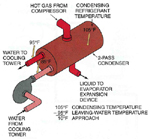
Figure 1-A. A water-cooled condenser. (Figures are from Refrigeration & Air Conditioning Technology, 5th Edition, by William Whitman, William Johnson, and John Tomczyk, published by Delmar Cengage Learning.) (Click on the image for an enlarged view.)
Bob started by asking, “Why would water-cooled equipment be used when a customer could get an air-cooled system that requires much less maintenance?”
Btu Buddy explained, “Both water-cooled and air-cooled systems have their good and bad points. It is probably an equal trade for the small maintenance for air-cooled equipment to the higher efficiency of water-cooled equipment.
Water-cooled systems were the first to be used and were used for a long time before air-cooled systems were developed. Years ago, in the 1940s and 50s, all technicians were very well acquainted with water-cooled systems. Then air-cooled condensers were developed and the big move began towards air-cooled. Energy was cheap and plentiful.
The evaporator absorbs heat into the system and the condenser rejects the heat from the system. Refrigerant is used to move the heat from the indoor evaporator to the outdoors with the condenser. A water-cooled condenser or an air-cooled condenser may be used (Figure 1-A and 1-B).

Figure 1-B. An air-cooled condenser. (Click on the image for an enlarged view.)
Let’s look at the head pressure for a water-cooled condenser. Typically, the water-cooled condenser can condense the refrigerant at about 10° higher than the leaving water temperature, the approach temperature. Most typical water-cooled condensers have a 10° rise across them with 85° water entering and 95° water leaving. This makes the condensing temperature about 105° (95 + 10 = 105) or a head pressure of 211 psig. You can see right away that the lower head pressure is where the savings will come from.
The key to getting the lower condensing temperature is created with the lower water temperature. The lower water temperature is created by the evaporation of some of the water in the cooling tower. A typical water cooling tower can lower the water in the basin to about 7° above the entering air wet bulb temperature. In areas away from the coast where the design wet bulb temperature is 78°, 78° wet bulb + 7° approach temperature = 85° entering water (Figure 2).
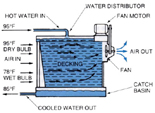
Figure 2. This typical water tower shows the typical entering and leaving water temperature and the tower approach temperature. (Click on the image for an enlarged view.)
Btu Buddy continued, “Air-cooled condensers are fairly easy to maintain. Just clean the coil periodically, keep the fans lubricated, and check any electrical switchgear in the unit.
Water-cooled equipment is another story. Any time water is used, it is subject to different conditions than air. As we mentioned before, water evaporates during the process when a cooling tower is used. Most water has some solid material suspended in it, called minerals. When the water is evaporated, these solids will not evaporate, so they are left behind. You have probably noticed that if you leave a glass of water out on the table until it totally evaporates, there is a film left in the glass. These are the minerals that were in the water. These must be dealt with in water-cooled equipment by means of adequate water treatment and makeup water. Water towers are also great filters for the air that passes through them. All dust, feathers, gum wrappers, and leaves in the air that pass through the tower will settle in the tower basin and may be caught in the sump strainer or the water filter.
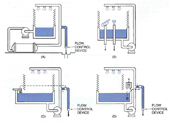
Figure 3. This illustration shows several ways that cooling tower blowdown is accomplished. (Click on the image for an enlarged view.)
Bob then said, “Those tubes didn’t look like they had ever been cleaned.”
Btu Buddy said, “It is possible to go several years without cleaning the tubes, but, as you can imagine, the condenser isn’t getting cleaner by the year. The allowed coating on the tubes is typically 0.0005 of an inch, called the fouling factor, for the condenser to operate at capacity. When you look at a tube with this fouling factor, it looks clean. When the tube is brand new, it will be bright and shiny copper colored. When the tube ages, it will look like an old penny, clean but brown. As tubes begin to build up minerals or foul, the fouling occurs faster and faster because there are minerals for minerals to cling to. All of a sudden, the machine is in real trouble and will trip off because of high head pressure. Meanwhile, the system has been operating at lower and lower efficiency. It pays to keep the tubes clean.”
Bob said, “Those are some good guidelines. How do I, as a technician, start the condenser up in the spring and be assured that it will provide good service all summer.”
Btu Buddy responded, “To start up the system, you should perform the service in two phases for the convenience of the customer.” He then laid out the plan.
“The first phase should be performed during the winter or very early spring:
1. Drain all the water from the condenser circuit and remove the condenser heads and clean the tubes and re-assemble.
2. Turn off the power and oil or grease all fans and pumps.
3. Check all belts on fans and couplings on all pumps.

Figure 4. This photo shows some new contacts compared to worn contacts. (Click on the image for an enlarged view.)
5. Turn the power on to the compressor and control panel to keep the crankcase heat on the compressor during the off-season.
6. Leave a note to fill the tower and condenser circuit and turn the pumps on at startup in case you are forgetful or you may not be the one to start it up again.
7. Clean the tower of all debris and check the fan motors and belts.
8. Clean any water strainers or filters in the system.
The second phase should be performed at startup time:
1. Make sure that crankcase heat is on at the compressor and that the compressor crankcase is warm to the touch. Sometimes management will shut off the heat to save energy. Not a good idea. If the crankcase is not warm, wait until tomorrow to start the compressor. You would be surprised how much liquid refrigerant will be in the compressor if the heat is off.
2. Check the oil level in the compressor crankcase. It should be 1/2 glass. If it is not, get a good light and make sure that you can see oil below the level of the glass. It should then come back up after startup.
3. Make sure the tower is clean and then fill the basin. Set up the recommended water treatment and blowdown.
4. Open the valves and fill the condenser.
5. Start the condenser water pump and make sure you have the correct water flow. There are often water gauges and there should be a correct water pressure drop from the inlet to the outlet.
6. Either use the gauges on the unit or put your own gauges on the unit to monitor the suction and discharge pressure.
7. Place a temperature lead on the compressor suction line and the refrigerant liquid line leaving the condenser.
8. Start the system up and observe the gauges for the correct readings. If the system is R-22, the suction pressure should settle down to about 70 psig when fully loaded and the compressor should pull about full load amps.
9. Observe the entering and leaving water temperature.
10. The compressor should have between 8 and 12° of superheat.
11. The condenser should have about 10 to 15° of subcooling.
12. If the system is a chiller, there will be a water-side to it also. Since the water-side of the chiller is a sealed system, not open like a water tower, you can just check the water treatment and flow rate and be satisfied that it is in good shape.
13. Record the water pressure inlet and outlet.
14. Record the suction pressure and the head pressure.
15. Record the superheat and the subcooling.
16. Record the entering and leaving water temperatures.
17. Record the condenser approach temperature.
18. Leave a copy of the operating conditions in the control panel of the equipment for future reference.
Bob, you have to realize that this is an ideal startup. Many people do not do every step every time. Many owners will not want to pay for a textbook startup. You will often have to use short cuts, such as doing the first phase on the day the unit is put on-line and they will want the system running in a hurry.”
Bob said, “Wow, that is a lot to remember. I can visualize why every step is a great idea. I can also see that management will often times want things in a big hurry.”
Btu Buddy ended by saying, “Always remember that a professional technician learns all of the steps to service procedures and tries to do the best possible under the circumstances.”
Publication date:09/22/2008