The variety of methods used is unknown, but there are a number of them. The difficulty with each one is that none of them will give the precise charge amount of refrigerant required.
The result is loss in efficiency, and longer compressor run time. The waste of electrical power, and higher electricity expense, is incalculable.
A new refrigerant charging device (patent pending) has been developed to supply a simplified method of providing more precise system charging. It is intended to give technicians an easy and more accurate way to charge. It assures the correct method of refrigerant charging, without consulting tables and using pressure and temperature gauges. This article details the invention.
The Refrigeration Cycle
Figure 1 shows a refrigeration cycle superimposed on a Mollier diagram. This diagram is an engineering tool, and a lot of detail is not required for these purposes, other than it shows the properties of a given gas/liquid.
Following the cycle on Figure 1:
A-B (compression) - Superheated gas is compressed from the low pressure (cooling coil) to high pressure in the condenser.
B-D (condensation) - Heat is rejected, by fan or water cooling, at nearly a constant pressure. The superheated refrigerant vapor is condensed to a slightly subcooled state. Note the line crosses the saturation line, and extends slightly to its left.
D-E (expansion) - The high-pressure liquid from the condenser is throttled through a control valve into the cooling coil. This is called expansion, where the liquid is sprayed into the coil, which is at low pressure, supplied by the suction of the compressor.
E-A (heat absorption) - The spray from the expansion device absorbs heat as it passes through the evaporator coil. As the name implies, all the liquid droplets evaporate, and absorb heat in doing so.
The term enthalpy is the measure of heat, expressed in Btu/lb. The values in the cooling cycle are approximately 105 and 44. The difference is the amount of cooling in the evaporator, or about 61 Btu/lb.
Condenser coils are designed to allow some 10 percent of the coil for subcooling liquid refrigerant. This simply means moving Point D to the left, as shown in Figure 2. This is a must, in order to supply all liquid to the expansion valve, with no entrained gas bubbles.

There is a limit to the degrees subcooling in the condenser, and the system must be charged correctly to obtain this value. Subcooling is decreased through the system, because of pressure drops in the tubing, evaporator elevation above the condenser, as well as liquid lines running across hot roofs and attics. Any of these, or combination thereof, may cause the evaporator to be underfed, because of gas bubbles entrained in the liquid. It is critical, therefore, to system efficiency to properly charge the system.
It is not simply good practice to maintain 100 percent liquid to the expansion valve. It is imperative. Otherwise, there will be additional running time requiring more electrical power, and system efficiency will be lowered significantly.
To see the efficiency gain with proper subcooling, one needs only to look at Figure 2 and see the Btu gained per pound of refrigerant. However, if gas bubbles are in the liquid line, the loss in efficiency can be substantial. Looking at Figure 1, this would place the reference line at Point D farther to the right, depending on the degree of gas at the expansion valve.
Unfortunately, with this problem nothing will show up waving a red flag. The inefficiency gets buried in the customer's electrical bill. But it makes no sense to waste electrical resources in today's economy.
Checking subcooling is done by measuring the temperature and pressure at the condenser outlet. Available charts show the degree of subcooling. However, it can be difficult to get techs to do this. The methods used to determine proper refrigerant charge are as varied as the personalities of the techs - one of which is that the "compressor sounds right."
Many systems have a liquid line sight glass at the condenser or receiver outlet. The inlet of the sight glass, or receiver, is supplied refrigerant from the last row of tubes in the condenser. Technicians charge until the sight glass has no more gas bubbles, but this simply means there are no bubbles in the last tube. This does not take into consideration the remainder of the coil which is devoted to subcooling.
This is at least better than remote A/C units, which generally do not have a sight glass, and a "seat of the pants" method may be used for charging.

The Elements Of The New Charging Device
The first part of this invention is the charging tool. This tool is used to its best advantage if the condenser coil is modified. Thus, the second part concerns a minor modification of the condenser coil. The first tube in the subcooling circuit is fitted with a special return bend, having a stub tube in the side for subcooling checks. The third part of the invention is a simple method of remotely checking the sight glass.The charging tool (Figure 3) has a small orifice, 0.010 inch or less. It is typically used with a standard sight glass, as shown in Figure 4.
For the return bend in the coil (Figure 5), the coil manufacturer would add this in the first row of the subcooling section of the condenser. Any method using the last tube in the condenser will bear no relationship to the additional amount of refrigerant required. The modification would allow the tech to check the subcooling level, since a conventional sight glass only indicates the condition in the last tube.
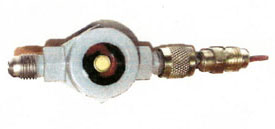
There is no comparison between checking liquid level from the last tube in the condenser and the level at the first tube in the subcooling circuit. If this revision is part of the condenser, charging can be done in the most efficient way possible, assuring the best possibility of solid liquid at the expansion valve.
A special sight glass may be installed in the liquid line near the expansion valve to allow the tech to monitor refrigerant level from a remote location. This is basically a normal sight glass incorporating a sensor with output connected near the condensing unit, for remote checking (Figure 6).

The most basic output would be a green LED for refrigerant OK, or a red one to add charge. The tech would simply charge until the green LED lights.
Using the feedback in conjunction with an alarm, this may alert a supermarket owner of low refrigerant. Leaks may then be repaired quickly, without the loss of a great deal of refrigerant. Supermarket installations can lose hundreds of pounds of refrigerant should a leak continue until the system malfunctions.

How The Basic Device Works
The charging tool, as noted above, is generally used by attaching it to a standard sight glass. The other end is attached to the high-pressure fitting on the charging manifold. The valve is tightly closed, and a hose is attached from the sight glass inlet to the system high-pressure fitting. A quick disconnect fitting is recommended.The other hoses are hooked up in the usual manner, and purged with refrigerant to remove air. The high-pressure manifold fitting is loosened and purged for a few seconds.
After all the hoses have been hooked up, the tech starts the compressor, opens the low-pressure manifold valve, and slightly opens the high-pressure valve. The sight glass is held in the horizontal position, for easy viewing.
If the unit is low on refrigerant, the line to the sight glass will quickly warm. After a short time period, charging is started, liquid begins to appear in the sight glass, and the liquid level will continue to rise. Normally, a few gas bubbles appear, but as charging proceeds, the sight glass fills up. Once it is completely full of liquid, the system is properly charged.
If the proposed modification on the coil is in place, correct subcooling will be a simple matter, by hooking the gauge to the subcooling loop. If the coil is not modified, the charging tool will give results equal to a sight glass. If no sight glass is installed, the use of this tool will ensure proper refrigerant level. This is especially critical on small deli cases, salad bars, beer coolers, etc.
John T. Eschbaugh, P.E., inventor of the refrigerant charging device, is a 40-year veteran of the HVACR industry. He has worked for a major refrigeration equipment manufacturer and a valves and controls manufacturer, as well as his own A/C and refrigeration service business. For more information, call 440-729-4069 or e-mail pushpull@excite.com.
Publication date: 06/28/2004