Bob gets a call from the dispatcher that a drug store is having trouble with its cooling system. It seems that the system had been working well until yesterday afternoon when it began to get warm in the store. It is a 7.5-ton unit with a reciprocating compressor using R-22.
Bob arrives at the store at about 10:00 am and goes to the manager. She explains, "The system is about nine years old and has never had any major repairs, just a condenser fan motor about three years ago. We keep the filters changed on a regular basis. The outdoor unit is on the roof."
Bob leans his ladder on the building to have access to the roof. He loads some tools in a canvas bag and ties a rope to it so he can climb to the roof and pull the bag up once he is on the roof. When he and his tools get to the unit, he notices that the fan is running, but not the compressor. He thinks, this is a classic case of low charge, with a hot compressor shutting off on internal overload. He removes the compressor compartment door and checks the compressor, and it is too hot to touch.
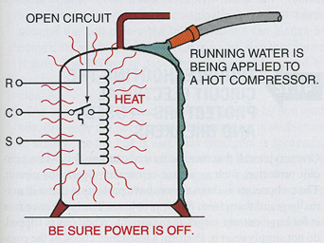
After the water has run over the compressor for about 15 minutes, Bob switches the power on and the compressor starts up. He watches his gauges to get ready to add refrigerant, but the suction pressure is not low, and the head pressure is normal for the conditions. The suction pressure is 80 psig and the head pressure is 300 psig. He decides not to add refrigerant but to observe the pressures. As he is watching the pressures, he feels the compressor. The suction gas returning is really cool, but the compressor is not cooling down. He touches the discharge line and it is very hot. He drips some water on it from the water hose and it boils away quickly.
Bob scratches his head.
Btu Buddy appears and asks, "What seems to be the problem?"
Bob says, "I don't know. This compressor is running really hot, but everything else seems normal. There seems to be enough refrigerant returning to cool it, but it is not cooling it."
Btu Buddy says, "The heat must be coming internally from the compressor. Get a long screwdriver and place it on the discharge line close to the compressor and put your ear to the handle. This is a poor man's stethoscope. Then turn off the power and listen."
Bob gets everything in place and shuts the unit off with the disconnect switch. A funny look comes across his face and he says, "I hear a hissing inside the compressor."
Btu Buddy says, "Feel the suction line now."
Bob says, "It is getting warm. It is not staying cool like it was. I don't get what is going on."
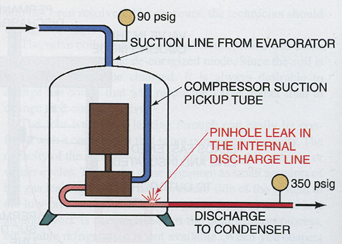
Bob then asks, "What if this had been a scroll compressor?"
Btu Buddy says, "Good question, Bob. A scroll compressor is a little different from a reciprocating compressor in that the pressures internally to the compressor will equalize when shut off, but there is a check valve in the discharge of the compressor that will keep condenser hot gas from backing up into the low side of the system. The funny sound that a scroll compressor makes at shut down is the high-side gas in the compressor backing up through the compressor to the low side. This is a small volume of hot gas. Not enough to warm the suction line."
"Well," says Bob, "I guess the next thing is to break the news to the store manager with a proposal to change the compressor."
Btu Buddy says, "That is all you can do for this system."
Bob then asks, "What may have caused this internal leak?"
Btu Buddy says, "It could be several things:
1. It may be a vibration leak at a weak braze joint.
2. It may be a leaking discharge reed valve in the compressor head.
3. It may be the internal relief valve leaking.
If the internal relief valve is leaking, it may be because of high pressure differential between the low and the high side, such as may occur if the condenser fan is not running all of the time. When we get the compressor changed, we will check the condenser fan closely."
Bob writes up a proposal in his service book to change the compressor and goes in and talks to the store manager. He explains, "This covers the changing of the compressor. I suspect that the fan may be the cause of the problem, but I want to check that out after the compressor is changed."
The store manager signs the proposal and asks Bob to get it done as soon as he can.
Bob assures the manager that he will work on it non-stop until the job is done.
Changing The Compressor
Bob gets the parts and arranges for a lift to help get the new compressor to the roof and the old compressor down. He also asks for a helper to move the compressor around, as it is heavy.After the compressor is changed and the unit is started up, he starts checking the fan motor by checking the amperage. The amperage is running a little high. Bob lets it run for a few minutes; the fan motor shuts off. He has found the cause of the problem.
Btu Buddy then says, "It may be the fan motor or it may be the capacitor for the motor. A motor will run high amperage if the capacitor is defective."
Bob shuts the unit off and uses his capacitor meter to check the capacitor. Sure enough, it is defective. He gets a capacitor from his truck as a replacement and installs it. He then starts the unit up again. When he checks the fan amperage, it is normal.
Btu Buddy says, "A defective capacitor can cause about a 10 percent increase in amperage in a fan motor. The motor will run for a while and then shut off because of internal overload. I think you have found the root cause of the compressor failure."
Bob then asks, "What caused the capacitor to fail?"
Btu Buddy explains, "It must be a random failure. Normally they last for what seems to be forever. A line surge may have damaged the internal insulation. You sure do ask a lot of questions, but that is good. You should be curious about failures. That means you will understand the internals of all of the components. It will prepare you for becoming a master technician."
Bill Johnson has been active in the HVACR industry since the 1950s. He graduated in gas fuel technology and refrigeration from the Southern Technical Institute, a branch of Georgia Tech (now known as Southern Polytechnic Institute). He taught HVAC classes at Coosa Valley Vocational & Technical Institute for four years. He moved on to become service manager for Layne Trane, Charlotte, N.C. He taught for 15 years at Central Piedmont Community College, part of this time as program director. He had his own business for five years doing installation and service work. Now retired, he is the author of Practical Heating Technology and Practical Cooling Technology, and continues as a co-author of Refrigeration & Air Conditioning Technology, 5th Edition, all published by Delmar Publishers. For more information, he can be reached at 704-553-0087, 704-643-3928 (fax), or bmj@myexcel.com.
Publication date: 06/27/2005