
This four-zone sheet metal job has a controller that uses screwless terminals, LEDs, and a temperature display to receive information from four thermostats, control equipment, and open-and-close dampers.
Residential zoning systems have come a long way in recent years, both in terms of the equipment itself, and in an increased understanding of how to apply it correctly. Yet there are still many misconceptions about these systems that zoning experts are trying to dispel. These experts emphasize that zoning systems are increasingly installed in retrofits as well as new construction; that they improve airflow control; and that they are not necessarily for a comfort customer or an energy-saving customer.
Don Prather, technical services specialist for the Air Conditioning Contractors of America (ACCA), said the top misconceptions about residential zoning are that it always saves energy; that zones can be designed properly without doing a Manual J8 load calculation; that installing a zoning damper and additional thermostat to an existing system always improves operation; and that zoning always solves all of the comfort issues on an existing HVAC system.
Dick Foster, president of ZoneFirst Corp., said the misconceptions are that it can’t be done or does not work; that nobody wants it or will pay for it; that it’s too expensive; and that it’s easier to put in multiple units or a mini-split.
“Most contractors want to take the quick in and out, and not take the time to run a load calc, look at the existing system, and try and fix it,” Foster said. “However, hydronic zoning with zone valves and circulators has been done for years. It works for boilers, and a boiler, circulators, and zone valves are more expensive than a furnace and zone dampers. People pay a lot more for in-floor zoned radiant heat than a forced air zoned system.
“It is long overdue that zoning should be recognized by the HVAC industry and energy regulators as a simple solution to save energy,” he continued. “No one would think of only having one light switch for their entire home, but we do this with heating and cooling when we only have one thermostat.”
RETROFIT SITUATIONS
“The first misconception is that the need for zoning is driven by architecture,” said Dennis Laughlin, Arzel Zoning. “Most people believe that two-story houses, large homes, or homes with cathedral ceilings are the [ideal customers].“While architecture is a great indicator, the people who occupy the space determine the need for conditioning,” he said. “So if your investigation process does not include some time to seek out your customer’s issues and expectations, you may walk right by a 1,800-square-foot ranch home that is a prime candidate.”
In retrofit situations, zoning should be considered part of a total solution. “Zoning will not cure oversized equipment,” Laughlin said. “Zoning cannot overcome improperly sized or fitted ductwork. Zoning cannot make up for inadequate return air. However, for many homes where these issues exist, the help zoning can provide is valuable, even if it is not a total cure.” He referred to it as an “economical partial solution that specifically targets comfort problems [which] are welcomed by consumers.”
As for the misconception that zoning is not cost effective for retrofits, Shawn Grennan, managing director for Advector Systems, acknowledged, “Historically this may have been the case, as contractors were left with very few options that did not require manipulating the existing duct-work, cutting into drywall, or spending hours running additional electrical lines.
“The good news is that new technology, such as wireless mesh communications and energy-optimizing software, allows contractors to retrofit an entire home in only a few hours, and with no need for electrical or structural rework.”
Advances in zoning technology allow contractors to offer customers “flexibly priced options to fit different comfort, energy-saving, and budget goals for retrofit projects,” he said.
Tim Storm, controls and zoning product manager for Ingersoll Rand Residential Solutions (of which Trane is a business segment), said the Trane ComfortLink II thermostat offers retrofit-friendly features, such as easy-install color coding, automatic sensor detection, and troubleshooting using wireless technology. “It can be used with any standard HVAC system with the addition of a relay panel accessory,” he added.
This control is also wireless, offers weather data, and can work with utilities to track time-of-day rates. “The platform allows us to partner with utility demand-response programs” to help control peak loads and provide energy management, Storm explained.

Inside a four-zone sheet metal system.
ENERGY VS. COMFORT
Another common misconception among contractors is that they need to quote energy savings to sell zoning. According to Laughlin, “Most consumers purchase zoning for comfort reasons. Homeowners buy a home with an implicit guarantee of comfort, only to find out that in most cases that goal is a work in progress.”Zoning can help consumers utilize their homes more fully through improved comfort, and doing this “will likely lead to energy savings,” he said. “However, these results are dependent upon other factors that perhaps are not in a contractor’s control.”
Grennan pointed out a similar misconception - that the only benefit from zoning is enhanced comfort. “Again, this may be true with traditional methods of zoning that are only able to create large, multiroom zones, but new zoning systems have the ability to control airflow and energy use on a room-by-room basis - and give homeowners the ability to use the HVAC system like a light switch.”
“The No. 1 benefit is even temperature throughout the home,” said Storm. “Energy saving is the second part - but it might not happen. You need to have the right programming.”
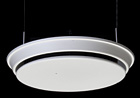
The inVENT wireless zoning damper for new construction applications.
DESIGN AND AIRFLOW
When zoned systems do not seem to live up to their potential, there are many possible causes, said Prather. These may include duct sizing, equipment selection, load calculation considerations, overblow-bypass-relief air system design, damper design and control, humidity control, stratification and air buoyancy, and “lifestyle-related operating choices of the user versus the as-built design’s limitations.”Regarding bypasses, Laughlin said, “While it is true that zoned systems will run at a higher static pressure that does not in and of itself compel the practitioner to install a bypass, in moderation, increasing static pressure in the supply trunk will have positive effects.” According to Laughlin, increasing static pressure will:
• Increase the velocity of the air in the open branches, thus increasing the throw at the registers and better destratifying the space. “If there are areas that were hard to serve before (i.e., the bonus room a long way from the equipment), the extra pressure will provide the force to push the air up the hill.”
• Slow down the air through the equipment, increasing the amount of Btu being squeezed into each cfm. “Now the system is delivering cooler, dryer air (in cooling mode) and warmer air (in heating) into the space.”
Adding a discharge sensor to supervise airflow will allow the application to be a well-controlled system, Laughlin noted. “Zoned systems only require bypasses when the increased velocity causes objectionable air noise in the space.”
Many contractors also still have the misconception that “you can’t zone variable-speed equipment.” Laughlin explained, “Zoning controls today are much more sophisticated and flexible than previous models. In zoning we often refer to the ‘other IAQ’: indoor air quantity. Solving the communication process with blowers and staging routines is about understanding how much of a given home is calling for service.”
Another misconception is that “zoning systems with bypass do not need an adjustable low/high temperature cut-out sensor,” said Greg Talley, Comfort Products, Inc. “Bypassed air can cause the supply air to get too cold or too hot. When this occurs, a supply air temperature sensor can de-energize the equipment so that the supply air can warm or cool before the equipment restarts.”
In earlier times, he said, “Dampers were oversized so that all of the air would dump into the zones that were open. If this occurred, too much very cold or hot air was being dumped into a few rooms that could not comfortably accommodate all of the system’s capacity.
“If ducts are correctly sized and the bypass correctly controls the supply plenum pressure, then the right amount of conditioned air will be delivered into the zone,” he explained. “The adjustable temperature sensor will not allow the system to operate out of a safe and efficient range, so balance is achieved.”
The condition of the duct system is understandably critical. “If you have a really poor duct system - totally undersized for example - you may need to modify it,” said Storm. “At some point, there are duct systems too poor for any zoning system to overcome.” He recommended properly sized ductwork based on ACCA’s design guideline.
For handling excess air, Storm said, “Some people do have a dump zone, an unused area. There are ways to do it. But managing the excess air is the biggest issue, especially in single-stage equipment. We use modulating dampers, power-open/power-closed, with incremental modulation.”
When there is a standard PSC system and a contractor closes off a vent, “you’re getting less capacity on the higher static system,” Storm said. “Our system measures the static so that it doesn’t go over a certain static pressure in the ductwork.”
An equipment-related misconception is that zone dampers should be powered closed and spring open, said Talley. “Unreliable damper motors are the No. 1 service call on a zoning system. This was taught to contractors early on because power-open, power-close damper motors were more expensive than they are today.
“Power-open/power-close motors are considered ‘commercial’ and are much more reliable,” he said. “Today’s power-open/power-close motors will muster 18 inch-pounds of torque using less than 3 VA of power.”

The inVENT wireless zoning damper for new retrofit applications.
ACCEPTANCE
Contractors need to overcome the “too much trouble” mentality, said Storm. “Now zoning systems automatically set airflow and detect dampers. At night, the system automatically evaluates cfm/zone and checks each zone multiple times.”But do customers understand how to use zoning? “Consumers surround themselves with technology to make their lives more comfortable and efficient,” said Grennan. “Cell phones, mobile computers, and WiFi at the local Starbucks is what today’s consumers are looking for.
“Contractors who take the time to understand the new breed of available zoning products will find touchscreen user interfaces, preset schedules, wireless communications, and on-demand priority adjustments,” he said. “In today’s environment of advanced technology, homeowners expect their contractors to present these types of solutions.”
“Zoning takes education and time,” said Foster, “which very few are willing to take the time to learn how zoning is the most effective way to save energy. Most experts agree that the HVAC furnaces and air conditioners are extremely efficient, and it’s the distribution system that still needs to be fixed. This is up to the installer.”
One way to make the distribution system more efficient, he said, “is to zone it and stop wasting energy in zones that are not being used or are already comfortable. Studies have shown zoning can save as much as 30 percent when operated properly.”
Not becoming better versed in the technology can lead to missed opportunities for contractors, said Grennan. “Zone control, using new advances in technology, can provide customers with new options, and contractors with a new source of revenue. Just about every homeowner has a room, or multiple rooms, that are rarely occupied or always feel way too hot or too cold.”
For more information, visit www.acca.org, www.advectorsystems.com, www.arzel.com, www.comfortproductsinc.com, www.trane.com, and www.zonefirst.com.
Publication date:05/16/2011