
Some 34 technical papers and a keynote speaker focused specifically on CO2 during the quadrennial International Congress of Refrigeration (ICR), sponsored by the International Institute of Refrigeration (IIR). The paper count was a quantum leap above the single-digit number of papers on the topic at past conferences.
The ways offered to make CO2 create cooling were wide ranging, including use as a stand-alone refrigerant and in conjunction with such refrigerants as ammonia, propane, and HFC-404A.
In general, advocates of CO2 backed off on calling for their favorite refrigerant as a down-the-road replacement for HFCs. In fact, several speakers said HFCs would be around for a long time, especially in the United States. A position often stated was, “Consider CO2 as a refrigerant option. Give the customer a choice between HFCs and CO2 and drive down the cost of both through competition.”
Another theory advanced during the five days of seminars was that while HFCs could face cutbacks and even phaseouts in Europe, that scenario might not be the case in the United States. One speaker referred to this as the “Atlantic Divide.”
The CO2 topic extended be-yond the walls of the conference hotel in downtown Washington. Two of the technical tours touched on the technology.
During a visit to the York Refrigeration/Frick complex in Waynesboro, Pa., ICR attendees learned that the company has been doing studies on CO2 in conjunction with ammonia and as a stand-alone refrigerant.
At the Evapco headquarters and R&D facility in Taneytown, Md., it was noted that one of its test chambers is set up with CO2 refrigerant, “in order to perform detailed thermal analysis on steel evaporators using this alternative refrigerant.”
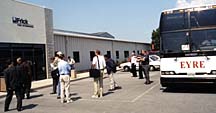
The Advocates
At the conference, seminars on CO2 were the most heavily attended. Among those calling for consideration of CO2 was Andrew Pearson of Star Refrigeration in Glasgow, Scotland. In his paper titled “Carbon Dioxide — New Uses for an Old Refrigerant,” Pearson urged audience members to “open your mind and think about future possibilities.”“The limiting factor for most carbon dioxide systems is currently pressure,” he stated. “This does not appear to be a long-term impediment, as compressors, pumps, valves, and controls are already on the market suited” for use with CO2, if not fully refined for such use.
He noted that initial development of CO2 systems on the industrial side is often done in conjunction with ammonia in cascades, but indicated downsizing is possible. “As compressor development continues and smaller machines become available, it will be possible to engineer packaged cascade plants comprising a semi-hermetic, carbon dioxide compressor of, say, 50-kW capacity, with a suitable ammonia or propane compressor, using brazed-plate, plate-and-shell, or micro-channel heat exchangers to give a low-charge, virtually leak-proof, compact installation using only ‘natural’ refrigerants.”
He listed five natural refrigerants: air, water, ammonia, carbon dioxide, and hydrocarbons, with the last three having “a broader range of applications.”
Lennart Rolfsman of York Refrigeration in Denmark predicted that CO2 will make an impact stateside. “To you from the United States, this technology is coming fast,” he told an audience with representatives from dozens of countries, including the United States. He noted that Europe is already starting to establish standards for the refrigerant.
His paper dealt with the components and physics of CO2 systems. He even took a gentle dig at those fretting about the pressures of carbon dioxide systems. “Outside of the refrigeration business, the pressure is not considered being high, although many old horses in this trade think so.”
He said the lubricant used with CO2 should be an ester oil, although there are other options. “One way is to use oil-free compressors; this works OK after the initial struggle, but to a higher cost both initially and for service. Another is to apply the ammonia principle, for example, a nonsoluble lubricant PAO [polyalphaolefin]. This [can be] correctly done in a safe way to handle the perceived inconvenience when mixing esters with ammonia.”
He noted a range of compressor options, including recips and screws. The most common defrost option is electrical, he said.
Rolfsman’s main argument was that the technology to head faster in the CO2 direction is pretty much in place; the roadblocks are elsewhere. “This hesitation to move in the direction of new solutions and new technology is to a large extent not only of psychological reasons, but also due to lack of this know-how among many companies.”
John Fleming of the Department of Mechanical Engineering at the University of Glasgow, Scotland, voiced the idea of CO2 existing in harmony with HFCs. “A total ban on HFCs is unlikely,” he said, so CO2 should be considered. “CO2 would be another refrigerant” and would compete with HFCs.
He reported on the performance of a trans-critical CO2 heat pump using a reciprocating compressor. The findings produced mixed results, he said, calling for further studies.
Expanding Options
Other speakers focused on the range of options.Sergio Girotto of Costan in Italy reported on work he did with Petter Neksa of Sintef in Norway. The focus was on commercial refrigeration applications. They conducted comparisons with systems that today most commonly run on HFC-404A.
They noted that “The total annual energy consumption of the installed CO2 system is estimated to be about 8 to 10 percent higher than the equivalent R-404A solution.” They also estimated that the CO2 installation would be about 10 percent more expensive.
They said that those differences could be overcome. “We are confident that in the future, all CO2 systems can be made as efficient as a good R-404A system.”
In the area of supermarket refrigeration, Frank Elefsen and Stephen White of CSIRO Energy Technology, Australia, compared a CO2/HFC system, a traditional direct-expansion system using an HFC, and a type of secondary-loop system Elefsen called “an in-direct HFC/brine system.”
They reported the following key findings:
The presenters asserted, “It is without any doubt that CO2 will be introduced very fast in supermarket refrigeration, with an environment and economical benefit for the industry and society.”

Walk-Ins, Transport
A report from researchers in Denmark described efforts to operate walk-ins with CO2 and propane instead of R-404A. The move, said presenter Kenneth Madsen of the Danish Technological Institute, came as the result of efforts in Denmark to phase out the use of HFCs.“The system was built in Denmark in 2002 as part of the first HFC-free restaurant in the world,” said Madsen. “The system contains a propane/CO2 cascade system. CO2 is used both in rooms with direct expansion in the (freezer) room and a flooded evaporator with natural circulation in the (cooler) room.
“Laboratory tests show that the unit performs as well as or better than the conventional 404A unit. The system uses less energy and combined with the low GWP for the refrigerants, the system has a TEWI that is reduced 35 percent compared to similar R-404A system. Energy consumption is reduced by 2 to 4 percent, according to the simulations.”
CO2 also turned up in transport refrigeration. A paper from Herman Viegas of Thermo King, Minneapolis, reported on the use of liquid CO2 that “provides all the energy needed to refrigerate cargo and provide mechanical energy to move air.”
He added, “Unlike liquid injection systems, the carbon dioxide does not enter the cargo space. This is an open system when the carbon dioxide is expended to the atmosphere after useful energy is extracted.
“A microprocessor-controlled flow control valve meters liquid to an evaporator coil, which is maintained above the triple point by a back-pressure regulator. The vaporized carbon dioxide gas is then expanded in a custom-designed, high-efficiency, vane-type rotary motor. A blower is mounted to one end of the motor shaft to provide airflow, and a small alternator is mounted at the other end of the shaft.”
He maintained that the approach removes global warming concerns, eliminates emission issues when diesel is the alternative, results in low noise, and offers rapid pulldown.
“You are not going to buy this to save money,” he admitted, referring to initial costs. But he noted that in Sweden, where CO2 refrigeration has caught on, cost comparisons with more conventional approaches “results in a wash.”
He joined the chorus of his colleagues in contending that a move to CO2 “is not so much dependent on technical success but rather on people-related issues.”
Distribution warehouses also offer possible CO2 applications. Andrew Pearson and Paul Cable of Star Refrigeration in Glasgow noted, “HFCs have failed to replace R-22 and R-502 in industrial cold storage systems, but for some end users, ammonia is not acceptable in direct systems.
“Carbon dioxide was selected as the preferred refrigerant for a distribution center built in Scotland in 2003 for a supermarket chain.”
The presenters did note that CO2 systems typically have “difficulty in achieving cooler defrosts by traditional hot gas methods,” and “the pressures used in the carbon dioxide systems are generally limited by available compressor technology.”
To work around this, the engineers decided to go with a combination ammonia/CO2 system with some modifications that departed from the direct system approach. Said Pearson, “It was concluded that there would be capital, operational, and environmental benefits if a two-stage cascade system could be designed to cover the four temperature levels.”
Yeah, But …
Throughout the dozens of CO2-related papers, presenters seemed to be anticipating “Yeah, but …” challenges from those who could not see CO2 becoming a widespread refrigerant. This attitude extended to the air conditioning side.Hans-Joachim Huff of the University of Maryland noted, “One of the major challenges with CO2 in air conditioning applications is the low energy efficiency of the system at higher temperatures in the heat sink. (But) the energy efficiency of a trans-critical CO2 air conditioning system can be improved significantly when the throttling valve is replaced to a work-producing expansion device, an expander.”
Huff and his colleague, Reinhard Radermacher, worked on a project involving two automotive R-134a scroll compressors that were modified for use as expanders with CO2. Initial results were mixed, Huff reported.
“An increase in the oil flow rate through the expander did not improve the expander performance. However, this result should not be generalized. At smaller gap sizes and lower leak rates, the oil is expected to have more benefit on the sealing. The effect must be reinvestigated with a better prototype.”
Another study on expanders by a team from Dresden, Germany, used “three pull-pressure expansion stages in series, whereas the compression is still done by one double-acting piston in line with the expansion stages.” The expander aspect was covered in several other papers as well.
More Research Needed
Nearly all papers included a call for additional research to fine-tune findings. A number of papers also provided a range of statistical information for the industry to consider when doing additional research.The question of the evaporative heat transfer characteristics of CO2 was explored by a five-person team from the National Institute of Standards and Seoul National University. The researchers used “a concentric tube heat exchanger heated by water in the annulus with CO2 in the central tube.” The detailed findings were compared to “existing correlations for a two-phase average evaporative heat transfer coefficient.”
Other studies focused on oils and compressors. The solubility of CO2 in synthetic oil was studied by a team from two research facilities in France, and focused on “saturation pressure seven to eight times higher than that of R-22 or R-134a.” The study dealt with PAG-type (polyalkylene glycol) oils.
A hermetic, two-stage, carbon dioxide compressor was studied by a team from Purdue University. They stated, “Compressor tests were conducted for varying suction temperatures and pressures, and discharge pressures.”
Reasons for the focus on CO2 varied from curiosity about a refrigerant that has been around for a long while to a sense of urgency, especially in Europe.
An example of the latter was a report from researchers from a number of Dutch agencies. The report, “CO2 Systems Are Sweeping through the Netherlands,” states that the reasons range from “stringent environmental legislation,” to “financial support schemes of the Dutch government,” to “successful research and start-up of the first projects.”
Publication date: 09/08/2003