Bob and Btu Buddy were on a service call yesterday where the compressor motor was running overloaded due to internal load; the bearings were dragging or worn. The compressor would run for a while and then shut off due to internal overload. Btu Buddy told Bob, “Motor overload protection and circuit protection are subjects that need to be discussed later.” They’ve gotten together today for that discussion.
Btu Buddy said, “Let’s first take motor overload protection. The motor in a system is usually the most used part of the system. It is in constant motion and subject to the most wear. It also is usually the most expensive part in the system, particularly when it is the compressor. These motors turn electrical energy into mechanical energy - work. There is a lot of stress at the motor.”
Bob asked, “Aren’t there several different types of motor?”
Btu Buddy answered, “Yes, and that calls for different types of motor protection. The motors that we are involved with in the residential and light commercial HVACR industry are used to operate fans, pumps, and compressors. These motors are either single phase or three phase and can have a rated voltage of 115V, 208 or 230V, 460V or 600V depending on the application. All of these motors have a rated load amperage (RLA) rating for compressors or for pumps and fans, full load amperage (FLA). This is the maximum allowable amperage for the motor to operate for extended periods of time. The overload protection must protect the motor if it is overloaded for a prescribed length of time. There must be a time factor because all motors start up from a standing or dead still start, which is locked rotor amperage (LRA). LRA will be five to eight times the rated amperage. As the motor begins to turn, this LRA begins to reduce until the motor is up to speed and at its rated amperage.”
Bob said, “Boy, that is a lot to remember.”
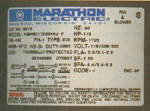
Figure 1. This is the nameplate from a fractional horsepower motor, 1/3 hp. (Figures are from Refrigeration & Air Conditioning Technology, 5th Edition, by William Whitman, William Johnson, and John Tomczyk, published by Delmar Cengage Learning.) (©Delmar Cengage Learning.) (Click on the image for an enlarged view.)
“Now, back to the overload protection. All motors will run overloaded for short periods of time under normal conditions. For example, suppose you repair an air conditioner at a building in very hot weather and the inside gets very hot during the downtime, maybe 85°F, and the outdoor ambient is 100°. The suction pressure and the discharge pressure are going to be very high for the start up and they may remain high for a while until the indoor conditions begin to cool down. The compressor is allowed to run at a slight overload until the system can operate under more normal conditions. For example, if the compressor RLA is 40 amps, and the compressor overload protection were to be set at 40.5 amps, the compressor would not run under the conditions mentioned above, a hot pull down. If the compressor overload protection were to be set at 44 amps, 10 percent above RLA, the compressor would run at a slight overload until the system settled down to more normal conditions. In the case of the 44 amp overload setting, the time delay built into the overload would allow the motor to run at 44 amps for some period of time before tripping.”
Bob then asked, “What is the overload set point of the manufacturers for a typical motor?”
Btu Buddy said, “That is up to the manufacturer or the design engineer. Your job is to see that the motor operates within the rated amperage. If the motor is operating over the rated amperage, it is your job to find out why and correct it.”
Btu Buddy then said, “Let’s talk about different motors and their motor protection:

Figure 2. One of these overloads is embedded in the motor winding and the other is fastened to the motor housing. (©Delmar Cengage Learning.) (Click on the image for an enlarged view.)
2.Larger motors, single and three phase, may have inherent or internal protection. This protection is typically a bi-metal device or devices embedded into the motor winding that will detect heat of the actual motor (Figure 2). The time delay in this overload is the time it takes the bi-metal to heat up and react. Some manufacturers, particularly with larger or more expensive motors, will embed thermistors in the motor windings and use an electronic circuit board to monitor the motor winding temperature.

Figure 3. This is a motor starter and it has the overloads built into the starter. They are removable, so different sizes may be used for the same starter. (©Delmar Cengage Learning.) (Click on the image for an enlarged view.)
Bob then asked, “How does the fuse or circuit breaker fit into motor overload problems?”
Btu Buddy responded, “Fuses and breakers are protection against circuit problem, the wires that furnish power to the various parts of the system. The wiring in a system offers some resistance to the electrical current flow. At a particular amperage, a circuit wire will be at a prescribed temperature. If the current rises, the wire temperature will rise. The National Electrical Code rates wires for their current carrying capacity and temperature rise. For example, a typical number 10 wire is allowed to carry up to 30 amperes of current. If the rating on the unit is 31 amps, you should move up to number 8 wire, which may be rated at 40 amps. The manufacturers help out with sizing the wire. They often use the term ampacity to size the wire. The wire is typically oversized by about 25 percent as a safety factor. The ampacity rating of a unit is about 25 percent over the expected current draw of the unit (Figure 3). This means that the wire is about 25 percent oversized.”
“Doesn’t that cost more?” asked Bob.
Btu Buddy said, “Yes, but it introduces a necessary safety factor. These figures have been worked out through many years of safety concerns and testing. It is the law, so we use them.”
Btu Buddy then said, “Now for protection for the circuit. It must be protected from two things, gradual overload and short circuits to ground or another phase of power. The gradual overload would be when the unit for some reason begins to pull more current. The example in the previous service call would be an example, where the amperage began to rise, but the overload shut the unit down before the circuit protection. The other condition, a short circuit, is much more severe. Without proper protection, the conductors would be glowing red hot.

Figure 4. This is the data sheet for a condensing unit. Be sure to read the fine print. Everything on this sheet says something important to someone. (©Delmar Cengage Learning.) (Click on the image for an enlarged view.)
Bob asked, “How can I remember all of this?”
Btu Buddy said, “Let’s sum up what we have talked about up to now:
1.The motors are typically allowed to run over their rated capacity by some percentage. The overloads protect the motors.
2.The circuit wire size is typically oversized and is sized by ampacity.
3.The circuit is protected by HACR fuses or breakers sized greater than the circuit ampacity.”
Bob said, “Boy, that is a lot to keep straight. The manufacturers are good enough to print all you need to troubleshoot the system on the nameplate. They also furnish the information about the breaker and the ampacity so you can verify the wire size from a wire size chart.”
Btu Buddy says, “You are right, Bob, they try to make it usable for the field technician.”
Publication date:03/21/2011