Bob was on his way to a new job to handle a service call where the owner said there was not enough heating in one end of an office building.
Bob arrived and talked to the building owner who told Bob that the building was heating really well until a few days ago, and then all of a sudden he started getting calls from some of the office personnel in one end of the building. He and Bob went to the end where the complaints were coming from and, sure enough, it seemed cool.
Bob used a thermometer to verify that it was only 67°F at one end of the building, while it was 72° at the other end.
He then checked the air temperature at some of the air registers in each end of the building. The heating system was a gas furnace and the discharge air temperature was about the same on each end of the building, 130°.

Figure 1. This is a typical duct system with two trunk lines. (Figures are from Refrigeration & Air Conditioning Technology, 5th Edition, by William Whitman, William Johnson, and John Tomczyk, published by Delmar Cengage Learning.) (©Delmar Cengage Learning.) (Click on the image for an enlarged view.)
Bob explained the situation to Btu Buddy.
Btu Buddy then said, “If both ends of the building are getting the same air temperature, what do you think it could be? The building is a ranch style building with two trunk lines (Figure 1).”
Bob then said, “That one end of the building must not be getting enough of the 130° air.”
Btu Buddy then said, “Good thinking. How are you going to prove that and find the problem?”
Bob said, “I am going to check the filters first. Restricted air filters shouldn’t cause uneven airflow, but I am going to check them anyway.”
Bob removed the air filters and found them in good shape. The building owner had changed them recently.
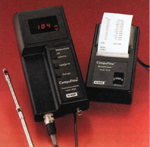
Figure 2. This is an electronic velometer that has a recorder for checking large systems and recording the results for a permanent record. (©Delmar Cengage Learning.)
Bob said, “I am going for my velometer to check the air velocities at some of the air registers (Figure 2).”
Bob went to the end of the building where the rooms were comfortable and read the velocity at several of the supply registers and it showed that the airflow was running about 1,100 feet per minute (fpm).
Bob then said, “That seems a little high and there is some air noise at these registers.”
He then went to the end of the building where the space temperature was too cool and found the velocity to be about 300 fpm. When he discovered this, Btu Buddy said, “Work your way back towards the furnace and see where the velocity picks up and that may give you a clue.”
Bob checked the air velocities back towards the furnace and, at one point, the velocity went back up to over 1,000 fpm.

Figure 3. This is an electronic manometer that measures duct pressures. (©Delmar Cengage Learning.)
Bob drilled several ¼-inch holes along the duct and began to check the air pressures. He found the static pressure to be averaging about 0.05 inches of water column (in. wc) and then all of a sudden in one section it dropped to 0.02 in. wc. Bob then said, “The problem must lie right in this area. Now, what can I do about it?”
Btu Buddy asked, “How is this duct insulated?”
Bob said, “The duct must be lined on the inside since there is no insulation on the outside.”
Btu Buddy then said, “Be glad the duct is in the attic where it is easy to cut an inspection hole.”
Bob turned off the fan and cut out a 1-foot-square hole in the duct between the two different readings and shined his light each way down the duct and saw that a piece of duct liner was laying down in the duct blocking the airflow.
“Now what?” asked Bob.
Btu Buddy said, “It looks like you have two choices. You can just cut out some of the lining or you can take the duct apart and reline that portion of the duct and put it back together.”
Bob then said, “I believe I will ask the owner what he thinks. If I remove some of the liner, I can insulate that portion of the duct on the outside. That would be simple and much less expensive.”
Bob came back from talking to the owner with a plan to remove that small portion of the liner that had fallen down. He removed it, then he screwed a patch over the hole and painted it with mastic, a thick paste product that will dry and seal the edges. He then insulated a portion of the duct on the outside.
When he started to leave, Btu Buddy asked, “What about all of those ¼-inch holes in the duct? They will be blowing conditioned air out in the attic?”
Bob then said, “I was about to forget to plug them. I have a jar full of rubber plugs that are used just for that purpose.”
Bob went to the truck and got some plugs and stopped up the holes, and said, “I am through now, and thanks to your quality control, the job is well done.”
Btu Buddy said, “It is hard to do a job too good.”
Bob asked the owner to turn the system on in one hour to give the mastic time to dry.
Bob then said, “I really don’t understand the pressures in a duct like I think I should. Can you explain that to me in simple terms?”
Btu Buddy said, “I will meet you for lunch tomorrow and we will cover that.”
Publication date:11/23/2009