How do you choose the best oil cooler for your customer’s application? Become acquainted with the design, components, and benefits of various systems on the market.
Wayne Wehber, P.E., director of Market and Product Development for Vilter Manufacturing Co., Cudahy, Wis., took attendees of the Refrigerating Engineers and Technicians Association (RETA) conference here through system characteristics that need to be considered when choosing an oil cooler.
Wehber said there are two basic types of oil coolers: indirect and direct cooling.
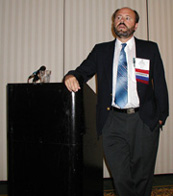
Indirect Cooling
In indirect cooling, the oil is cooled through the heat transfer of an intermediate medium, Wehber explained.“This is an outside system with an external heat exchanger, which uses water, liquid [such as glycol] or refrigerant, or thermosyphoning to cool.” Shell-and-tube and plate-type heat exchangers would both use indirect coolers.
In water-cooled external heat exchangers, oil flows out of the separator. Either a pump or differential pressure forces oil through the heat exchanger. The oil temperature usually is controlled by the thermostatic valve controlling bypass of the heat exchanger.
Wehber said that water-cooled cooling system components include:
The heat exchanger cools the oil before it is injected into the compressor.
External systems that operate via thermosyphoning include shell-and-tube heat exchangers, plate-type (brazed, welded, or bolted plate-and-frame) heat exchangers, and shell-and-plate heat exchangers. In this system design, oil flows out of the separator and is forced through the heat exchanger via pumping or differential pressure forces. Oil temperature is controlled by a thermostatic valve controlling bypass of the heat exchanger.
Thermosyphon cooling system components include:
The benefits of indirect cooling systems include the fact that they require little maintenance, and they are simple in design and operation. The disadvantages are that they may carry a higher system cost and a higher initial cost of cooling.

Direct Cooling
The direct cooling method allows the refrigerant to be in direct contact with the oil/refrigerant mixture, Wehber explained. There are several direct oil-cooling designs.In the booster application, liquid refrigerant enters the discharge line of the compressor from a higher pressure source. In this system design, a nozzle sprays liquid refrigerant mist directly into the compressor discharge. The liquid refrigerant then mixes with oil and the compressed refrigerant.
“The refrigerant flashes or evaporates, thus cooling the oil,” Wehber explained. A temperature sensor controlling the thermal expansion (TX) valve maintains discharge temperatures.
Components of the booster method system include:
For liquid injection into the discharge line of high-stage applications, liquid refrigerant is injected into the compressor’s discharge line. “It can be used when there is inadequate liquid feed pressure to high-stage applications,” Wehber said. A pump injects liquid refrigerant at a higher pressure.
He explained that “A discharge temperature sensor signals the controller to the variable-speed pump, which speeds up or slows down to control the process. Liquid refrigerant is injected directly into the compressor discharge through a nozzle, mixing with oil and compressed refrigerant.” When the refrigerant flashes, the oil is cooled.
Components of this system (also called the V-Plus) include:
Direct liquid injection into the compressor provides cooling during the compression process, Wehber explained.
In this type of system, he continued, a discharge temperature sensor signals the TX valve controlling liquid injection into the compressor. Liquid refrigerant evaporates during the compression cycle. The refrigerant gas/oil mixture is discharged from the compressor when it reaches the desired temperature.
The compressors for this type of liquid injection system may have low and high port locations to inject liquid refrigerant. “Injection of liquid at the port of highest possible pressure minimizes recompression,” advised Wehber.
Its components include:
Cool compression is a new oil-cooling design, Wehber said. “It was started as a liquid ammonia flooded screw oil cooling system.” That test ran for a year, and the manufacturer recognized the benefit of having some oil in the mixture injected into a single screw compressor: It helps viscosity.
The company also recognized the properties of liquid ammonia droplets for separation: No coalescing element is needed.
“It starts like a standard oil-flooded unit,” Wehber said, “with oil sitting in a separator” and no oil pump. Cooling is initiated by a supply of liquid ammonia, the level of which is formed on top of the oil in the separator. “The ammonia forms a couple of inches deep on the oil,” Wehber said. “The oil isn’t aware of what is going on.”
The oil-rich mixture is injected in the bearings and seal chamber. The oil and liquid ammonia are injected into the groove of the screw during the compression process.
In the cool compression design, liquid ammonia droplets capture oil droplets inside the separator. The blanket of liquid ammonia on the oil completes the cooling process and keeps the oil from foaming.
Its components include:
To monitor the liquid ammonia supply in the cool compression system, saturation temperature is calculated from the discharge pressure and compared with actual discharge temperatures to calculate superheat. When superheat is greater than 25 degrees F, the unit unloads. When superheat is greater than 35 degrees, the unit shuts down.
In this design, the oil and liquid ammonia mixture reduces viscous drag of rotating components, Wehber said. When the mixture is injected at saturation temperature, it minimizes flashing of the ammonia and recompresses.
It also minimizes preheating of gas entering the screw with cool oil/liquid injection temperatures. Ultimately this allows more capacity through the compressor, Wehber pointed out.
The benefits of cool compression are low initial cost, simple design, less maintenance required, and more stable temperature control.
“Liquid ammonia does some neat, wild stuff once it gets in contact with the oil,” Wehber pointed out.
By knowing the types of system limitations and benefits beforehand, refrigeration contractors can make better informed decisions about oil cooling systems to meet their customers’ needs.
Publication date: 01/13/2003