
Figure 1. This tester can tell the actual capacitance of a capacitor. (Figures are from Refrigeration & Air Conditioning Technology, 5th Edition, by William Whitman, William Johnson, and John Tomczyk, published by Delmar Cengage Learning.) (©Delmar Cengage Learning.)
The day had been very hot and Bob was really tired after spending all day on rooftops working on equipment when he received a call from the dispatcher telling him about a restaurant that was having difficulties. The restaurant expected a big crowd in the dining room that night and the air conditioning was off.
Bob arrived at the restaurant to discover yet another unit on a rooftop that had a problem. Bob checked the thermostat and it was set at 72°F and the room temperature was 80°. Bob turned the thermostat fan switch to fan-on and the fan started. This verified the indoor power supply was working. He then set the thermostat fan switch back to auto and went to the truck for his ladder to go on the roof where the air-cooled condenser was located.
When he got on the roof he noticed that the fan motor was turning, but seemed to be very slow. As he approached the condensing unit, the fan stopped. A few seconds later the compressor shut off because of high pressure.
Bob was sure that the fan capacitor must be the problem, so he turned off the power and removed the old capacitor and went down to the truck for a replacement.
While at the truck, he used his capacitor tester to check the capacitor (Figure 1). He was surprised that it checked out OK. He carried the new capacitor up to the unit anyway and installed it. He started the unit again and the fan was still turning slowly and ran for a few minutes and stopped again. He let the unit sit for a few minutes and placed his clamp-on ammeter on the condenser fan wire and started the unit again. The fan was supposed to draw 6 amps and it was drawing 7 amps. Now the picture was getting clear. Then Btu Buddy appeared and Bob explained what was happening.
Bob asked, “What could be wrong that would cause the motor to draw 7 amps? That is only slightly more than the 6 amps that it is rated at.”
Btu Buddy explained, “The unit is a top discharge fan unit. As this motor moves the air, it is causing a downward thrust on the bearings (Figure 2). I would suspect that the thrust bearing is worn out. This calls for a new fan motor and the supply houses are closed.”
Bob then asked, “What is the difference in the type of wear on a fan that blows out the side?”
Btu Buddy explained, “When a prop type fan is a side discharge, it has a small amount of thrust towards the back of the motor, but most of the wear is on the bottom of the bearing because the fan shaft is laying in the bearing. You might say that the shaft is cradled in the bearing.”
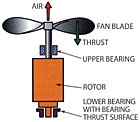
Figure 2. This illustration shows the two bearings that support a vertical condenser fan motor. (©Delmar Cengage Learning.)
Btu Buddy then explained, “All equipment was side discharge in the beginning. As time went on, some people wanted top discharge fans to move the hot air upward. This moved the hot air and the sound upward and allowed you to place units closer together. With the side discharge units, there was always the problem of one unit blowing hot air into another unit unless they were arranged correctly. Side discharge units can also kill shrubbery with the hot air blowing on it. Placing multiple units is easier with top discharge fans. Top discharge fans also must be protected from rain dripping in the motor and leaves and pine needles falling into the unit. That was not a problem with side discharge units. Times and applications change and manufacturers adapt to them.”
Btu Buddy then asked, “What are you going to do now?”
Bob said, “I have a night number for a supply house that is close to this job. I am going to call them and get a fan motor. The owner will have to pay an extra fee for night duty, but under the circumstances, I am sure that will be OK.”
As Bob was going down the ladder, the owner came around the building and Bob explained the situation. The owner said to go ahead because he really needed the dining room to be cool for this evening’s party in that dining room.
Bob met the supply house agent and purchased the fan motor and went back and installed it. The unit started up and ran just as it should. He went into the dining room and made sure the thermostat was set correctly and the owner said, “Thanks, Bob, this really saved the party. It is a party for a really good customer and it would be hard to explain why the air conditioning is not working. They will be here in about an hour and the dining room will be cool by then.”
As they were riding away, Btu Buddy said, “Well, Bob, you now have another very satisfied customer for yourself and your company. Good loyal customers are not easy to get and your company will notice this. It is not easy to work these service calls after-hours and after a hard workday, but you are in the emergency service business. Other peoples’ problems are your income.”
Bob said, “Boy, this has really been a long, hot, and tiring day, but very rewarding.”
Publication date:08/10/2009