Bob and Btu Buddy got together for lunch at a place where they could take their time and talk about why high head pressure seems to drive up the power consumption of a compressor. Bob started if off by saying, “I have had several complaints of high power bills, particularly with heat pumps, and have discovered that dirty indoor coils or reduced airflow had driven the head pressure up and the customer discovered it from excess power bills. They then called the company and asked for service. This doesn’t seem to happen in the cooling season, only in the heating season. What is the difference and why is this happening?”
Btu Buddy began the explanation: “The simple and easy answer is to say that a compressor in a system is responsible for raising the pressure in the system from the saturated suction pressure to the saturated discharge pressure. The more that it has to raise the pressure, the more it costs. Now for why.
“Let’s take this one component at a time. An air conditioner has a 40°F boiling temperature for R-22 that creates a suction pressure of about 70 psig, rounded up from 68.5 psig, at design conditions. This is the low-pressure side of the system.
“The condenser normally has a condensing temperature of 125°F that creates a head pressure of 278 psig of head pressure at design conditions. This is considered the high-pressure side of the system.
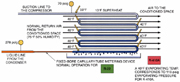
Figure 1. Notice that the suction pressure at the evaporator is 70 psig and the liquid line pressure is 278 psig. The compressor created this pressure difference. (Figures are from Refrigeration & Air Conditioning Technology, 5th Edition, by William Whitman, William Johnson, and John Tomczyk, published by Delmar Cengage Learning.) (Click on the image for an enlarged view.)
Bob said, “This sounds like it could get serious.”
Btu Buddy said, “Yes, it is quite detailed. You remember that we live in an atmosphere of air. Actually, you could say that we live at the bottom of an ocean of air. Air is matter, explained by the fact that it has weight and takes up space. Actually this ocean of air above us creates a pressure at sea level, during standard conditions, of 14.696 pounds per square inch. You notice it when you drive up a mountain; your ears pop. The pressure on the outside of your body becomes less, and your ears pop when the pressures equalize. You will also recall from your technical school days that your manifold gauges read atmospheric pressure as 0 psig. When we start working with the details of compressor lift, we have to take atmospheric pressure into consideration and deal with pounds per square inch absolute (psia). For practical purposes, you just add atmospheric pressure to your gauge reading to get psia.”
“Wow,” said Bob, “fill me in slowly so I don’t get lost.”
Btu Buddy then said, “When engineers talk about how a compressor works with pressure, they use a term called compression ratio. Compression ratio is the absolute discharge pressure divided by the absolute suction pressure. In formula form it would look like this: CR = absolute discharge pressure / absolute suction pressure. This is a ratio of the volume of refrigerant in a cylinder at bottom dead center to the volume of refrigerant in the cylinder at top dead center. The refrigerant volume is compressed from a large volume to a smaller volume.
“Suppose your gauges read design conditions, 278 psig discharge pressure and 70 psig suction pressure. That would mean that:
absolute discharge pressure is 278 + 14.696 = 292.7 psia
absolute suction pressure is 70 + 14.696 = 84.7 psia
“Placing this in the formula:
CR = 292.7 / 84.7 = 3.46:1 ratio of inlet to outlet.
If this were cubic feet, we would have 3.46 cubic feet of refrigerant compressed to 1 cubic foot during the compression process.
“If we raise the discharge pressure to 350 psig + 14.696 / 70 + 14.696 we get a new CR.
CR = 364.7 / 84.7 = 4.3:1 ratio of inlet to outlet.
You can say that enough work was done to compress the volume of refrigerant gas from 4.3 to 1 in this compression process.
“The compression ratio can also be changed by lowering the suction pressure. For example, suppose we lower the suction pressure to 60 psig and keep the same design discharge pressure.
CR = 278 + 14.696 / 60 + 14.696
CR = 292.7 / 74.7
CR = 3.9:1 ratio of inlet to outlet.
If you raise the discharge and lower the suction:
CR = 350 + 14.696 / 60 + 14.696
CR = 364.7 / 74.7
CR = 4.8:1 ratio of inlet to outlet.
“Now, lets look at a heat pump and see what we may get on a cold day. Let’s suppose the head pressure is 210 psig and the suction pressure is 21 psig.
CR = 210 + 14.696 / 21 + 14.696
CR = 224.696 / 35.696
CR = 6.3:1 ratio of inlet to outlet.
That is a lot of conversation that tells you to keep the head pressure as low as practical and keep the suction pressure as high as practical. When either pressure gets out of the design parameters, there will be less efficiency.”
Bob asked, “How does that fit in with today’s practices for service technicians and their service duties?”
Btu Buddy said, “Our job is to keep coils clean, both indoors and outdoors. Now let’s get back to the heat pump that we worked on yesterday that had a dirty coil in the winter. Suppose it had a head pressure of 300 psig and a suction pressure of 21 psig.
CR = 300 + 14.696 / 21. + 14.696
CR = 314.696 / 35.696
CR = 8.8:1 ratio of inlet to outlet.

Figure 2. Notice the size of the evaporator and the condenser. The condenser must reject the heat of compression from the compressor as well as the heat absorbed by the evaporator. (Click on the image for an enlarged view.)
“The job was a heat pump and heat pumps have a little different slant on the problem. Typically an air conditioner condenser is about 25 percent larger than the evaporator because the condenser must eliminate about 25 percent more heat than the evaporator absorbs into the system (Figure 2). This heat is called ‘heat of compression.’ Compression ratios of over 12:1 are prohibitive for compressors because as the compression ratio rises, the discharge gas temperature rises. Oil is always present in discharge gas and oil particles begin to break down at temperatures of over 250°F. These high compressor temperatures are asking for a problem.
“I don’t know if you have noticed, but heat pumps use the same indoor and outdoor sizes as air conditioners.”
Bob then said, “When they reverse the cycle for winter time operation, the condenser area is automatically 25 percent smaller than the evaporator. That can’t be good.”
Btu Buddy said, “It works out that it is good because it is harder to extract heat from the colder outdoor air and the coil really needs to be larger. The indoor coil being smaller is good because it raises the air temperature to the structure. Typically, the supply air from a heat pump is no greater than 100°F. You have been on a service call where the customer complained about drafts. If the outlet air were any cooler, even though it was heating the house, there would be more complaints.”

Figure 3. There is always volume left at the top of the cylinder (clearance volume) in a reciprocating compressor. The refrigerant compressed into this clearance volume will expand when the piston starts back down. No refrigerant will enter the compressor cylinder until the pressure in the cylinder is less than the pressure in the suction line. (Click on the image for an enlarged view.)
Btu Buddy then explained, “The heat pump we were working on yesterday was a reciprocating compressor. High compression ratios are even worse on reciprocating compressors because of the clearance volume at the top of the cylinder on the upstroke of the piston. When a reciprocating compressor piston reaches the top of the stroke, there is a little refrigerant trapped at the top, between the piston and the cylinder head (Figure 3). All reciprocating compressors have this clearance volume so the piston will not hit the cylinder head. When the piston starts down, this tiny bit of gas re-expands in the cylinder on the down stroke. The cylinder cannot start filling until the pressure in the cylinder is less than the pressure on the low side of the system. When the head pressure is higher than normal, there is more than normal refrigerant gas trapped in the clearance volume of the compressor. The compressor efficiency just went down even more than what was caused by the compression ratio.”
Bob said, “Boy, this is really a lot of information.”
Btu Buddy said, “When you buy a huge cup of iced tea in the summer at lunch, you drink it a sip at a time. It is hot outside and you are really thirsty. I bet it takes awhile to drink it all. This is how your education is. You take it a little at a time and over time you really become educated; just like the cup of tea, you keep reaching for the bottom, only with education, there is no bottom. This keeps you interested all of your life.”
Bob then said, “Thank goodness for good resources, such as other technicians, books, and the Internet.”
Publication date:03/24/2008