Bob’s service call yesterday involved a leaking underground refrigerant piping system. The refrigerant lines were laid in a large plastic pipe which originally had a drain line. The drain had been covered and the refrigerant had leaked out. Since the system did not have a low pressure control, but used the compressor internal overload to monitor when the system ran low on refrigerant, the underground leak probably allowed water to enter the system because the underground sleeve containing the refrigerant lines was full of water. Bob cleared the drain line and let the water drain off and replaced the refrigerant lines. He leak tested the lines and left them yesterday afternoon under 150 psig of pressure. He has now returned to the job the next day to see if the pressure held and to check for moisture in the system.
Bob said to Btu Buddy, “The pressure held at 150 psig, so we know that there are no leaks. We did not install a suction or liquid line drier yesterday because we wanted to try an evacuation first to see if there was any water still in the system. The leak was very small and it is likely that if there was any freestanding water in the system it would be in the suction line that we cut out. Let’s examine that line and see what we see. I had to coil it up to remove it. Let’s turn the coil around and see if any water runs out.”
Bob took the coil of tubing that was still in the equipment room and turned it around and around and no water came out.
Btu Buddy said, “You made a good judgment call yesterday to just put the system under a 150 psig standing pressure check. The pressure test was good and it is likely that there is no water in the system. If there is, it must be very little.”
Bob asked, “What do you think we should do now?”
Btu Buddy said, “Bob, you have made good decisions up to now. What do you think?”
Bob said, “I believe we should purge the system with nitrogen and pull a deep vacuum. If that proves there is no water in the system, we should fill the system with nitrogen up to atmospheric pressure and install a liquid line drier. If there are signs of moisture, we should pull a vacuum until the moisture is boiled out of the system and then install a suction and liquid line drier and pull another vacuum.”
Btu Buddy then asked, “Why wouldn’t you just install the driers now?”
Bob said, “If there is moisture in the system, the driers would just have to be replaced. I am trying to save that step and expense.”
Btu Buddy said, “You are right; it is a gamble. You have no way of knowing if there is moisture in the system until you pull the vacuum. Tell me what vacuum procedure you are going to use.”
Bob explained, “I hear some technicians say that it is not too critical if some moisture is left in the system because the system operates above freezing and the moisture will not freeze in the system. I don’t believe that is good practice because I was taught in school that only two products should be circulating in any system. Those two products are refrigerant and oil. If moisture is left in the system, it is true it won’t freeze and cause a restriction, but moisture does other things to even high temperature refrigeration systems like air conditioning. When moisture is circulated with refrigerant, it contains oxygen and hydrogen. These two chemicals and heat will over time form acids in the system and cause electroplating of the machined parts and can also damage the motor windings. If there is moisture present, the system will not lead its expected healthy life. It will have problems early, like people who don’t take care of their bodies.”
Btu Buddy said, “Boy, that was some speech. You must have really listened in class. You really picked up the correct habits. How are you going to remove any possible moisture from the system?”

Figure 1. This illustration shows a Schrader valve with the core removed. This can be used to more quickly evacuate a system to a deep vacuum. The size or bore of the pipe and tubing has a lot to do with evacuation time. (Figures are from Refrigeration & Air Conditioning Technology, 5th Edition, by William Whitman, William Johnson, and John Tomczyk, published by Delmar Cengage Learning.) (©Delmar Cengage Learning.)
1.Blow the nitrogen out of the system to atmospheric pressure.
2.I am going to remove the Schrader valve cores to give the valve a bigger opening for quicker evacuation (Figure 1).
3.I am going to use my four-valve gauge manifold with copper tubes and a large line for the vacuum connection (Figure 2).
4.I am going to connect my electronic vacuum gauge and let the vacuum pump run and see what happens.”

Figure 2. This gauge manifold uses copper lines for evacuation purposes and a flexible yellow line for adding refrigerant. The copper lines are much more efficient and less likely to leak under a vacuum. Notice that the vacuum pump line is larger copper, 3/8th in. (©Delmar Cengage Learning.)
During lunch, Btu Buddy asked Bob, “What are you going to do if the vacuum pulls down to about 5,000 microns and will not go any further?”
Bob said, “I will know there is moisture in the system for sure. I will look at the vacuum pump oil and see if it is getting milky and change it if needed and keep pulling the vacuum. It would be good if I could apply heat to the system, but the coolest part of the system is going to be the underground piping. Water could boil out of the evaporator section and condense in the underground suction line. It would be very hard to heat that length of pipe. I guess I could use a heat gun (like a super hair drier) to shoot some heat down the pipe. A heat gun is so hot that I would have to keep an eye on the plastic sleeve that the pipe is running through.”
Btu Buddy said, “You are on the right track. Heat would turn any liquid water to a vapor where the vacuum pump could pump it out.”
When they got back from lunch and looked at the micron gauge, Bob was very disappointed. The gauge showed 6,000 microns. The system definitely had water in it and there was no way of knowing how much.
Bob said, “The moisture had to enter the underground suction line and there was no sign of water in the old piping. Since it entered the suction line, it is surely in the compressor and condensing unit. The crankcase heat has been on at the compressor so the oil is hot. The moisture probably moved on to the condenser while the compressor was still running. It may also have moved on to the evaporator where, if it boiled off, it would end up in that underground suction line, just where it will be the hardest to remove. I have an idea. Suppose we stop up the drain to the plastic sleeve and fill the sleeve full of warm water. We know that it doesn’t leak, but it is always risky having a pipe in a vacuum under water.”
Btu Buddy said, “You are right, it is risky, but try it.”
Bob put a plug in the drain line to the piping sleeve. He then used the utility sink in the equipment room to allow warm water into the sleeve and filled it up. He went to look at the vacuum gauge and said, “Would you look at that, the gauge went up to 10,000 microns. We found the moisture. I am going inside and tell the owner that I am going to another job and perform a maintenance contract and will be back in about two hours. The vacuum pump can do its job and I can be off the clock while it is working.”
Btu Buddy said, “It is always best to alert the owner when you leave and tell them when you will be back. They will not be charged for the labor time of just watching a vacuum pump run.”
After the vacuum pump had run for two hours, the micron gauge showed 500 microns. Bob had returned from the maintenance contract call.
Btu Buddy asked, “What are you going to do next?”
Bob explained, “I am going to:
1.Let nitrogen into the system up to about 3 psig.
2.Then I am going to cut in and install a suction and liquid line drier.
3.Then I am going to increase the system pressure to 100 psig and leak test the four connections that I made on the driers.
4.When I am satisfied there is no leak, I am going to pull another vacuum. This one should go very fast because the system is dry and we still have not installed the Schrader valve cores back into the system.
5.When the system reaches a vacuum of less than 500 microns, I am going to close the valve to the vacuum pump and let the vacuum stand with the vacuum pump off to see if the vacuum holds.
6.When I am satisfied that the vacuum is good, I am going to bring the system pressure back up to 3 psig and install the Schrader ports and pull another vacuum to 500 microns. Again, this should happen very quickly because the system is clean and dry.”
Btu Buddy said, “Not only is the system clean and dry, you have fresh suction and liquid line driers. They can stay in the system forever after you charge the refrigerant into it and provide long-term protection.”
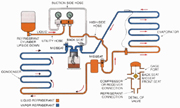
Figure 3. This figure shows liquid refrigerant flowing into a system that has been evacuated. The liquid flows both ways, towards the condenser and towards the evaporator. The liquid refrigerant will stop flowing when the system and the tank pressure equalize, well before the system is overcharged. (©Delmar Cengage Learning.) (Click on the image for an enlarged view.)
Btu Buddy suggested, “You now have a choice as to how to charge the system, vapor or liquid. I would suggest that you charge liquid in through the liquid line port until it stops flowing. By doing this, the liquid will flow towards the condenser and the evaporator, with no chance of any reaching the compressor (Figure 3). When the liquid stops flowing, you can shut off the high side gauge line and start the system and finish charging through the suction side. Since most of the refrigerant went in as a liquid, the refrigerant tank will still have enough pressure to finish the charge.”
Bob did what Btu Buddy suggested and said, “That saves a lot of time rather than charging the entire refrigerant charge with vapor into the suction line.”
Bob finished charging the system and everything was running like it should when the owner showed up and said, “We sure are glad to have the cooling on. That must have been quite a job. I watched you as you worked. There was certainly no slack time and I appreciate getting my money’s worth. You have done a very professional job.”
Bob said, “Thanks, our company insists that its customers get the best that we can offer.”
As they were riding away, Btu Buddy added, “It really makes you feel good when you know that you have done a good job, doesn’t it?”
Bob said, “The owner noticed the work and this system has the best chance it could have to operate for a long time.”
Publication date:10/18/2010