Bob and Btu Buddy have met on another job that has a low charge. The season has really gotten hot and units that are not performing are beginning to show up. This unit has a thermostatic expansion valve (TXV). The charge was a little low and it’s not cooling correctly. Bob and Btu Buddy were standing at the outdoor unit talking and Btu Buddy asked Bob, “Just from looking and touching around on the unit, what do you think?”
Bob said, “The suction line is not very cool; the compressor is very warm. I would say that the evaporator is starved for refrigerant. I would suspect a low charge.”
Btu Buddy then said, “Several things can cause the evaporator to be starved. The expansion valve could be out of adjustment. Feel the liquid line and tell me what it feels like.”
Bob held the liquid line in his hand and said, “It is hot. Shouldn’t it be warm instead of hot?”
Btu Buddy explained, “The reason it is hot is because it has no subcooling. There is hot vapor from the condenser circulating in the liquid line. That is a sure sign of low charge. We are at the outdoor unit touching the liquid line. If there were a restriction in the liquid line and it was starving the TXV for refrigerant, the liquid line would be cold just after the restriction. If there were a restriction in the liquid line up next to the TXV, the liquid line leading to it would be warm. There would be a lot of subcooling in the liquid line because refrigerant would be backed up in the condenser.”
Btu Buddy then said, “Let’s go in to the air handler and look for another clue.”
When they got to the air handler, which was in the garage, Btu Buddy said, “Listen to the expansion valve and tell me what you hear.”
Bob said, “It is making a hissing sound.”
Btu Buddy said, “Yes, there is vapor passing through the valve and it doesn’t sound like pure liquid. This is saying that the starved evaporator is coming from not enough liquid in the liquid line.”
Bob then asked, “So the hot liquid line is telling us that the refrigerant charge is low and the hissing TXV is telling us that the starving is coming from the liquid line?”
Btu Buddy said, “Yes, using your hands and your ears to check out a unit is very effective. You can verify what your hands and ears tell you with your instruments. Let’s see if we can find the leak. Turn the unit off and let the pressures equalize from the high-pressure side to the low-pressure side. If the expansion valve prevents them from equalizing, just use your gauge manifold to let them equalize. We need to have good pressure on the low-pressure side of the system in order to properly leak check the unit.”
Bob turned off the unit and did a leak check of the service valve connections and found no leak, so it was good to fasten the gauges to the system.
Bob fastened his gauge manifold to the unit and purged the lines and connected the center line to a cylinder of R-22, the refrigerant in the system. He shut the system off and the pressures did not equalize so he opened the gauge manifold valves and let the pressure move from the high-pressure side to the low-pressure side. The equalized pressure on the system became 133 psig.
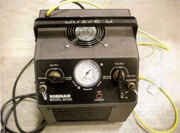
Figure 1. This recovery unit uses no oil and is very handy because it is light and you don’t have to keep oil in the crankcase of its compressor. (Figures are from Refrigeration & Air Conditioning Technology, 5th Edition, by William Whitman, William Johnson, and John Tomczyk, published by Thomson Delmar Learning.)
There was no moisture on the suction line so there was no need to wipe it off before leak checking. He did not discover a leak at the outdoor unit, so he moved to the indoor unit. When he put the leak detector probe into the area around the suction line, the detector showed a leak. He removed the cover from the side of the coil and found that a hole was rubbed in the suction line.
Bob reported to the homeowner that the refrigerant would have to be recovered and the leak repaired.
Bob got set up with his recovery machine (Figure 1) and started removing the refrigerant. While the recovery process was taking place, Bob changed the air filters and oiled the evaporator fan motor and the condenser fan motor. He examined the contactors and found them to be in good shape. He also changed the indoor air filters.
When the refrigerant was removed, he patched the leak using silver solder and repositioned the piping so that it would not rub again. He then pulled a vacuum on the unit and was ready to charge it with refrigerant.
Btu Buddy asked, “How are you going to charge the unit? There are no directions on the unit.”
Bob said, “Let’s use the superheat method like we used on the other system.”
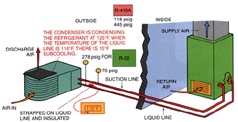
Figure 2. This standard efficiency air conditioner is being charged using the subcooling method. (Click on the image for an enlarged view.)
Bob turned the R-22 cylinder upside down and added liquid refrigerant and, when it stopped flowing, he turned the cylinder upright and closed both valves on his gauge manifold and started the unit.
Btu Buddy said, “Install a temperature tester lead on the liquid line and don’t forget to insulate it so it won’t register the surrounding temperatures. Also, remember that it is only 80°F outside so the condenser air will need to be blocked to simulate a 95° day.”
Bob looked at the head pressure and it was 210 psig, corresponding to an 80° day (80° + 25° approach temperature = 105° condensing temperature). The temperature tester was set up and the liquid line temperature was 100°.
Btu Buddy said, “That is a subcooling of 5° and we have not blocked the condenser yet to get the head pressure up to that of a 95° day.”
Bob blocked the condenser and the head pressure began to rise. He added vapor refrigerant in small amounts in the suction side of the system until the liquid line reading was 110° and the head pressure was 278 psig, corresponding to a condensing temperature of 125°. The subcooling was now 15° (125° condensing temp – 110° liquid line temperature = 15° subcooling).
Bob then asked, “What would happen if there was no subcooling and the liquid line temperature was 125°?”
Btu Buddy said, “The system would operate and cool, just not up to capacity. More importantly than that, the efficiency would not be as good. The customer may never know the difference in the efficiency, but if you left the system like that you would know that you did not give the customer their money’s worth. You are well paid to provide professional service and I know that is what you want to do. You can charge a system to 10° and up to 20° of subcooling and it will be good.”
As Bob was putting away his tools, he said, “You really did show me how to do the right thing. Do you suppose all technicians try to do the job correctly?”
Btu Buddy said, “Many technicians don’t know the difference in getting the correct charge into the system and some don’t care, they are just out for the paycheck. I wouldn’t be helping you if you didn’t want to do the job correctly. It always pays to give the customer the correct value for their money. I will bet you that your mother said something like, “What you hand out is what you will get back,” didn’t she?”
Bob said, “Yes, she always told me, “What goes around comes back around.” I suppose it is the same thing.”
Publication date:07/23/2007