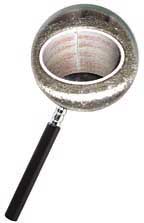
To help clear up some diagnostic misconceptions, therefore, The News and Copeland have developed this series of articles on compressor failures — why they happen, who’s at fault, and what technicians need to know to prevent misdiagnoses.
Compressor failures in some cooling systems are like heart failures in some people: You can’t tell the wife of a guy with a knife in his back that he died of heart failure.
Names and situations have been changed to protect the innocent. We would be surprised, though, if they didn’t look familiar.
Setting The Scene
John and Joan live in a suburb of Houston, in their first house. They moved to Texas from Minnesota the year before, and this last October they made the commitment of buying a house, saying goodbye to apartment life.They both work in downtown offices. Since they quit smoking and started working out at the gym before going home, they usually come home around 7:30 or 8:00 p.m., to two cats.
In April the temperatures outside started climbing into the 80s, getting a little warmer every day. John and Joan learned more about the joys of homeownership, such as mowing the lawn and washing the windows — the obvious things. The heat pump started switching over to cooling during the day. They weren’t home to experience it. At night they only needed the house fan and ceiling fans.
What The Customer Saw
One weekend, while they were working on projects at home, it got particularly hot and humid — not as hot as it would get later in the summer, but hot enough to make them want air conditioning.“Hey,” said John as he came in from lawn mowing, opening a beer, “put the air conditioner on.”
Joan went to the thermostat; it was set on “auto” and 76 degrees F; the room temperature read 80 degrees. “Uh oh,” she said.
John came over to the thermostat. “What does ‘uh oh’ mean?” he asked.
“I don’t think it’s working,” she answered.
John frowned and tapped the thermostat a couple of times. Then he reset the temperature to 72 degrees. “It should work pretty soon.”
Temperatures outside got up around 90 degrees that day, with 70 percent relative humidity (rh). It was close to 84 degrees inside John and Joan’s house. They were thumbing through the phone directory, looking for an air conditioning contractor. They eventually found an ad that said, “Fast Service, Even on Weekends!” Joan called while John stood in front of the open freezer door, wondering if he should stick a pair of shorts in, like that guy did in the soft drink commercial.
After waiting on hold 15 minutes, John and Joan were given the next available service appointment — for the next day, Sunday. “Isn’t there any way someone could come today?” asked Joan.
“I’m sorry,” said the frazzled but polite receptionist. “This is our first hot spell, and the phone always rings off the hook. I did give you our next available time. Of course, being a weekend call, we will have to charge double our normal service rate; whether or not any warranty applies depends on what our technician finds when he gets there. Will you be paying with Visa or MasterCard?”
“Visa,” said Joan, with a sinking feeling.
They opened their windows that night, but there was little breeze except for the air circulated by the ceiling fan. A storm was coming the next day. Neither of them slept well. Just as they were nodding off, they heard the loud hum of their heat pump, and the softer hum of their neighbor’s heat pump in the distance.

What The Technician Saw
Terry the service technician arrived at John and Joan’s home by 10 a.m. on Sunday, much to their relief. He looked at the thermostat; it was still set on 72 degrees, and the home’s temperature was already 77 degrees. “Was the air conditioning on all night?” he asked. They answered in the affirmative. He went outside.The unit was still running. After connecting his gauge to the service port for this R-22 system, he measured the suction pressure: 60 psig. He also measured the suction line temperature with a surface temperature probe. The suction line temperature was 34 degrees.
Terry determined there was no superheat by converting the suction pressure to temperature using his handy refrigerant pocket guide (60 psig = 34 degrees) and comparing the saturated temperature on this chart to the line temperature. They were the same.
“I need to see the indoor portion,” said Terry. Blank looks from John and Joan. “You know, where the filter is,” said Terry.
“Filter?” asked John.

The Culprit
The indoor coil was located in a crawl space over the garage port. Terry climbed in with his tools; the cardboard frame filter had accumulated so much dirt, the media had separated from the frame. Dirt had also accumulated on the indoor coil, and that dirt turned into a kind of muddy paste because of moisture.“Here’s the culprit,” said Terry.
“What is it?” asked John.
“This isn’t pretty,” warned Terry, passing the dilapidated filter down to John. “These filters need to be changed at least every three months,” Terry said. “Have you ever put a new filter in here?”
Joan gasped and turned away. “No,” said John. “We didn’t even know about this place in the attic.”
“See, when a filter loads up with this much dirt, it can’t send enough air to the system for proper heat exchange,” explained Terry. “When the coils get in this kind of shape, it gets even worse. Your compressor has been running with liquid refrigerant flooding back to it. Compressors, even scrolls, are designed to pump gas, not liquid. This is why I did a superheat check to determine what was going back to the compressor.”
(Service note: This system used orifice refrigerant controls. Had the system been constructed with thermostatic expansion valves, there probably would not have been any floodback, but the compressor could have overheated once the evaporator iced over and the suction pressure went lower.)
“How bad is it?” asked Joan.
“From the sound of it, your compressor seems OK,” said Terry quickly, “but I will have to check it out once I have cleaned the coil.”
Once the system was in operation, Terry again checked the suction and discharge pressures and the suction line temperature. Because the airflow had been restored to normal and the indoor coil was clean, the suction pressure had risen to 75 psig (which converted to 44 degrees saturated suction using the pocket reference guide). He again measured the suction line temperature and found that it now was an acceptable 15 degrees to 20 degrees warmer than the saturated suction temperature.
Terry knew from these readings that the compressor was probably OK and had not become inefficient due to wearing or scoring of sealing surfaces or bearings. Just to be sure, he did an efficiency test. He measured the compressor’s amp draw using the common line from the compressor and wrote down the suction and discharge pressures. He would later compare this to the compressor manufacturer’s data sheet.
He knew that an amperage reading within plus or minus 10 percent of the manufacturer’s specification would mean the compressor was running within acceptable limits. He also knew that an inefficient compressor would result in abnormally high suction pressure and lower-than-expected discharge pressure.
The Consequence
John and Joan paid for the repair. It wasn’t as expensive as it might have been if the problem had happened later in the summer, when air conditioning service is at its peak.A less-experienced technician under excessive time constraints might not have checked for superheat; instead, he might have taken out the old compressor — which still worked — and put in a new one in an attempt to increase unit capacity.
The homeowners would not have learned about the filters or coils — yet. The new compressor still would not have pulled the indoor temperature down, necessitating another service call.
As it was, Terry sold them a service contract. He sees them twice a year to clean the coils, check the motors, and check the refrigerant charge. John and Joan change the filter themselves, every three months; more frequently when the cottonwood is flying.
Floodback
Terry has improved his troubleshooting skills by performing teardowns on compressors that are no longer under warranty. He used a handheld grinder to grind through the girth weld. He has also attended compressor teardown classes held by the manufacturer.The problem in this case was the result of floodback — a system problem, not a compressor problem. Floodback occurs when liquid refrigerant returns to the compressor during the running cycle. There can be multiple system causes.
The metering device may lose control, but this does not mean it is a metering device problem. If the evaporator coil freezes over or an evaporator blower fails, for example, the liquid will not be properly evaporated and liquid returns to the compressor. The excessive dirt built up on the evaporator coils in this case prevented proper airflow and evaporation of the liquid refrigerant.
Depending on the style of compressor, different failure patterns will be found. A refrigerant-cooled compressor such as a scroll requires the return gas to flow across the motor before entering the compression chamber. The liquid refrigerant would mix with the oil in the crankcase and would result primarily as low-end wear, such as worn bearings. In his dissection of a refrigerant-cooled, welded compressor, Terry saw damage to the running gear, bearings, rods, and crankshaft areas.
Liquid refrigerant displaces oil as it travels through the crankshaft. Also, liquid refrigerant is a solvent and washes the oil film from adjoining surfaces; this, in turn, causes wear. Scoring may be evident.
“The Compressor Mysteries” are a collaborative creative endeavor between The News and Copeland Corp., an Emerson Climate Technologies company. Sam Gauge can be reached by calling Barb Checket-Hanks at 248-244-6467; barbarachecket-hanks@achrnews.com. For more information on floodback, please visit www.EmersonClimateContractor.com.
Publication date: 04/28/2003