The 52 contestants had made their way around eight workstations, demonstrating their skills to the judges. In each instance, they were given a specific problem (usually in the form of a customer complaint) and had to call upon what they had learned to diagnose and repair the problem.
When the last competitor had finished, contestants regrouped and representatives (who acted as event captains) from the eight manufacturers who had set up equipment and "created" the problems, each took a few minutes to describe the problem and how it might have been resolved - as well as offer a few general comments.
It would be another day before the contestants would officially know how they did, but the debriefing did bring a few knowing nods, as well as a few self-imposed head slaps when the proper procedure was explained.
Here is a sampling of what the industry experts had to say.
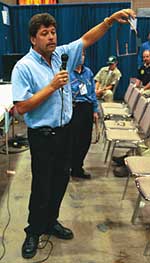
Steve Brown of Emerson Climate Technologies said the contest for servicing indicated some confusion on how to do a proper pumpdown.
"Get with your instructors back at your schools and get some extra tutoring in that area."
In the SkillsUSA event, the pumpdown was needed in order to change out a low-pressure control, set the control based on proper cut-in and differential. The process, Brown said, involved them going back with a manifold gauge to make sure the control was cutting in and out at specific pressures.
"There are a lot of good manufacturers of pressure controls, but the scale on the face is only going to get you in the ballpark," Brown said. "You have to go back and follow up with manifold gauges."
Robert Mikell of Carrier said the residential air conditioning mechanical issue focused on measuring the air going through the system. He noted two methods, temperature rise and velocity, with temperature rise being the easier and most commonly used today, especially with the availability of voltmeters, amp meters, and thermometers in the field.
Contestants also needed to determine suction gas superheat on the charging side using fixed metering devices. Procedures, he said, were as important as outcome in scoring.
Lynn Bosse of Lennox told contestants the residential air conditioning electrical issue concerned a unit that was installed the night before and ran all night, creating an extremely cold house. The problem related to incorrect wiring at the thermostat that resulted in the blower running constantly.
Bosse said judging was based not only on finding that problem, but explaining the situation clearly to the customer, "so the customer will have confidence in you and call your company back the next time service is need."
Bosse advised, "Listen to what the customer says, and he will steer you in the right direction."
Bosse also encouraged the young technicians to get a thorough knowledge of electricity, which can be involved in 60 to 80 percent of service work.
Jerry Meyer of Hussmann (Ingersoll-Rand) said the situation for the refrigerated display case dealt with an open contact on the defrost timer. Rather than just automatically replacing the timer, the contestants were expected to verify the voltage on both sides of the timer, then double-check with an ohmmeter.
The basic skill needed, he said, is the ability to read a wiring diagram and use a meter while following the diagram. Those who could do so completed in the task in a matter of a few minutes, he said. Those who could not read a wiring diagram struggled through the entire 15-minute time limit.
Jim Knutson of Scotsman noted that because ice machines may not be given much emphasis in classrooms, contestants were able to review manuals the day before that would pertain to equipment used in the contest. The assumption was that such publications should be available to technicians on a service call, to eliminate the need for guessing and parts changing.
In the contest, competitors were asked to determine model and serial numbers displayed in several areas on an ice machine, identify components that could be found in the manuals, use a meter to determine voltage, and run a diagnostic, again by following steps in a manual.
Rick LeBeau of JKL Technical Sales said the use of manifolds and vacuum gauges was second nature to most contestants, but many were still unsure about recovery equipment. LeBeau said part of that might be based on fear. He pointed out that such machines are fairly basic pieces of equipment with inlets and outlets. "Spend a few minutes to look at the recovery machine, then think through what you are going to do before hookup."
Another area that needs attention in schools, he said, is work with micron gauges, especially since such gauges are becoming more and more important as the industry moves to POE oils.
Raymond Granderson of Rheem said a problem set up in the contest's furnace was one that "is not uncommon." The storyline involved a homeowner who had a furnace quit and first called her brother-in-law to try and fix it; he tinkered around for a while but could not fix it. So a technician was called to deal with an "anything is possible" situation.
The board was flashing a three-fault code, "trying to tell you what was wrong," and the overtemp limit was open. By using a voltmeter and working through various possibilities, the technician should have been able to trace the problem to incorrect polarity, he said.
For more coverage of SkillsUSA, read the exclusive online feature titled "Careers Are Just Beginning For Contest Finalists," which covers Ruth King's words of advice for the competitors.
Publication date: 08/02/2004