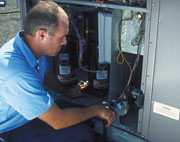

This article details a few commonly overlooked aspects of rooftop unit heating maintenance.
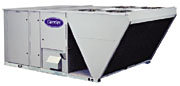
ELECTRICITY, SAFETY
In general, the electrical components are often overlooked, said Craig Walker, Senior Service Training Instructor for the Carrier Corporation's Customer Technical Training Group. He has been involved with training the company's distributor, dealer, and contractor customers since 1987."Technicians often center in on cleaning coils or inspecting belts and pulleys," Walker said.
Note: Before servicing rooftop units, techs need to take care to shut off all electrical power to the unit. Tag the disconnect to keep anyone else from turning it back on; this will help avoid shocks or injuries from rotating parts.
However, when it's time to check the electrical circuits, the power needs to be turned back on, said Walker. The following service and maintenance, therefore, requires extra caution on the part of the technician.
- Walker first recommends inspection of electrical connections - wiring, connections, contactors, relays, and circuit breakers. Check for signs of overheating or wear; replace as necessary. If wear seems to indicate deterioration other than normal aging, the tech may need to examine the system further.
- Check current and voltage in close proximity to the terminals, using reliable instruments.
- Check for voltage and current imbalance on three-phase loads. "On three-phase loads, the compressor and fan motor contactors could have two to three contacts," Walker explained. If those contacts are overheated and worn, this could result in increased resistance and could lead to voltage and current imbalance. (Maximum is 2% voltage imbalance and 10% current imbalance).
Walker also offered the following safety pointers for technicians working near live electricity:
- "Don't wear metal." Any type of metallic jewelry could be a conductor.
- Wear rubber-soled shoes. "Watch out for industrial-type shoes with metal toe guards," he advised.
- "When your hands are in the control box, the chance of electrocution increases," said Walker. Therefore, techs need to know the proper use of a voltmeter. "Emphasize that they put one of the probes on the load side of potential stationary with an alligator clip," said Walker. "That way they only have one hand in the electrical control box while troubleshooting electrical circuitry.
"We all tend to get careless and in a hurry sometimes," he continued. "If you're cautious, it's not a problem having both hands in the control box." But in general, it's better to be safe than sorry.
WINTER SPECIFICS
Even if it's still too warm to require the heating to be on, a good prewinter rooftop unit checkup means that "You verify that heating is going to be operational," said Walker. The fall checkup needs to include checking the controls and heating system operation.Some basic inspections are also in order.
Flue gas passageways: Inspect the flue collector box and heat exchanger annually. Clean all surfaces as needed using a wire brush. Depending on how long it's been since the system was last serviced, techs may find dirt (from the unit's outdoor location), rust (a result of water vapor condensing), and soot (from incomplete combustion).
Combustion air blower: Clean the combustion air blower to ensure proper airflow and heating efficiency. The blower wheel should be inspected every fall, and periodically throughout the heating season. This can be part of a customer's maintenance contract. Inspect the blower wheel by shining a flashlight into the draft hood opening, he said.
Temperature limit switch: Test the temperature limit switch and verify operation of the limit by temporarily blocking the return air until the limit trips.
Block it with plastic or cardboard on smaller units, said Walker. "This will reduce airflow over the heat exchanger, causing the temperature to increase."
It's important to monitor temperature as close to the limit switch as possible, he stressed. Did it overshoot? Take longer than necessary? "Look at possible replacement of the switch," said Walker. Take this measurement with a thermometer or thermocouple-type device. Techs may need to locate a remote measuring device in the unit. Also with return and supply air unrestricted, check for correct temperature rise (the difference between return and supply air temperature). Temperature rise should be measured and compared to the manufacturer's nameplate specifications.
Main burners: Inspect the main burners for deterioration or blockage from corrosion or other causes. The main burner flames should be observed and adjusted, if necessary.
Soot that techs may see would come from incomplete combustion, said Walker. Depending on the age of the product, corrosion could result from water vapor, a byproduct of complete combustion. "Many manufacturers now use a coating to inhibit corrosion," he said.
If evidence of incomplete combustion is observed anywhere within this inspection, the technician needs to observe the unit's sequence of combustion and troubleshoot accordingly. Incomplete combustion may pose a risk of CO poisoning to the building's occupants.
FREQUENCY
In general, the system's lifespan hinges on how often it is maintained, said Walker. It also varies according to the climate in which it's installed, which in turn affects how often the system runs. The environment (pollution, etc.) in which it's installed is also key.All too often, rooftop units are out of sight, out of mind - "especially the smaller units, 10 tons and under," said Walker. For larger applications with many units, the property owner is often more sophisticated when it comes to maintaining the property. How-ever, for cases like constant-volume, small store applications, the landlord or tenant may not think about servicing the rooftop unit until it breaks down.
This could present the best opportunity for contractors to offer regular service through a maintenance contract.
For more information, visit www.training.carrier.com (website).
SIDEBAR: Winter, Spring, Summer, or Fall
During the winter or summer preseason inspection, regular service and maintenance for rooftop units should include:- Inspecting and cleaning the evaporator and condenser coils (this can be performed more often, depending on the application);
- Cleaning or replacing all filters as needed;
- Cleaning and/or inspecting inlet screens;
- Checking the compressor's oil charge;
- Lubricating the fan motor bearings (if not permanently lubricated);
- Checking the condenser fan height;
- Inspecting the evaporator fan to ensure that it's centered in the housing;
- Inspecting the blower belt for wear, proper tension, and pulley alignment;
- For units with TXVs, checking each circuit to ensure that the bulb is secure, insulated, and in the correct position;
- If the unit has an economizer, performing a cycle run-through;
- Checking the refrigerant charge; and
- Checking for loose and overheated electrical connections.