The most recent Food Marketing Institute Educational Exposition here stressed a wide range of options for cooling and freezing. All were linked by a commitment to energy conservation, ranging from a basic coil to complex electrical distribution systems.

RACKING IT UP
Hill Phoenix(Conyers, GA) showed a refrigerated display case called the Park Avenue Prestige™. The European-style case uses what the company said is a proprietary secondary coolant system called Coolgenix™. It is supposed to provide a “balanced temperature in the case with no forced air or movement that extends the shelf life of meat up to three times longer than conventional cases.”The company added that “thermal shock, the result of rising product temperature normally associated with defrost in conventional cases, is virtually eliminated.” Moreover, “With no moving parts, fans, or coil systems, cleaning is simply a matter of wiping away residue and moisture from the bottom panel of the display case.”
The company’s PowerWall™, PowerPlus™, and PowerCenter™ electrical distribution units were also on display. They were described as preassembled, custom-made systems adaptable to any size project to help reduce cycle time for new construction or retrofits.
Technology at the booth of Tyler (Niles, MI) included a demonstration of controls from the Canadian company Micro Thermo, which has been purchased by Carrier Electronics. (Carrier Corp. owns Tyler). The idea behind the technology is to create an easier interface and logging between the software and rooftop units and/or racks without added hardware.
On the Tyler racks themselves, Echelon nodes included those for compressor controllers, billed as “smart controllers.” Another product shown was the Carlyle Sentinel™, a compressor protector “able to warn you of deteriorating operating conditions before compressor damage has taken place.”
The exhibit area included Carrier airflow and heat transfer technology in display cases. One example was 3/8-inch tubing as part of a configuration designed “to support the air curtain at the return and make air movement better,” according to one booth official. He noted a 28 degrees F suction temperature vs. a typical 20 to 21 degrees for similar applications. “The higher suction means a higher EER,” he said. “The coils hardly have any frost, so they stay wet all the time. This makes for much quicker defrost.”
Hussmann (Suwannee, GA) displayed its Protocol supermarket refrigeration system, which does away with a large mechanical room and uses compact, multiple compressor refrigeration units closer to the refrigerated cases. This distributed approach is designed to reduce the refrigerant charge, plus installation, construction, and operating costs.
The company featured parallel compressor systems that likewise promoted flexibility and energy efficiency. The company noted it has rack systems for use with R-22, -134a, -404A and -507, as well as options for mechanical subcooling, ambient subcooling, heat reclaim, winter control, loop piping, variable-speed drives, and remote headers.
Last but not least, the company’s Electrical Distribution Centers (EDCs) are said to allow electrical distribution equipment to be preinstalled in a separate housing located outside the store, on ground level, or on a mezzanine inside the store.
Kysor (Conyers, GA) focused on solutions for stores with limited interior space. One option was an outdoor rack unit in an enclosure that could be accessed through a series of doors; these can be removed with a quarter turn of a single bolt on each door.
For inside mechanicals, the company offers a double-stack recip rack, which actually consists of two independent racks on a single frame. The top rack holds medium-temperature compressors with a vertical receiver on one side. The lower rack has low-temp compressors with its receiver to the other side. A single controller regulates both racks and condensers.
Zero Zone (North Prairie, WI) showed its line of display cases as well as custom-made rack systems that had long been manufactured under the Systematic Refrigeration name before that company was acquired by Zero Zone earlier in the year. The racks continue to be made to Systematic specifications in Ramsey, MN.

TECHNOLOGY TWISTS
BRR Technologies(Newport, NC) added a new twist to secondary-loop technology. It offered an additional coil mounted next to the heat reclaim coil. The coil, called the “gizmology,” is a chilled liquid coil. The company said the coil can drop the dewpoint to 34 degrees, which officials said is 12% less than that offered by a direct expansion coil. A reheat to 68 degrees can be done with 25% RH. The ultimate idea, said BRR’s Tom Beckman, is to negate an energy penalty that he said has been cropping up when secondary-loop technology is employed on systems with display cases and walk-ins.The same booth offered a presentation by DTE Energy (Farmington Hills, MI) on the liquid pressure amplification technology introduced a number of years ago by HySave Refrigeration, which is now part of DTE. The technology was shown as part of a pump stand which is now offered by DTE Energy. By getting the system factory mounted on the frame, contractors can avoid some of the problems of improper installation, especially with regards to proper heights, the company said.
XDX Innovative Refrigeration (Arlington Heights, IL) promoted its technology to reduce power usage and the number of defrosts of the evaporative coil. The company’s Xstream component is added to a system downstream from the expansion valve. It creates what the company calls “a turbulent mix of liquid and vapor.” Applications include supermarket display cases and walk-ins. Company officials said it can be used to upgrade existing equipment or as specified by an OEM.
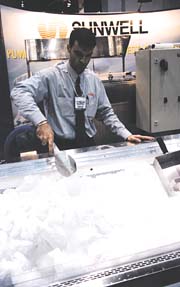
COMPRESSOR TALK
Horizontal compressor technology continues to gain attention.A horizontal rotary compressor and low-profile condensing unit for supermarket applications was introduced by Tecumseh Products Co. (Tecumseh, MI). The company said the compact refrigeration components were developed to meet the needs of store designers and operating personnel.
According to company officials, most self-contained refrigerated display cases today use reciprocating compressors that have more moving parts than rotary compressors. They contend that laboratory and field experience both indicate that the rotary compressor is more reliable than the compressors it replaces, and also offers lower sound and power consumption.
Offering an argument for horizontal scrolls for refrigeration was Hitachi America Ltd. (Dallas, TX), which had representatives showing that the design provides high compression with less leakage for greater efficiency of operation. The technology was said to be able to be used on display cases as small as those on wheels.
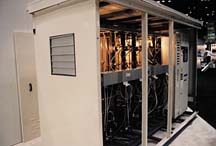
TECHNOLOGY ON ICE
The Canadian companySunwell(Woodbridge, ON) had a different approach to generating ice for display cases in stores: Deepchill™. Ice crystals are produced in an ice generator, then pumped into a sealed, insulated storage and dispensing unit, where they are suspended in water. A controller controls both the ice making and delivery functions.The ice crystals are discharged on demand from the dispenser on top of the unit. The ice then travels through the delivery chute into a positive-displacement pump, where it is mixed with a small amount of water. The ice is then distributed through a flexible hose and eventually out of a specially designed nozzle, into food display cases. Booth officials contended that the result is more sparkling and cleaner ice, since it doesn’t have to be manually transported from a rear room ice machine to the display case.
Howe Corp. (Chicago, IL) showed its Rapid Freeze® ice flaker, which the company said has “a sophisticated design with only one moving part.” The machine produces “100% dry, crisp, subcooled ice that cools faster and more efficiently than any other ice.”
Weber (Kansas City, MO) showed German technology that uses a rotating evaporator for flake ice production. The company said the unit can be hooked up to existing refrigeration systems using R-404A or -22, or to a separate condensing unit.
From time to time, exhibitors draw attention to cooling methods that don’t require mechanical refrigeration. These are usually insulated enclosures for the temporary storage of ice and food. One such example was a display unit from Polar Industries (Ellicott City, MD). There is an ice tray and an adjustable plug.
Another company showed a way to display such foods as fish and meat without having to set them directly on ice. Stark (College Point, NY) suggested that such foods be displayed in stainless steel pans set in a display case that has a gravity coil on top and a refrigeration coil below. A fogger creates and maintains moisture in the case. Officials said product can be kept in the pans and moved to a cooler while the case is hosed out when cleaning is needed.
COMPONENTS AND CONTROLS
New fromKeeprite Refrigeration(Brantford, ON) is a low-velocity unit cooler. The company said the product is designed for applications where low air movement and even temperatures are required throughout the refrigerated space, while maintaining desired humidity conditions.Grasslin Controls (Mahwah, NJ) featured a multivolt defrost timer, said to be applicable to air defrost and in electric or hot gas defrost systems. It is used when the defrost is terminated by the timer or when the coil is frost free, as sensed by a temperature or pressure switch, even if the programmed defrost termination time has not been reached. A fail-safe time termination function terminates the defrost if the temperature or pressure switch fails to do so.
Elreha Controls (St. Petersburg, FL) showed a variety of temperature controllers, including a single-stage model with defrost control. There were also cold storage controllers with either time clock or cyclic timers.
Weiss Instruments (Holtsville, NY) featured what it called “a super low light solar thermometer.” The unit can be mounted in very low light areas, said the company.
Cooper Instruments (Middle-field, CT) showed an infrared thermometer developed for Hazard Analysis and Critical Control Point (HACCP) monitoring with what was said to be a high degree of accuracy between 32 and 150 degrees.
Parker Hannifin Corp. (Cleveland, OH) showed a line of ball valves and quick couples for the supermarket industry as part of the company’s recent acquisition of Aeroquip.
COVERS
Eliason(Kalamazoo, MI) featured night covers designed for energy conservation of refrigerated cases for stores that have closing hours.Econofrost (Shawnigan Lake, BC) featured aluminum night covers for open refrigerated cases.
Sidebar: Emerson Booth Encompasses Range Of Divisions, Services
CHICAGO, IL — Emerson Climate Technologies had a booth at FMI that represented Alco, Clive Samuels, Computer Process Controls (CPC), and Copeland divisions, as well as the Retail Services Group and Design Services Network.“We understand the issues that supermarket operators care about the most, such as saving energy, safeguarding food quality, and reducing equipment maintenance costs,” said Thomas E. Bettcher, business group leader and executive vice president for Emerson. “Historically, the Emerson Climate Technologies division provided compressors, valves, and electronic controls for supermarket applications. Today we are focused on integrating these core technologies with performance-based services, like e-commissioning, to deliver more powerful results for our customers.”
Bettcher went on to highlight one offering in particular: supermarket racks that can be configured with Copeland Scroll compressors and CPC’s Einstein controls, then monitored for optimum efficiency through a remote location.
The e-commissioning program (available through Emerson’s Retail Services Group) provides supermarkets with a comprehensive energy audit and continuous monitoring of HVACR, lighting, and building control systems.
— Peter Powell
Publication date: 08/05/2002