Steam heating has been around a long time. It’s a tried-and-true way to heat a number of different applications because it’s such a wonderful medium for heat transfer. In addition, it is usually easy and relatively inexpensive to move steam heat from a boiler to an occupied space, typically via unit heaters or air-handling units.
However, steam is not without issues.
One of the main problems is that steam condenses when giving up its heat; that condensation can accumulate, causing the coil to freeze. Every year, companies everywhere experience frozen coils. This translates into discomfort for building occupants, who then shiver and complain. In addition, it’s often costly to repair or replace the coils.
Most coil freeze-ups occur in the northern tier of the United States, where temperatures can drop into the subfreezing range and stay there for days or weeks. However, warmer parts of the country can have problems as well, especially if a surprise cold snap hits.
Freeze-ups generally occur more often with aging systems, although newer systems that have not been properly installed or maintained can suffer as well. As in most hvac installations, proper installation and maintenance are key to trouble-free performance.
Why It Happens
A freeze-up can occur when condensate freezes within a coil. For this reason, it is important that condensate be completely removed as quickly as it forms. There are generally two reasons why condensate may remain in the coil long enough to freeze:1. Standing condensate near the steam trap freezes (because of an improperly sized or installed steam trap, or the trap has malfunctioned), creating an ice plug. This allows additional condensate to back up further into the coil.
2. If the steam supply is shut off, it’s possible that a slight vacuum forms within the coil, preventing free drainage of condensate. This creates a pocket of condensate that can quickly freeze and create a blockage. A vacuum breaker can help solve this problem.
If either of these scenarios happens, look out. Besides losing the energy transfer that heats the airflow across the coil, costly maintenance problems may occur. The forces of frozen condensate can rupture the coil’s pipes and, perhaps, the steam trap itself. Should the coil rupture, that section of pipe will need to be repaired or cut out and replaced. Otherwise, when the system warms above freezing, valuable steam will escape through the opening.
Depending on the trap type, it too can be damaged by freezing. That’s why it’s extremely important to trap a steam system — and do it properly.
The Need To Trap
The function of a steam trap is to remove condensate and noncondensible gases as soon as they form. Because the purpose of steam heating coils is to transfer energy from the steam to the air, condensate will form quickly in the coil. Due to gravity, this condensate collects in the lowest part of the coil. These low points or pockets are where steam traps should be installed.Without a method of removing condensate, the coil can become flooded. If it’s cold enough, it can freeze.
“Because a properly installed steam trap is essential for removing condensate, and because traps vary from manufacturer to manufacturer, follow the trap manufacturer’s installation recommendation,” advises Scott French, P.E., manager of application engineering, Armstrong International, Inc., Three Rivers, MI. “Also, the universal rule is that each individual heat transfer unit must have its own properly sized steam trap.”
French notes that some rules of thumb apply to trapping. The first rule of trap installation is proper selection of a steam trap. This includes specifying the proper trap size.
“Beyond selection, it’s essential to pipe the low point of the heat transfer equipment to the trap and be sure to follow the installation directions,” notes French. “Do not confuse the inlet and outlet sides of the trap during installation.”
It’s preferable to install the trap so that the discharge will flow into a return system below the trap. If the return line is above the heat exchanger, make sure there is sufficient pressure to elevate the condensate; if there isn’t, a pumping trap may be required. When piping to an overhead return system, make sure there is adequate insulation covering the riser, which could be as high as 15 ft or more.
Most steam coils have modulated control. Therefore, even if there is enough steam pressure in the supply line, the pressure may be modulated to the point where there is not enough pressure in the coil to make the required lift.
“As a general rule, a pressure of 1 psi is required for every 2 feet the condensate is elevated. Therefore, 7.5 psi would be needed to lift the condensate 15 feet to the return line. With only 5-psig steam at the coil inlet, condensate obviously backs up. It’s a freeze-up waiting to happen, so use a pumping trap or a safety drain,” says French.
As noted earlier, it’s important that each individual piece of heat transfer equipment has its own steam trap. Installers often reason that because the coils are fed by the same steam supply and are doing the same general duty, condensing rates and pressure drops across the coils are the same. However, small differences in construction, airflow rate, air temperature, and dirt build-up lead to differing pressure drops. Even differences too small to register on a gauge can be enough to prevent proper drainage that may result in a frozen coil.

What Else Is Required
Steam traps are just one component that helps reduce the risk of freezing. Vacuum breakers, thermostatic air vents, and possibly pumping traps may be required for efficient heat transfer with a reduced possibility of freezing.In addition to steam traps and other components, proper maintenance must take place to ward off freezing. For peak coil performance, it’s advisable to periodically clean the finned coils of dirt accumulation and to protect the fins from becoming mashed or broken.
“As you are cleaning the coils, inspect the support brackets to ensure that the coils are in proper alignment and none of the mounting brackets have broken or become loose,” says French. “However, the most important preventive maintenance procedure is to regularly inspect and test the steam traps to ensure they are operating properly.”
It is highly recommended that the traps be tested during system start-up and at least several times throughout the season. Pay close attention to the traps during the coldest part of the season, and repair or replace failing or failed traps immediately.
By paying attention to details during installation and providing proper maintenance after installation, there’s a much better chance that a building owner will not suffer the expense and irritation caused by coil freeze-ups.

Sidebar: Coil Design Can Help or Hinder Freeze-Ups
Besides installing steam traps and devising a thorough maintenance program, coil design is another factor that can influence freeze-ups.There are four or five basic coil designs and they are usually identified by the steam circuitry within each coil. They include the standard coil (“We do not recommend these for freeze-prone applications,” notes Scott French, P.E., Armstrong International Inc.), the centifeed, and two designs of the tandem coil. Either the centifeed or the tandem designs are usually specified in cold climates.
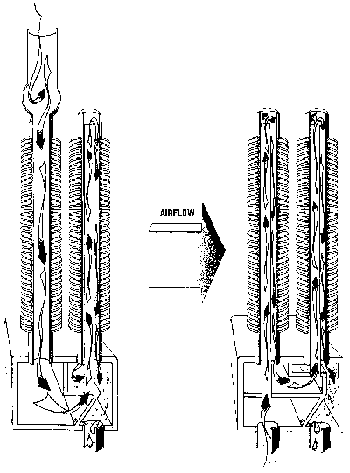
The standard coil design is used in most applications where entering air temperatures are above 35?F and steam is at a constant pressure. Basically, rows of finned tubes are connected to a header that feeds each tube with steam. This type of coil is not recommended where even outlet air temperatures are required immediately after the coil, such as in multizone heating systems, or where a modulating steam control valve is used to control temperature. “This standard coil is ruled out when considering coils for applications in very cold climates, where freezing is likely,” says French.
A centifeed coil essentially is a plain tube (called the inner steam distribution tube) inserted within an outer fin-mounted tube. Steam enters the center tube and exits into the outer tube. As air passes over the fins, the condensate discharges to a receiver. French notes, “The single-row centifeed coil can be used where air is below freezing and/or modulating control is used. The inner tube acts as a steam tracer to keep the finned tube warm.”
Another type of coil design is known as the tandem design, and there are two types of circuitry, one with opposite-end connections and the other with same-end connection. The tandem coil is recommended in freezing applications requiring more than one row to achieve the desired final temperature.
The total amount of steam to be condensed by the entire coil is fed into the first row in the direction of airflow. This purges noncondensible gasses and droplets of condensate from that part of the coil exposed to the coldest inlet air. Channeling the steam from the header to the other rows in series has the same purging effect. This design ensures that air passing over the last row is at least 35? and above the freezing point.
“The coldest part of the tandem coil will always have steam in sufficient quantity to overcome unequal distribution and back feeding due to different steam loads and pressure drops in adjacent tubes. This eliminates freezing problems caused by condensate holdup,” says French.