numerous benefits of using a CO2 refrigeration system:•High volumetric capacity:reduced compressor and pipe size;
•Low HFC refrigerant charge:HFCs are eliminated or restricted to a machine room; therefore, line runs are shorter and overall volume is minimized;
•Lower HFC refrigerant costs:CO2 costs are currently 90 percent less than traditional refrigerants;
•Reduced carbon footprint:CO2 has GWP of 1 vs. HFC GWP of 3,300;
•Reduced carbon emissions:because refrigerant is confined to a machine room, there are fewer braze joints and a significant reduction in potential for leaks in the system.
Additionally, various studies cite benefits of better temperature control due to smaller and warmer pipe temperatures, reduced installation cost, and space savings due to smaller line sizes and reduced copper piping, and energy savings potential.
A coil circuited for CO2 fits into essentially the same cabinet as any other unit cooler, but the circuiting is different. An installation should include provisions for additional cooling of the CO2 to keep CO2 under 88°F at all times in the event of a power outage. Additionally, while CO2 is plentiful, lead times can be long, so customers will need to keep a sufficient charge on site, particularly in remote areas.
One of the biggest concerns about CO2 as a refrigerant is related to safety. With CO2, a small increase in temperature results in significant increases in pressure. Most building codes require a more complex pressure relief system and a means of pressure relief in any portion of the system that can be isolated.
The system should also be designed to vent CO2 directly to the atmosphere to prevent personal injury in occupied spaces. Systems do require additional controls such as detectors and alarms to ensure safe operation since CO2 is odorless and colorless. These additional controls may add cost and complexity to the system, compared to a traditional direct expansion system.
Successful installation relies heavily on organizations establishing clear design criteria to understand every aspect of the design. Support materials and information such as pressure drop calculators, capacity, and circuiting are needed. Finally, installing contractors and staff who will work with the system will require special training.
Once more experience is gained with CO2 systems, it can be expected that upfront costs will decrease.
TRACK RECORD
Some two dozen CO2 based supermarket installations have been completed successfully in the United States, along with many more across the globe. Additionally, future legislation may make it difficult to cost effectively operate a supermarket with high GWP refrigerants. Outside North America, in regions such as Australia, HFCs are coming under increasing scrutiny and are already being subject to more stringent regulation. This will likely further drive the supermarket industry across the globe toward natural refrigerants such as CO2.For more information, go to www.thecoldstandard.com for information on CO2 as used in supermarket refrigeration, specifically Bohn unit coolers.
Publication date:09/06/20110