Established in 1971, the University of Kansas School of Medicine-Wichita is housed in a 150,000-square-foot learning complex in north central Wichita. Here third- and fourth-year medical students undergo clinical training. First- and second-year students study at the University of Kansas School of Medicine-Kansas City. About 100 students study annually at the Wichita facility, and unlike traditional school settings, the school's students spend much of their time outside the classroom working under physicians in the community's hospitals.
The school consists of two buildings connected by a corridor. The original three-story building houses patient-care and psychiatry clinics, student laboratories that simulate medical scenarios, a library, and a bookstore. The new one-story building holds administrative offices and a research area. While not as vital as it would be to a surgery center, air conditioning is still necessary to the school's operation. "Everyone wants to be comfortable," says Leabo. The cooling season stretches from March through November most years.
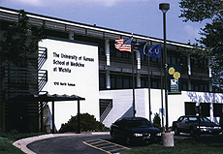
Single-Chiller Buildings
Each of the two buildings has a central cooling system, with chilled water being supplied to the building's air handlers. In the older, three-story section, chilled water was produced by a single 275-ton water-cooled centrifugal chiller. This high-pressure gear-drive machine was 22 years old and was located in the center of the basement of the older building. It started up normally in March 2002, but a few weeks after spring startup, it unexpectedly failed, and preliminary indications were that there had been serious damage to the chiller. The breakdown occurred during a period of unusually warm April weather.Leabo turned to Craig Singer, an existing building sales representative with Trane's Wichita sales office. Leabo had worked with Singer before and trusted his judgment. The two soon would be key players in the chiller changeout. When Singer received the call to evaluate KU School of Medicine's ailing chiller, he sent Curtis Beauchamp, a Trane service technician, who, ironically, had overhauled the machine 10 years earlier.
Chiller Severely Damaged
Beauchamp opened the chiller and his suspicions of major damage were confirmed. "We got it opened up and it was really torn up inside. Those are real high-speed machines," he said. "It had just disintegrated - things were so badly damaged we would have had to replace elements that you don't normally have to replace."Singer evaluated the level of repairs required and suggested that Leabo instead consider replacing the machine with a new 280-ton Trane Series R Model RTHC screw chiller. After comparing the costs of both options, Leabo decided to replace the damaged machine.
His relationship with Singer, he said, and the urgency of the situation played a significant part in his decision. "I've dealt with Craig long enough that I believe he'll shoot straight with me. He's very up front and truthful. If he promises to deliver it, it's done. That's built my confidence," Leabo said. Singer immediately contacted Trane's Water Chiller Business Unit in Pueblo, Colo., to learn how quickly a new chiller could be shipped to Wichita. Fortunately, Pueblo had a new machine available, and it could be delivered within a week.
Temporary Chiller Installed
Meanwhile, the building needed cooling, so Singer contacted Trane's ChillerSource Temporary Cooling division to secure a rental air-cooled unit to serve the building until the new chiller was operating. ChillerSource delivered a 200-ton air-cooled chiller, which was quickly connected to the school's chilled water lines using temporary hose connections. This solution saved the school several weeks of discomfort. "It was a lifesaver," Beauchamp said.With the rental RTAA unit cooling the building, much of the pressure was lifted off the shoulders of the Trane service team. Facing a one-month deadline, Beauchamp and Trane service technician Brad David set to work preparing to install the new machine.
They faced a great challenge.
Since the old chiller sat in the center of the building's basement, it had to be disassembled and carted out, while the new machine was disassembled, carted in, and pieced together. Both old and new pieces would have to be lugged across a 100-yard path that included steps, inclines, declines, narrow doorways, and numerous turns.
Removed, Installed In Pieces
"We had a lot of pieces and parts," Beauchamp said of the teardown process. "It was stripped down as far as they had it at the factory." While Beauchamp and David disassembled the new machine, Richard Caywood, vice president of American Mechanical Inc., a mechanical contractor in Wichita, and his team disassembled the old machine and hauled it out."You've got to be creative getting them out," Caywood said. Several doors had to be widened and glass windows removed to get the chillers' barrels in and out of the building. Both crews used a forklift, winches, carts, and rigging techniques to complete the changeover, which lasted a week. Beauchamp said the new chiller was reassembled at the final location in four days.
Leabo said he had not seen anything quite like it. "It was phenomenal, just the amount of work to get the thing in place," he said.
Next, Trane and American Mechanical changed the original piping system that fed the new machine. The old chiller had run inefficiently, partly because of a three-way condenser water valve that had pulled air into the pump, causing it to air lock, Beauchamp said. He fixed the problem by redirecting the condenser water bypass line to the holding basin.
In addition, the new chiller was equipped with an additional condenser water-line valve located at the chiller that is operated by refrigerant pressure differential, Beauchamp said. This regulates the pressure differential between the vessels to ensure proper oil return and chiller operation, a fact that pleases Leabo.
Huge Potential For Savings
"What seemed like a little change is going to be a huge money saver down the road," Leabo said. On a warm June evening less than a month after the procedure had begun, Beauchamp and David started the new machine for the first time. It ran smoothly. "It was a good feeling," Beauchamp said. "You get them off the rental chiller and they're back in normal operation.... I think they have a better operating system than what they had. They're much better off now. It will definitely pay for itself."Leabo said he immediately noticed a difference in the new chiller. "It's much quieter," he said, adding that people on the building's first floor once complained about the old machine's noisy operation. "We have no complaints from them now. That's an added bonus we didn't plan on."
Publication date: 01/05/2004