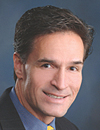
Mike Murphy
However, seized by an arresting development recently, I noticed that many of the new ideas I championed years ago are now quite passé, if not down right stupid in hindsight. Many of them would not even make it to today’s dry erase board - though all ideas in a brainstorming session are good, right?
Good ideas become old ideas, some will stand the test of time, some will not.
A good old idea that seems to be gathering momentum, especially as governmental bodies seek ways to ensure that equipment efficiency promises can be delivered upon, is the idea of installed quality.
IGNORANCE NOT BLISSFUL
Not too many years ago, while joining a table of contractors to discuss “the new realities” of business, one summed up his feelings this way: “Old marketing doesn’t work anymore.” Others around the table used his comment as a springboard for discussion about all that is changing within the industry, the local market, the company.One of the best takeaways for the group was an agreement that in the future the only thing that would matter would be contractor quality. Most concurred that though there are occasional difficulties with product, manufacturers build product to exacting standards. When a consumer might say, “I bought a lemon,” what often has happened is that the customer has purchased a good quality box with a somewhat lacking installation from a company that didn’t know what it was doing.
Ignorance is not a crime nor is it unusual; it is actually rampant in this business as in most service-dependent industries. A case in point from another industry: bad tire wear on an automobile. Most everyone understands what tread wear looks like on over- or under-inflated tires. Some more knowledgeable people may be familiar with other tread wear patterns, and what they may signify. That type of person is usually a tire expert such as a service mechanic who sees tires nearly every day of his/her life, and knows what may be causing specific wear patterns.
Tires from manufacturers are generally of good quality and last a long time with evidence of normal wear. Eventually, tires wear out, and we buy new ones. But improper service procedures can have a very negative impact on tire life. For example, lug nuts that have not been properly tightened can lead to warped rotors in the braking system, improper brake pad wear patterns, and yes, nasty looking tires that don’t live to meet the projected mileage life of the tires.
How about something as simple as rotating the tires at regular intervals? Of course, the customer is more responsible for that maintenance schedule than an automotive dealership or the neighborhood mechanic, but you could liken that to changing filters on a regular basis.
Aside from under- or over-inflating their tires, or never rotating their tires, most consumers don’t usually mess with anything that requires loosening and tightening the lug nuts. Yes, the trusted automotive service technician who doesn’t use a torque wrench properly is messing up a lot of rotors, brakes, and eventually the tires.
SHARING THE BLAME
It would be nice to be able to blame all the short-lived tires on an owner’s failure to rotate their tires. It would be nice to blame short-lived motors on owners who never change their filters. Though there is truth in both, many more problems are due to improper installation and improper service procedures, whether it be automotive or HVAC.So, if you may be interested in changing the world, and creating your own renaissance even if just one job at a time, the quality of your installations can play a huge part in taking an outstanding (or not so outstanding) piece of equipment, and turning it into something quite different.
In other words, there is probably no such thing as a lemon; the fruit of your labor is the lemonade.
MURPHY’S LAW:Under that pile of manure there must be a pony.
Publication date:05/31/2010