
These questions have been on the minds of many commercial contractors, but particularly those who work on systems for the health care industry. Fred Willson of Entek, Longview, Wash., has been studying the problem lately for a variety of reasons. He most recently was looking at protection for his own employees if they provided HVAC maintenance at an AIDS hospice, but the contractor has been actively looking at ways to protect employees in all settings.
"We're very jealous and watchful of our field help," Willson said. "We're also trying to convince a second-generation of workers that this is a great place to work. You've got people out there who are rightfully concerned about their work environment."
There are two main routes of disease transmission: airborne and blood borne. Airborne transmission means a person has to inhale something in order to be infected. This can include inhaling respirable droplets, such as those released when a person sneezes. Diseases that are airborne tend to be much hardier than blood borne infections, which do not survive for long outside of the human body.
"We're working in tons of clinics and hospitals," Willson said. He wants to make sure his employees are protected.
According to company engineer Matt Todd, "Dental offices are pretty bad too." Human blood and tissue are released during most procedures. "That material they use to grind your teeth, and the composites," he continued; "it makes filters look like a nice enamel smile."
AIDS AND HIV
Working in the AIDS hospice, at least, this becomes a nonissue for contractors like Entek. The fragility of the virus makes it unable to survive in an airborne environment; its transmission is only direct through blood and a few types of bodily fluid.Protecting hospice residents becomes more of an issue, because their immune systems are compromised. Todd said they installed a Mitsubishi City Multi system, with ventilation levels mandated by the American Society of Heating, Refrigerating, and Air-Conditioning Engineers (ASHRAE) achieved with a Greenheck energy recovery ventilator (ERV). There are 35 zones; 15 patient rooms, a full kitchen, administrative offices, and a total of roughly 7,000 square feet.
"The residents basically move into their rooms," said Todd. "As long as they're able, they wash their own linens and clothes. We're going into their homes when we work on the systems.
"There is an isolated area for residents who smoke that has radiant heat," he continued. "AIDS patients are very prone to being cold all the time." The room's air is ventilated separately from the rest of the hospice. "The ERV is providing a great deal of continuous ventilation for the facility. It runs 24/7. They had nothing in there before; it was an all-steam pipe system with radiators."
Now the contractor is waiting on approval of a maintenance contract. "Every two months, we will go in and clean the washable filters," Todd said. "We are going to buy a separate, complete set of filters and swap them out with the filters in the units. Then we'll bag the ones that came out of the units, take them back, and run them through an industrial dishwasher." The contract also includes a twice-yearly chemical clean. "We've also proposed using a biocide treatment to help clean drain lines," he said.
"It's a two-headed coin," said Willson. "We want to keep the hospice folks comfortable, and for our guys too, we want to keep it as clean as possible."
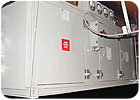
HIV DENTAL CLINIC
Meanwhile on the other coast, an engineer has been dealing with the dual challenges of HIV patients in a dental clinic.The Albany (N.Y.) Medical Center (AMC) HIV Dental Clinic is paying extra attention to air filtration and air changes, to protect HIV patients from developing active tuberculosis (TB) and other airborne infectious diseases while they are getting dental work performed.
According to the Center for Disease Control (CDC), one-third of all AIDS victims worldwide die from TB complications; this played a big part in the design of systems at AMC. The center's HIV services include medical, dental, social, nutritional, psychological, educational, and clinical research.
The center's Engineering and Construction Department based the dental center's HVAC design on recommendations from the CDC's "Guidelines for Preventing the Transmission of Mycobacterium Tuberculosis in Health-Care Settings, 2005," as well as ASHRAE standards.
The two most critical compliances were air changes/hour and filter media recommendations from the CDC, according to John Davidson, manager of facilities engineering, AMC. "The attention we paid to air filtration, particularly the control of infectious airborne diseases such as TB, goes well beyond what you'd see in a conventional medical outpatient setting," he said.
Conventional rooms typically require six air changes/hour; however, 12 air changes/hour were designed for the 1,250-square-foot HIV dental area, which comprises rooms for waiting, offices, instrument sterilization, and three dental operatories.
Filtering is provided by a BioCircul-Aire® air purification air handler package unit from the Circul-Aire Inc. division of Dectron Internationale Inc. Circul-Aire custom designed the 2,100-cfm system to Davidson's specs, a combination of an ASHRAE-rated 30-percent filter, 90-percent filter, and 99.97-percent HEPA filter, the latter of which is specifically outlined in CDC's TB containment guidelines.
PROJECT CHALLENGES
The retrofitted space design, which included piping, sheet metal, and equipment installation services by project mechanical contractor Alltek Energy Systems Inc., Waterford, N.Y., was challenging from the aspect that AMC leases rather than owns the building. Consequently, the existing Lennox 5-ton conventional rooftop system supply air had to be modified instead of replaced with a system more suitable for this application.Davidson isolated the space by providing an independent air supply from a dedicated rooftop unit that was routed through the filtration system and recirculated/exhausted independently of other spaces outside the dental area.
Alltek rigged the air purification unit through tight doorways and fabricated a hanging support system for it in an enclosed ceiling space. Running ductwork and piping in a confined environment was equally challenging, according to Alltek sales engineer David Legge.
F.R. Foote, a Clifton Park, N.Y.-based manufacturer's representative, confirmed that the unit would fit. Alltek also fabricated all the sheet metal, and installed Metalaire diffusers and Greenheck exhaust fans to balance the space to the specified negative pressure.
Bill Mattfeld, sales engineer, F.R. Foote, helped coordinate motor horsepower and sized the equipment.
Davidson also specified pressure-differential gauges for all three filters to determine filter replacement. Both the rooftop and filter system were outfitted with flow alarms by Kot Electric that activate when airflow falls below specifications.
Publication date: 11/06/2006