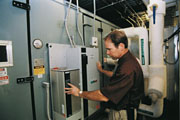
Most motors operate at a nearly constant speed; however, much of the time the devices they drive may operate at less than the maximum design speed. A vfd controls the amount of electricity going to the motor, so energy is saved by matching the motor speed to the load.
In the hvac industry, vfd’s are usually found on motors that drive fans, blowers, pumps, cooling towers, etc. The Department of Energy reports that 64% of all electrical energy in the U.S. is consumed by electric motors. And you can bet that many of those electric motors are used in hvac applications.
According to some studies, the addition of vfd’s to an existing system can result in a reduction in energy consumption of 30% to 60%. For this reason, vfd’s are becoming quite popular. Since the technology has become much more stable over the last few years and costs are coming down, it’s a good time to look at vfd’s.

ENERGY SAVINGS
As noted, the most obvious benefit to using vfd’s is energy savings. With a centrifugal fan or centrifugal pump, energy savings of 60% or more are common compared to full-flow operation. According to Bill Mudge, vice president — Sales and Marketing, Danfoss Graham (Milwaukee, WI), vfd’s should be considered for every centrifugal fan and centrifugal pump in the hvac system.This includes supply and return fans and primary and secondary chilled-water pumps. Cooling tower fans, condenser water pumps, ventilation fans, makeup air fans, and domestic water booster pumps are also candidates for vfd’s.
“Any fan or pump that during the course of the year has excess capacity is a candidate for a vfd,” says Mudge. “Virtually every hvac fan or pump has excess capacity almost all of the time, as it was sized for full occupancy on the hottest day of the year.”
The vfd will also automatically compensate for any oversizing of system components by automatically reducing system capacity to that required by the load. Any time the motor driving the fan or pump can be slowed down, increased savings and control can be achieved.
Other means of flow control (such as inlet guides and variable-pitch vaneaxial fans in air systems, and throttling valves and bypass loops in water systems) can be used, but the energy savings will be reduced, says Mudge. “Vfd manufacturers can provide computer-based payback calculations comparing vfd’s to other systems.”
The continued decline in the price of vfd’s, coupled with the continued increase in the cost of electrical energy, make the paybacks shorter than they were just a few years ago, Mudge continues. It is now feasible from a payback perspective to equip almost every three-phase fan or pump with a vfd. Of course, the payback will be quicker on larger motors because the cost per hp decreases with size. However, one of the most popular sizes available is 15 hp, with 10 hp following right behind.
Many older buildings could be made much more efficient, and therefore much more attractive to a tenant or owner, with an hvac retrofit that includes vfd’s.
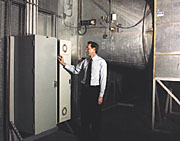
OTHER BENEFITS
A less obvious — but also important — benefit is that the vfd will allow lower maintenance costs and longer life for the driven equipment. The driven equipment will not experience the shock of line starting, will not be short-cycled, and will not run at a speed higher than that required to meet the comfort needs of the people in the conditioned space, says Mudge.Another important benefit is that of occupant comfort. “The vfd-controlled system never produces pressures or flow in excess of those required for comfort, reducing noise, drafts, and changes in noise and airflow associated with systems that cycle,” says Mudge.
It’s a good thing that there are so many benefits to vfd’s, because ASHRAE Standard 90.1 will effectively require vfd’s on every hvac motor except the smallest ones in commercial buildings of more than 25,000 sq ft.
Something to be aware of, though, when retrofitting older equipment with a vfd is that it may be desirable to retrofit the motor as well. “If the motor is old, it is likely of low efficiency. Also, its insulation may be near the end of its life, and the application of the drive may hasten the motor’s deterioration,” says Mudge.
In addition, if in retrofitting a cooling tower fan a gearbox is used, it may be splash lubricated. If that is the case, the minimum operating speed of the gearbox must be known, as well as the minimum speed of the drive set at or above that point to ensure proper lubrication of the gearbox.
CHOICE AND MAINTENANCE
When choosing a vfd, contractors should follow the specification, says Mudge; this should indicate a vfd designed for hvac applications (a drive designed exclusively for variable-torque loads). Only this type of drive will maximize the savings potential.The drive must be able to communicate with the building automation system to be used. This often requires a proprietary interface, or the more open LonWorks or BACnet communication.
There is no regularly scheduled maintenance for the vfd, says Mudge. Keeping its environment within the manufacturer’s temperature and humidity recommendations and not exceeding the enclosure’s rating for dirt and water protection are the only considerations. The vfd will reduce the need to inspect and replace drive belts, and the slower, more constant rotational speed will increase the life of bearings and sheaves.
If there is any change in the sound of either the vfd or the motor, a problem might be indicated in the power section of the vfd, a bearing or insulation problem in the motor, or a wiring problem between the vfd and motor, says Mudge. Repeated fault trips of the vfd, depending upon the nature of the trip, could indicate a problem in the vfd, motor, power line, or a change in the load.
For most applications, the current vfd technology is excellent. “Future changes in technology will only make the hvac vfd more flexible, more communicative, more reliable, and lower in cost, and yielding a better product with an even shorter payback,” says Mudge.
Publication date: 03/18/2002