Now more than ever, modular and prefab construction are playing critical roles in delivering creative, sustainable solutions in the building industry. While the concepts are not new, they have been fleeting, until now. According to McKinsey’s Modular Construction: From Projects to Products report, thanks to enhanced technology and a changing economy, they’re likely sticking around.
If you’re smart, today’s rigorous project schedules rely on prefabrication to complete on-site work in shorter time frames. The ability to build multi-trade construction modules that include plumbing, HVAC, piping and electrical systems all in one unit make installation faster and easier. On-site mechanical work is reduced, resulting in smaller crews and shorter durations. As a result, labor savings can often be directly passed on to the customer. When labor can be moved to a regulated fabrication facility, jobsites also become safer as hazards and distractions are reduced. Requirements include locating the machine, uncrating it, running air and electric to it and hooking up the exhaust.
Skilled workers produce prefabricated items to exact specifications in a controlled environment where they can be carefully stored to prevent damage. Just-in-time delivery capabilities also help manage site constraints on jobs with limited storage.
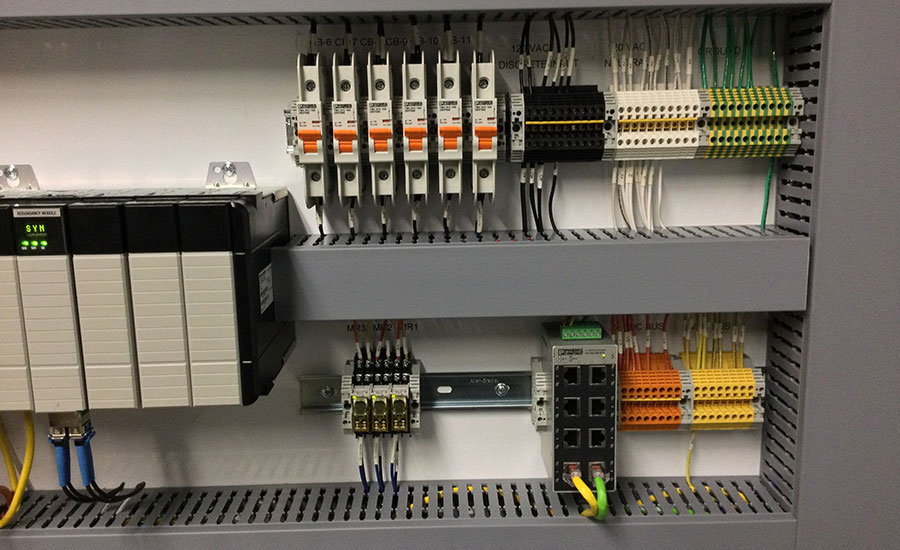


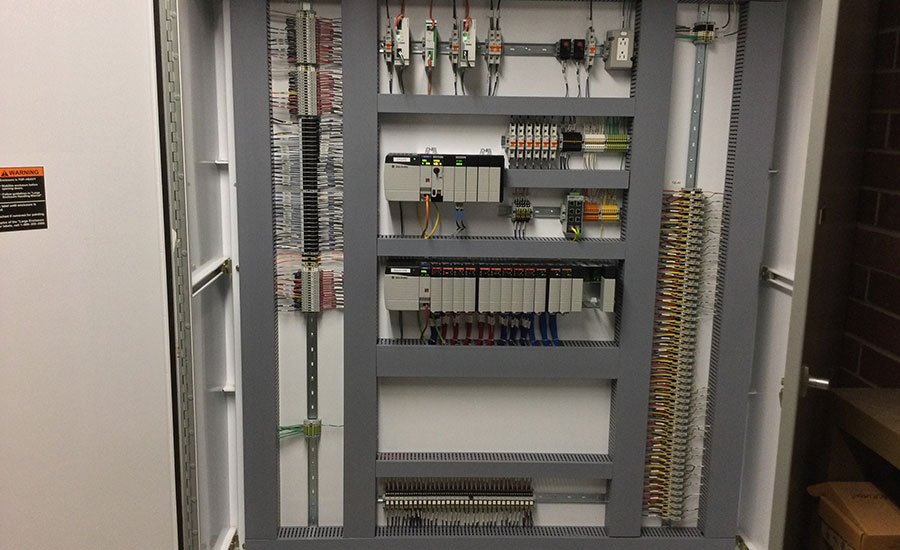


Photos courtesy of Harris.
With creativity, cost savings and customer satisfaction as benchmarks, using prefabrication in building automation is a must for leading national mechanical contractor, Harris. In fact, the company now has a dedicated Salt Lake City Building Automation Panel Shop, which is UL508A certified, where its innovative prefab is a company mainstay. Allowing work traditionally completed on-site to be done off-site, the team has saved thousands of hours in the field and improved the overall effectiveness of building automation projects across the country on a daily basis for Harris.
Case in point. Working on the new 360-acre Utah State Correctional Facility, the SLC team provided and installed HVAC Controls for the complex’s 31 buildings. Using engineered, designed submittals and field input, the Building Automation shop programmed 220-plus PLC and DDC panels months in advance.
Meeting rigid quality standards and an accelerated schedule, the prefabrication will save nearly 4,000 project hours. The work has set a new standard for Harris panel fabrication, enabling better quality control, national standardization and more efficient and skilled field personnel.
“The ability to be across the country and, for example, have one color mean the same thing to everyone – regardless of the project – equates to less time in the field troubleshooting, standardization in service, safety mitigation and more,” says Steven Clark, procurement fabrication lead, Harris. “Even with shipping and receiving of parts, having that buying power with larger quantities, we can pass that savings on to our customers.”
Harris’ Jarvis Hofhines, general manager, Service + Building Automation, adds that having a minimum standard quality that you build to, while doing so as cost effectively as possible, is important. And, engineering panels that are robust for field applications will produce long-term gains for customers. Similarly, service friendly solutions create reliability.
Clark notes that the panel shop likely doesn’t have more than two panels that they’ve built that have been totally alike. Even with air handlers, there are relays that change and different actuators. “We may have a standard layout, but every panel we do is custom to the job, whether it’s terminals and power supplies in a certain spot, or terminals in a certain way,” he says. “There’s less time in the field, which also means less chance of someone getting hurt.”
But don’t forget, not all control panels need to be new. “There’s a huge opportunity and tremendous value for customers in retrofitting control panels,” says Hofhines. “Unfortunately, it’s not uncommon to open a cabinet and find a wiring nightmare.” But that doesn’t have to mean gloom and doom. “We’ve made it possible to look at an existing system and custom tailor a panel solution that takes advantage of existing field wiring,” he says. It is feasible to make sense of it all, to get it organized, and even get an as-built drawing so servicing the system becomes manageable.
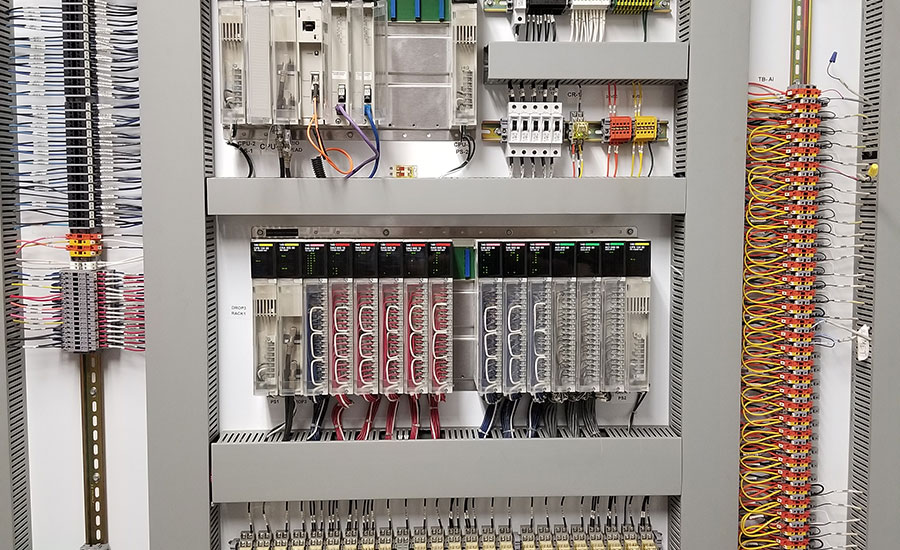


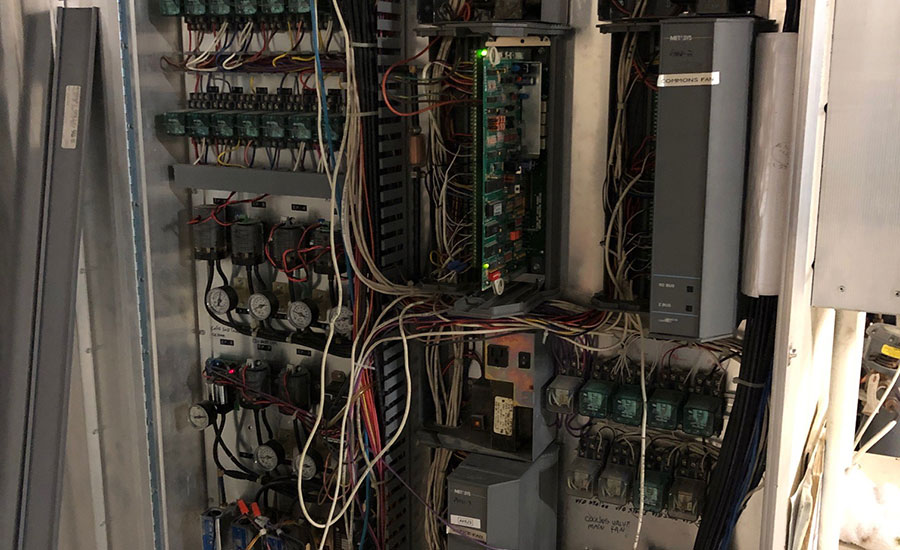


Photos courtesy of Harris.
It’s no surprise that large facilities require sophisticated controls in order to sustain comfortable temperatures and humidity levels, while also remaining efficient and reliable. Industrial, commercial and sizable buildings, such as schools and hospitals, often have dedicated direct digital control (DDC) systems to provide more precise control over HVAC and other operations. This allows different temperature zones to be set, as well as scheduled and automated system operations and performance monitoring.
While a DDC systems’ primary purpose is building automation and systems integration, they also allow for greater flexibility by exposing unique conditions, errors and system-wide visibility. But the panels need to be designed correctly, otherwise they’re difficult to troubleshoot and can experience accelerated failure rates.
John Wanner, Salt Lake City School District HVAC Controls, helps oversee the district’s building automation systems and networks and has been working with Harris to upgrade control panels at more than 10 district schools so far. By retrofitting the panels – reusing existing control cabinets and frameworks – the cost is minimized for the building owner.
Harris has been constructing panels for the district that run air handlers, as well as central plants – which includes taking over chilled water systems, boilers and heating water systems. The Harris team is led by Hofhines and includes a skilled field team working under the technical direction of Drew Lewis.
“Harris has turned our DDC panels into an organized system that’s easy to troubleshoot and diagnose,” says Wanner. “We get a nice wiring diagram that matches everything, making it a lot easier to diagnose complicated systems.” Wanner says Harris has been able to update certain panels while school is in session and systems are running.
“They’re able to take old panels out and put new ones in during daytime working hours, without disruption. That’s been wonderful,” Wanner continues. “On days when we’re swapping out a more complicated system, and do need to shut down, we’ve been able to schedule that work with Harris at times when students and staff are not in the building due to COVID-19 hybrid models.
“Working with Harris, I’ve had fewer wiring issues with these panels than I have had with others,” states Wanner. “Quality, knowledge and dependability are really important.”