
While the 2005 hurricane season in Florida has not been nearly as brutal as last year, Aggreko will be ready if that changes. Aggreko, a supplier of temporary power, temperature control, and compressed air services, performed numerous hurricane-related jobs in Florida last summer as hurricanes Charley, Frances, Ivan, and Jeanne visited the state.
"Damage from the storms was extensive," said Tim Ainslie, Aggreko Southeast area sales manager. "A combination of flooding, wave action, and high winds had damaged the exterior and foundations of many coastal facilities, allowing water to penetrate throughout building interiors."
Aggreko teamed up with Belfor, a provider of fire, water, and storm damage repair services, to provide drying and restoration services for hotels and commercial environments in the area.
"Job sizes ranged from 3,500 cfm to 120,000 cfm," said Ainslie. "Aggreko utilized over 200,000 cfm of desiccant dehumidifiers, along with over 12 megawatts of generator power, consisting of more than 50 individual units."
These jobs included a luxury resort that suffered extensive water damage after being struck by a category four hurricane. Aggreko provided 40,000 cfm of drying equipment for restoration work at the resort, eliminating concerns about mold growth and contamination and allowing the resort to reopen quickly.

Getting It Done
In order to address water damage effectively, Aggreko takes the following steps:
"High humidity can be rapidly controlled with the proper use of dehumidification equipment. However, saturated materials are the major problem," said Robert Peetz, Belfor operations manager.
Belfor, which has a strategic alliance with Aggreko, specializes in eliminating the source of water damage, which involves the cleaning and treatment of HVAC systems, as well as damaged content and substructure to eradicate irritants, pollutants, and potential health threats. Hurricane damage mitigation is directly correlated to response time and the utilization of effective restorative techniques.
"Wall cavities provide notoriously great host environments. They are dark, have negligible airflow, are not climatically controlled and provide the preferred nutrients of cellulose - a major component of wood. Only water is required to tilt the scales in favor of mold growth. Without the knowledge, techniques, and equipment to control and dry this hidden moisture, an ordinary cleanup and drying project can quickly turn into a major mold remediation project," said Peetz.
The projects varied greatly in damage, with some being completed in three days while others took several months.
Water is a principal source of contamination and corrosion, and has a direct and indirect impact on structure, contents, computers, records, machinery, work in progress, and other essential business functions.
After the damage occurs, removal of surface water is the first step; however, buildings may still contain high levels of moisture. It can take up to six weeks to completely dry a building, even with dehumidification equipment installed. Water may reside undetected under floors, causing deterioration of building foundations.
Water can penetrate conduits, causing long-term corrosion and electrical safety hazards. Fresh water can pick up chemical contaminants from building surfaces, which can be harmful when deposited on sensitive equipment. Water ingress can cause short circuits and electrical damage to equipment. Paper, books, and documents that become wet can additionally suffer mold growth and subsequent deterioration.
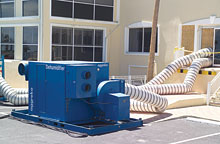
Strategic Alliance
This was not the first time Aggreko and Belfor had worked together. Major joint projects have included restoration work resulting from Tropical Storm Allison in Houston, and recovery work in New York City at Ground Zero."Aggreko and Belfor formed a strategic partnership to offer businesses priority service that guarantees the availability of the experts, equipment, and manpower necessary to put them back in business fast," said Gordy Broussard, Aggreko vice president and west area general manager.
"Under the agreement, Aggreko's temporary power, dehumidification, temperature control, and electrical distribution equipment is used in conjunction with Belfor's specialized emergency response capabilities and disaster recovery services to provide a single, cost-effective, time-sensitive solution to companies of all sizes."
Aggreko's dehumidifiers have been successfully applied in numerous manufacturing and restoration settings, such as reducing the drying time for wet concrete, speeding up painting and coating operations, or minimizing corrosion. The units have also been applied in process applications, such as stabilizing or preserving food products.
The dehumidifiers are also used in combination with its portable air conditioning and heating equipment, air handlers, and chillers to provide a temporary solution while contractors perform planned or emergency repairs on permanent HVAC systems.
Publication date: 08/15/2005