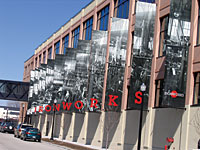
But in recent years, while the quality has remained, problems with delivery and customer satisfaction has caused the company to undergo an extreme makeover - to the point of the company calling itself ‘The New Henry Technologies' and adopting the slogan, "A 91-year-old startup company."
The process began last summer when Hendricks Holdings Co. Inc. announced that it had acquired Henry Technologies and would "aggressively pursue a growth strategy and take advantage of opportunities to expand into new market areas and product line offerings," according to an announcement made at the time of the acquisition.
Hendricks Holding is owned by Ken and Diane Hendricks, who are also CEO and EVP, respectively, of ABC Supply Co., described as the largest wholesale distributor of roofing and siding materials, tools, and supplies in the United States. Through Hendricks Holding, the couple has acquired some 28 manufacturing companies including Henry.
Ken Hendricks himself described Henry as having "products with a Mercedes reputation, but a kind of Yugo business strategy. I saw a real opportunity to take a company that had been a great company and make it great again."
NEW OWNERS
Amfinity Capital, the acquisition arm of Hendricks Holding, engineered the purchase. Amfinity's Kellee Ann Thomas headed the process and then became senior vice president of Henry Technologies, with involvement in the areas of sales and marketing.One of her responsibilities is to assure Henry customers that Ken Hendricks has a "buy/hold approach" to companies he acquires. "Henry was not acquired to be flipped into an IPO (Initial Public Offering)," she said. "The goal is for Henry to be profitable and continue to provide quality products with improved customer service and streamlined manufacturing."
Henry originally was located in Melrose Park, Ill., and for a time had corporate offices in Woodstock, Ill. Corporate operations are now in Beloit, Wis., just across the Illinois state line, where Hendricks Holding and ABC Supply are also headquartered. In fact, the Henry corporate offices are in an old ironworks building that Hendricks purchased and remodeled into office space, as part of major investments he has made in the community over the years. Eleven people work at the Henry corporate office in what is called the International Support Center.

PRODUCTION PHILOSOPHY
Manufacturing continues at a number of locales familiar to the HVACR industry including the Chatham, Ill., plant where some 90 employees are involved in the production of pressure valves and products under the Henry Valve Co. brand name; a plant in Brantford, Ontario, where about 100 employees produce Chil-Con products, heat transfer products, and pressure vessels; and in Glasgow, Scotland, where 60 employees make AC&R Components brand products for the European and Asian markets that are the same types of products made in Chatham for North America.Since Hendricks Holding took over, two other companies have come under the Henry Technologies Inc. banner. This past February, Stainless Tank and Equipment Co. of Beloit was obtained for the production of over the road stainless steel tank and transport trailers. Also that month, GWC Gas-Water Components GmbH & Co. of Stadtlengsfeld, Germany, was acquired for the production of polyethylene ball valves.
That valve is the first of what Henry officials expect to be 10 or more new product introductions in the next year or so, to go along with the already established line of Henry Valve and Chil-Con components.
Charles Graham is executive vice president of operations and oversees both new product development and the operations of the now five Henry plants. He came to Henry with extensive experience in plant operations including tenures with a number of HVACR manufacturers.
He said the new valve with an operating pressure of 24 bar is expected to have a significant impact in the industry because the use of polyethylene means resistance to corrosion, higher elastic capacity than steel, low flow noise, a lighter weight than steel, and competitive costs due to production factors and better ease of installation.
The whole issue of production capabilities at Henry manufacturing sites was a prime part of the equation. Graham said there is a commitment to upgrading plants with state-of-the-art equipment. And a more open and responsive management style has been introduced. Part of the process includes white boards and billboards detailing how the company is doing in a range of categories that can be viewed by all employees. Research and development are also being beefed up, he said.
"We want to be a lean manufacturer," he said. "And we want to design quicker and better."
RE-ESTABLISHING THE PIPELINE
Another significant objective is to do a better job getting existing and new product offerings onto the shelves of wholesalers/distributors and into the specifications of OEMs.Leading that effort is Vince Colorito, director of Global Business Development, who also came aboard last year after a career in the steel and automotive industry.
One of his tasks has been to visit top tier wholesalers to assure a more reliable flow of Henry products as well as work with OEMS on the spec issue.
"There had been a strained relationship with good distributors," he said. "But we've taken steps to get back in sync with the good guys." For the OEMs, he said, "We want to be the best vendor."
He said this re-establishing of rapport is a work in progress, but progress is being made. A key element to the new Henry Technologies is the ability to respond quicker and more efficiently to the needs of those in the supply chain from OEMs to supply houses, to contractors and technicians.
Thomas, Graham, and Colorito pointed out that they operate as a trio of decision makers and that Henry is not bogged down in a heirarchy that could slow down any part of the manufacturing and distribution process.
Said Graham, "The three of us can make ad hoc decisions. We are a business that has flexibility."
Publication date: 05/01/2006