
Temperature and humidity swings caused problems at Angiotech’s plant in Reading, Pa. (above). Disposable scalpels and surgical needles with attached sutures are assembled and packaged at the plant. (Click on the image for an enlarged view.)
He tried dehumidifiers. He tried a large industrial desiccant unit. Balanced dampers? Reduced air pressure? Been there, done that.
Angiotech, a pharmaceutical specialty and medical device manufacturer with more than 1,500 employees worldwide, uses the Reading plant to assemble and package sterile, disposable scalpels and surgical needles with attached sutures. High humidity in the clean rooms could not only encourage bacterial growth, it could prematurely degrade a type of moisture-activated suture that is designed to slowly dissolve in human flesh after the surgical incision heals. Low humidity, on the other hand, promotes static electricity, which interferes with computerized packaging and labeling equipment and gives employees small shocks.
“Temperature and humidity swings were normal,” said Garbini. “Our employees were either too hot or too cold. It was a challenge to maintain the proper temperature while still dehumidifying the space.
“The air-handling compressors were constantly slamming on and off, but the main problem was that I could never get the humidity low enough to stay within our specs, which are more stringent than the federal clean room standards.”
Today, temperature and humidity are holding steady in both Angiotech clean rooms. The solution came in the form of APR Control, a device manufactured by Rawal Devices Inc., of Woburn, Mass.
PLEASED WITH PRODUCT, RESULTS
Garbini learned about the unique control from Bob Reichenbach, service manager for The Warko Group, Angiotech’s local HVAC contractor. In fact, Reichenbach had been recommending the device for years, but Garbini had not found room for one in his budget.Reichenbach told Garbini the control is designed to modulate a direct-expansion air conditioning system’s capacity, “allowing it to dehumidify the space without overcooling it.” Reichenbach said the control varies refrigerant flow according to suction pressure, which changes with the temperature of air crossing the evaporator coil. Because it continuously monitors the heat content of return air, the APR Control is designed to maintain the system in a dehumidifying mode “more efficiently than thermostats and humidistats and without risk of coil icing, liquid slugging, or excessive compressor cycling,” said Reichenbach.
Garbini eventually purchased the control, along with a new air handler for the troublesome clean room, the one where the needles with moisture-activated sutures are packaged. It was installed in late December 2005, when the plant was shut down for the holidays.

The APR Control, shown installed above, was instrumental in stabilizing the humidity in an important clean room at the Angiotech medical specialties plant.
“The APR Control is running great, with no problems at all,” said Garbini. “It made such a significant impact that we installed another one in the air handler for the other clean room in May 2006. Now we’re maintaining humidity and temperature in both rooms well within specs, our employees are more comfortable, and I’ve even seen a decline in the electrical energy consumption.”
To allay any doubts that the improvements from the first installation were due to the control, rather than the brand new air handler, and to demonstrate its effectiveness once and for all, Reichenbach persuaded Rawal Devices Vice President Richard Rawal to donate the second unit. In the end, the results were enough to finally convince Angiotech’s upper management.
Garbini recently ordered a third control for the finishing department, where the needles and blades are polished, cleaned, and washed before going to the clean rooms for assembly and packaging. Though not an official clean room, this area requires frequent air changes, HEPA filtration, and, of course, stable levels of temperature and humidity.
“For new additions to the facility, the APR Control will be designed in from day one - that’s a given,” said Garbini. “I wouldn’t think of installing another air handler without one. I can certainly justify the expense based on the positive benefits that have already been realized.”
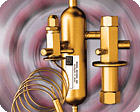
The APR Control, shown above, is designed to allow an air conditioning system to dehumidify without overcooling.
GIVING A/C SYSTEM A BRAIN
No one understands those positive benefits better than Reichenbach, who has more than 30 years of experience in the design and service of HVAC systems. He said installing the control “is like giving your a/c system a brain.”According to Reichenbach, a typical HVAC system is designed for a sunny, 95º day with 95 percent relative humidity. On cooler days, because the system has more capacity than it needs to satisfy the actual load, it tends to cycle on and off. When it shuts off, the humidity increases, causing occupants to feel uncomfortable even when the temperature is within the desired range. Occupants tinkering with the thermostat only make things worse.
Reichenbach said the APR Control improves an HVAC system designed for on/off operation by allowing it to “track” the load - to operate at the same capacity as the load. In other words, a compressor pumps only what it is rated for, but the APR Control “de-rates” the evaporator coil for a reduced load, he said. Reduced compressor cycling means energy savings and less wear and tear on the compressor, he added.
In a system equipped with the control, even if a filter is clogged or a belt malfunctions, coil temperature never falls below freezing, he explained. With no coil icing, the building is spared the water damage often caused by melting coil ice. According to Reichenbach, the control is also ideal for high-percentage (up to 100 percent) make-up air systems, reducing the cycling caused by wide variations in the temperature and humidity of outside air.
“The APR Control corrects a long list of recurring problems and dramatically reduces the number of service calls. This makes for happy customers,” said Reichenbach.
For more information, contact Richard M. Rawal, Rawal Devices Inc., at 800-727-6447 or www.rawal.com.
Publication date:08/13/2007