Bob has been sent on a service call where the customer is complaining about her power bill. She thinks that the heat pump may be the problem. Her power bill is much higher than last year and more than the neighbors by a considerable amount. She explained all of this to Bob and he started by asking a question, “Does the auxiliary heat light come on very often on your thermostat?”
She said, “Yes, it is at the end of the season and it is coming on every once in a while.”
Bob then said, “When the thermostat is set and left to control the temperature, the light should only come on when the outdoor temperature drops below about 38°F.”
She said, “No, it is coming on when the temperature is much higher than that.”
Bob said, “I am going to look into the problem.”
Bob got his tools and moved to the outdoor unit and started to fasten his gauges to the unit when Btu Buddy showed up and said, “Why don’t you do some looking around before you fasten the gauges? You know that it is very easy to alter the charge with the gauges and easy to leave a leak behind.”
“What would you suggest that I do without gauges?” asked Bob.
Btu Buddy then turned the question around and asked Bob, “What can cause the unit to use excess power?”
Bob said, “Let me think:
• High head pressure due to stopped up filters or restricted airflow.
• The electric heat coming on every time the compressor runs, or a shorted heating element causing it to operate all of the time.
• A system that is not efficient because of a defective compressor or four-way valve.”
Btu Buddy said, “Let’s take them one at a time. Check the filters and see if there are any registers that are closed off. That will only take a few minutes to eliminate that as a problem.”
Bob checked those items and said, “The airflow seems to be normal. The liquid line would be hot if there were a reduced airflow and it is cool.”
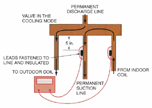
Figure 1. The temperature tester leads are securely fastened to the two suction lines. It is trying to detect if discharge gas is leaking into the suction line. (Figures are from Refrigeration & Air Conditioning Technology, 5th Edition, by William Whitman, William Johnson, and John Tomczyk, published by Delmar Cengage Learning.) (©Delmar Cengage Learning.) (Click on the image for an enlarged view.)
Bob checked this out and said, “The compressor is the only thing operating. I checked all three electric heat elements on both sides of the line. There is no added heat coming from there.”
Btu Buddy then said, “We are down to the refrigeration cycle. We need to determine if it is functioning correctly.”
Bob reached for the gauges again and Btu Buddy said, “Let’s give the four-way valve a temperature difference check before we go to the gauges. Get your temperature tester and fasten the leads as shown in Figure 1.”
Bob fastened the leads and insulated them and said, “The temperature difference between the entering and leaving suction line is 2°. That looks OK.”

Figure 2. This valve is defective because discharge gas is leaking into the suction line. This can cause capacity loss and the system would have to run longer. (©Delmar Cengage Learning.) (Click on the image for an enlarged view.)
Bob said, “I don’t believe this valve is defective.”
Btu Buddy said, “That only leaves us the compressor. How do you think we could check it?”
Bob said, “I can fasten gauges to the system and see what the pressures are running.”
Btu Buddy then said, “That is correct, but let’s do a couple of external checks first and use the gauges to verify our external findings. Check the amperage on the compressor and get a temperature reading of the discharge line.”
Bob checked the amperage and said, “The rated load amps on this compressor is 22 amps and it is only drawing 15 amps. That seems very low. The discharge line temperature is only 140°. I don’t know what it should be, but that seems low.”
Btu Buddy then said, “Let’s fasten the gauges and see what the pressures are running.”
Bob said, “I thought we would never get around to this.”
Btu Buddy said, “I am always hesitant to fasten gauges until necessary. I have seen too many system charges altered when it wasn’t necessary and I have seen too many leaks left behind at service ports. I just practice gauges last, visual and outside tests first.”
Bob fastened the gauges to the system and commented, “These are really funny readings. The suction pressure is 85 psig and the discharge pressure is 160 psig.”
Btu Buddy said, “We have proved the compressor is defective, but just out of curiosity, what should the pressures be.”
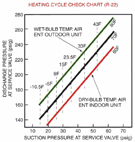
Figure 3. This is an R-22 charging chart for a particular piece of equipment similar to the one in the service call. (©Delmar Cengage Learning.) (Click on the image for an enlarged view.)
Bob found the indoor dry bulb reading to be 70° and the outdoor wet bulb reading to be 33°, and said, “Looks like the suction pressure should be about 45 psig and the discharge pressure about 235 psig. The amperage is low, the suction pressure is high, and the discharge pressure is low.”
“That is correct,” said Btu Buddy. “Can you tell me what the most likely problem is?”
Bob said, “That is more than likely a two-cylinder compressor and I believe that it is only pumping on one of the cylinders.”
Btu Buddy said, “I believe you are right. Can you think of anything that could have caused this?”
Bob said, “This system is several years old. It is very possible that at some time it has had too much refrigerant in the system and the compressor was slugged with liquid. It is also possible that someone has started the compressor up after a long power outage when there was liquid in the crankcase, before the crankcase heat boiled it out.”
Btu Buddy said, “I believe you should question the homeowner about that and see what you can learn.”
Bob talked to the owner and she said, “A few weeks ago, we were out of town and when we returned, the breaker at the outdoor unit was tripped from a storm while we were gone. My husband discovered the breaker had tripped and reset it and he described the unit as having made an awful noise and had a lot of vibration when the unit started up. He started to turn it off when it settled down to run normally.”
Bob explained to her that the damage most likely occurred at that time. He explained that if that should happen in the future, she should shut the unit off at the thermostat, then reset the breaker, and let the unit set for about 24 hours before starting the unit.
Bob set up to change the compressor and, as they were riding away, Btu Buddy said, “You really didn’t need to determine the cause of the failure, but you did the research and got to the bottom of the problem. Systems don’t often just fail; there is usually a reason.”
“That was a simple call when we got all the way through with it, but it had a few twists and turns. Thanks for the help,” Bob said.
Publication date:04/18/2011