Its own regulations as a county, however, required proof of the drives’ ability to deliver meaningful energy savings before they could move forward.
Dominic Radosta of Capital City Mechanical, Norcross, Ga., explained that “This was a customer who trusted us for many years. We were doing a lot of their maintenance, service, and repair work.” This customer also has a substantial amount of motors, said Radosta; the contractor proposed the idea of installing variable-frequency drives (VFDs) as an energy use reduction measure.
Before the contractor could convince the client’s financial and operations directors, however, they needed proof that the drives would indeed reduce their energy consumption substantially.
The contractor called upon Yaskawa Drives, New Berlin, Wis., and Electronic Maintenance Associates, Norcross, to devise a testing program that would provide the evidence the county needed.
Capital City Mechanical is an HVAC commercial-industrial design-build-maintenance contractor that specializes in controls upgrades and new installations.
“Listen, then work” is the contractor’s motto; it’s “not the simplest way to do business. It’s simply the best way to do business.”
Side-By-Side Testing And Monitoring
Their proposal centered on retrofitting a VFD to an existing air-handling unit (AHU) in a county facility, Radosta said, and operating it in tandem with an identical unit using the existing constant-speed motor and mechanical inlet guide vane control system. The two units’ energy use was systematically monitored and operational costs were compared.The tests were conducted in two virtually identical sites selected by the county to have similar equipment and load profiles. Measurement, comparisons, and monitoring were handled by an independent consulting firm.
“We did the project turnkey and brought in the energy consultant to verify the results,” Radosta said.
The test sites selected by the county were the seventh and eighth floors of one of its most active downtown facilities, where courtrooms and other law-enforcement facilities required that cooling be provided around the clock, seven days a week.
The floors have similar layouts and circulation patterns, Radosta explained. They were cooled by identical variable air volume (VAV) AHUs powered by identical, constant-speed, 25-hp AC motors.
Existing control schemes used a combination starter running the motor at constant 100 percent power. Airflow was modulated by mechanical inlet guide vanes, which were pneumatically controlled through an aging building automation system.
To ensure accurate results, all parties agreed to methods for monitoring energy use, length, and conditions of the test period. Integrated Services Group, an independent energy consulting firm based in Atlanta, monitored, measured, datalogged, and tabulated energy use, and created reports.
Return air temperature and AHU power use for each floor were logged at five-minute intervals during the 13-day test. Return air temperature was also monitored to ensure that the new control scheme would positively affect tenant comfort.

VFD On Seventh Floor
A Yaskawa Model E7 HVAC-specific, 480-volt VFD was installed on the seventh floor AHU. The air handler on the eighth floor continued operating on the existing constant-speed, VAV system.Electronic Maintenance Associates provided installation materials and labor, and integrated existing controls into the drive wiring. The contractor completed installation and startup in less than a day.
The county engineering staff stated that they wanted to use the drive to maintain static pressure in the supply duct. A pressure transducer was installed in the ductwork to provide feedback to the drive’s PI control loop, with a setpoint of 1 inch programmed into the drive.
The inlet guide vanes on the seventh floor air handler were locked open, leaving the E7 drive in control of the supply air volume flow.
Monitoring covered the 13-day period from Aug. 30 through Sept. 11, 2002. Test results are summarized in Table 1.
Energy Savings, Payback
At the end of the test period, data showed an impressive reduction of nearly 72 percent in energy consumption on the floor where the VFD had been installed.Cooling on the seventh floor, using the VFD, required an annualized total of 29,960 kWh. The eighth floor, operating on the existing constant air volume system, required nearly 108,000 kWh to maintain the same cooling levels. That’s an annualized energy savings of 77,948 kWh.
Electrical rates paid by the county vary with demand and time-of-day charges, but average 4.45 cents per kWh. At that rate, based on an estimated $5,000 installed drive price, payback for this variable-speed drive is 1.44 years.
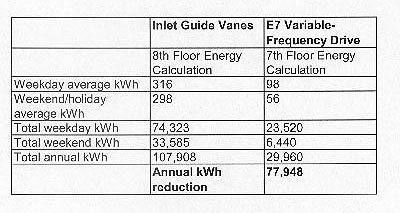
Calculated at the average cost of electricity in the U.S. (6.93 cents), the results are still more impressive. At the average national rate, the drive installation would provide annual savings of slightly more than $5,400 and a payback of less than a year. (U.S. DOE, Energy Information Association, “Electric Power Monthly Annual,” August, 2001.)
That payback period can be further shortened by rebates offered by many utility companies for installation of variable-frequency drives — often as much as $20 to $200 per horsepower.
How Drives Deliver Savings
A variable-frequency drive delivers its savings by controlling motor speed to provide only the precise airflow and pressure required to maintain desired heating or cooling levels.The drive’s ability to optimize motor speed reduces power consumption and produces significant energy savings — typically ranging from 10 to 75 percent.
In contrast, many of the county’s existing HVAC components employ a VAV approach, using mechanical modulation of airflow from a constant-speed fan. Fans and motors run at constant maximum speed while the volume of air is modulated by relatively inefficient mechanical devices, such as inlet guide vanes or outlet dampers.
In a typical building, maximum capacity is required only about 10 percent of the time; 90 percent of fan operating time requires only 40 to 70 percent of maximum volume (and, therefore, fan speed).
In the county’s facilities, as in most, applying 30 to 60 percent more energy to fan operation than was necessary wasted a significant amount of electricity and inflated the utility bills.
Reduced Maintenance Costs
VFDs also help cut into maintenance costs through their ability to deliver “soft” starts and stops. Accelerating or decelerating motors and mechanical equipment smoothly cuts down on mechanical stress and wear and tear that occurs when started directly across line power.Additionally, the inlet guide vanes’ mechanical linkage and bearings were a maintenance nightmare for the county, resulting in tenant comfort headaches for the building’s engineering team.
The results of this study — energy savings of more than 70 percent, short payback periods, reduced maintenance, and improved comfort levels — speak for themselves.
The county, with more than 600 buildings using more than 1,000 air-handling units, has the proof it needs to proceed on its drive retrofit program — and to begin to realize the savings.
“The customer loves it,” said Radosta. “They are trying to move forward to complete drive installations throughout the facility.” After that, this customer has more buildings, with more motors that could probably benefit from VFDs.
Phillips is regional drives specialist for Yaskawa Electric America Inc.; 800-927-5292, ext. 7801; 847-887-7310; www.yaskawa.com.
Publication date: 06/02/2003