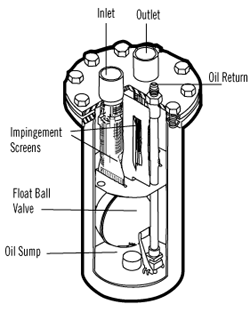

New refrigerants mean that many systems will be reexamined, redesigned, or replaced. This provides an opportunity to change components that critically affect overall system efficiency but are often overlooked.
Some of these components have new features to match the refrigerant improvements. The oil separator is a case in point.

HIGH DAMAGE POTENTIAL
Yes, oil is essential to refrigeration. But oil must be confined to where it is needed. Since oil and refrigerant gas are miscible — or mutually attractive — the gas can carry oil throughout the system, with devastating results.To be more specific, oil’s sole purpose in a refrigeration system is to lubricate the compressor. Inadequate lubrication will eventually cause a compressor to seize up or burn out. Oil will, however, harm other system components and so must be confined to the compressor.
Unavoidably, all compressors pump oil into their systems, the amount being determined by several factors:
In most systems, the pumping rate of oil to refrigerant can average from 3% to 15% of the total mass, with some systems having 25% to 75% of the mass flow as oil.
Oil and refrigerant in the condenser and liquid receiver will more readily mix in the high temperature phase of the refrigeration cycle. Lower temperatures in the evaporator cause the oil and refrigerant to mix less readily, forcing the oil to precipitate and accumulate in the evaporator, thereby robbing the compressor of its vital lubrication.
From the condenser to the metering device, refrigerant oils are soluble with liquid refrigerant. But, oil and refrigerant vapor do not mix readily. So, from the evaporator to the compressor suction inlet, oil and refrigerant are not very mixable. Oil can be circulated through the system only if gas velocities are kept high enough to carry the oil along the piping and heat exchanger tubes. The ability to retrieve or flush the oil from the evaporator or other locations depends on:
A refrigeration system should have velocities high enough to carry the oil through the system and back to the compressor. These high velocities provide good oil return, but also cause pressure drop. This pushes the system to work harder to produce a given amount of refrigeration effect, requiring more energy or larger equipment — and rising costs. The oil is forced around the system, but the lubricant’s insulating effects reduce heat transfer efficiency.
Excessive oil in the system initiates many problems. Worst case is a system with oil trapped in the evaporator and a higher load demand, with increasing refrigerant velocity. The higher speed may return all the oil to the compressor at once, causing an oil liquid slug and ruining the compressor.
It was once believed that oil helped refrigerant make better contact and adhere longer to the wall of heat exchangers (condensers and evaporators), thus improving heat transfer. Actually, a thin film of oil carried by the refrigerant coats the inside of the system, acts as an insulator, and isolates the refrigerant from direct contact with the heat exchanger, retarding heat transfer efficiency.
In the condenser, temperatures are higher, so the oil film will be thinner. However, it can still measurably increase head pressure and temperature. Colder temperatures in the evaporator will thicken the film to the point where the oil is too viscous to flow. Lower heat coefficients in the evaporator lower evaporating temperature and pressure. What happens in the condenser and evaporator directly affects compressor capacity and efficiency.
To make up for the heat transfer losses, a system must have larger condensers, evaporators, compressors, and other components. Systems not compensating for the loss of efficiency will have longer compressor run times, different pressure control settings, and more required defrost periods, all wasting energy.
To sum up, oil’s undoubted benefit to the refrigeration system is in constant danger of being offset by its potential for causing serious problems — problems which can cause down time for the refrigerating system, higher operating costs, and, ultimately, spoilage of stored goods.
COMBATING THE OIL PROBLEM
The oil separator is a device specifically designed to remove oil from where it can harm the refrigerating system and to return it to the compressor, where it is needed. Although there are several types of separators, let’s focus on the two that seem likely to dominate the field in the near future.Conventional “impingement” separators (Figure 1) are most commonly used today.
These units rely on centrifugal force and the expansion of gasses to remove oil. Superheated and oil-laden refrigerant gas enters the separator shell, where the oil passes through an inlet screen and is separated from the gas by adhering to the screen. Gravity pulls the oil to the separator’s sump, from which a float valve meters it back into the compressor.
A drawback to this type of unit is its reliance on centrifugal force to accomplish separation. Centrifugal force only works effectively on relatively large oil droplets. This means that smaller droplets remain in the gas and are recirculated through the system.
It’s likely that, under actual operating conditions, conventional separators will function in the 80% to 85% range.
The second type of separator, the coalescing unit (Figure 2), operates through a filter of exceptionally pure, extremely fine glass fibers, which form a capturing matrix. This matrix excites the oil molecules, causing them to collide with each other and form larger droplets, which are forced to the filter’s outer drain layer. Gravity then pulls the droplets into the sump.
These units achieve their efficiency by capturing the small oil droplets and a large percentage of atomized oil vapor.
Coalescing units are capable of delivering between 95% to 99%-plus efficiency, depending on the grade of filter core used and the attention paid to design details.
Coalescent units cause less pressure drop than conventional separators. They are designed to maintain efficiency over a system’s entire load range rather than becoming less efficient with lower loads.
CLEANING WITH COALESCENTS
The new refrigerants have made system cleaning even more important than when CFCs were the mainstay refrigerants. The replacement refrigerants (HFCs) and oils (POEs) are even better solvents than their predecessors.So, it is significant that coalescing units capture solid contaminants to 0.3 microns, cleaning the system and preventing it from fouling metering devices. Equipped with accessible filters, coalescent units work well during system start-up. And, they are effective during burnout, capturing the vast majority of resulting carbonized oil, winding lacquer, and metal shavings.
On average, a properly designed and sized coalescing oil separator has five times the filter area of the standard liquid line filter-drier and five times the filtering area of the suction filter that would be used on a system of the same capacity.
Arbiture is with Temprite, 1555 Hawthorne Lane, West Chicago, IL 60185; 630-293-9594 (fax).
Publication date: 12/04/2000